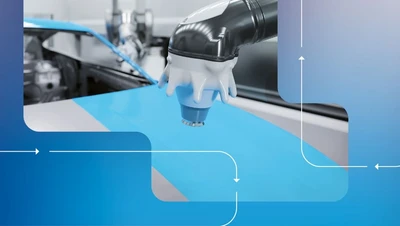
Zukunft in den schönsten Farben
08.04.2025
Lange war sie eine Vision - jetzt wird sie Wirklichkeit: Die Lackieranlage der Zukunft leitet eine neue Ära der Automobilproduktion ein. Starre Systeme weichen Modulen, die flexibel angefahren werden können und dadurch noch effizienter werden. Dazu gehören kompakte Lackierboxen, sparsame Trockner, sekundenschnelle Farbwechsel sowie die Nutzung überschüssiger Wärme.
Wie auf einer Perlenkette reiht sich in den Automobillackieranlagen der Welt eine Arbeitsstation an die nächste. Nach einem strengen Takt sprühen die Roboter Lack auf Karosserien, der dann in Trocknern aushärtet.
Diese starre Logik des Fließbands hat sich über Jahrzehnte bewährt. Sie passt aber nicht mehr in eine Zeit, in der immer mehr Modellvarianten in bestehenden Anlagen gefertigt werden sollen. Zudem drängen neue Wettbewerber auf den Markt und Umweltvorschriften werden strenger. Dürr arbeitet deshalb seit Langem an einem Konzept, das diesem Wandel Rechnung trägt.
Die Lackieranlage der Zukunft begann vor vielen Jahren als Skizze, die Entwickler auf eine Serviette kritzelten, als sie während einer Dienstreise in einem japanischen Café eine Pause machten. Heute wird sie in der Realität gebaut. Ihre hervorstechende Eigenschaft ist Flexibilität. „Sie besteht aus unterschiedlichen Lösungen, die unsere Kunden immer neu auf ihre Bedürfnisse zuschneiden können“, sagt Produktmanagerin Corinna Maier. Die Lackieranlage kann sich ohne Produktionsstopp wechselnden Stückzahlen oder veränderten Modellen anpassen. Der Einsatz effizienter Produkte, innovativer Energieverbundsysteme und intelligenter Software schont außerdem Ressourcen. Eine Auswahl der Komponenten:
< 5 Minuten
Länger steht die Lackierkabine EcoProBooth pro Tag für eine Wartung nicht still. Bei herkömmlichen Lackierkabinen dauert die tägliche Produktionsunterbrechung bis zu zwei Stunden.
Lackierbox erschließt neue Wege
Die Lackieranlage der Zukunft ist ganz anders aufgebaut, als es bisher der Fall war. Statt langen linearen Lackierstraßen enthält sie Lackierboxen, die nebeneinander stehen. Dieses Boxenkonzept spart Platz und macht das Lackieren flexibler.
Die Lackierboxen der aktuellen Generation tragen den Namen EcoProBooth. Sie sind kompakt und mit vier Lackierrobotern ausgestattet, die Außen- und Innenseite der Karosserie in einem Arbeitsgang lackieren können. Bislang waren hierfür drei Lackiertakte nötig.
Zentrale Merkmale der Lackieranlage der Zukunft sind Flexibilität und Modularität. Die traditionelle Lackierstraße ist pausenlos in Betrieb. Mit dem bausteinartigen Boxenkonzept lassen sich einzelne Kabinen vorübergehend stilllegen, wenn weniger Autos bestellt werden. Das senkt die Betriebskosten. Steigt die Nachfrage, kann der Hersteller die Produktion zügig wieder hochfahren. Und wächst die Nachfrage weiter, funktioniert das Szenario auch: „Weitere Lackierboxen können im Handumdrehen aufgestellt werden“, sagt Frank Herre, Leiter der Applikationsentwicklung. Wochenlange Produktionsstopps während eines Umbaus, wie sie in starren Lackierstraßen nötig waren, gibt es nicht mehr.
Die EcoProBooth hat einen weiteren Vorteil: Autohersteller fertigen unterschiedliche Modelle auf derselben Linie. Dabei bestimmen die großen Fahrzeuge, wie lang ein Arbeitsschritt dauert, auch wenn sie nur einen Teil der Produktion ausmachen. Kleine Karosserien lassen sich zwar schneller lackieren, doch sie müssen den Takt der großen mitmachen. Das kostet Zeit. Das neuartige Boxenkonzept erlaubt unterschiedlich lange Takte, da die Karosserie in nur einer Station lackiert und direkt ausgefördert wird. Das nächste Modell kann ohne Verzug nachrücken. Das spart Zeit und erhöht das Produktionsvolumen.
Ein anderes wichtiges Element sind kleine Wartungsfenster in der Lackierkabine. Durch sie lassen sich die Lackzerstäuber der Roboter einfach reinigen oder reparieren, ohne dass die ganze Linie angehalten wird. Nur der verschmutzte Roboter unterbricht die Arbeit und hält seinen Kopf ins Wartungsfenster. Von einer gut belüfteten Zelle aus lasse sich der Zerstäuber reinigen, sagt Produktmanager Daniel Ackermann. „Bislang musste ein Mensch mit Atemschutz die Kabine betreten und brachte womöglich Schmutz mit hinein, der dann auf den frischen Lack gelangte und aufwendig repariert oder herauspoliert werden musste.“ Allein für ihre Reinigung steht eine herkömmliche Lackierkabine durchschnittlich anderthalb bis zwei Stunden pro Tag still. Mit den Wartungsfenstern dauert die tägliche Produktionsunterbrechung keine fünf Minuten.
Weitere Lackierboxen können im Handumdrehen aufgestellt werden.
Frank Herre, Leiter der Applikationsentwicklung bei Dürr
Flexibel fluten und spülen: Vorbehandlung neu gedacht
EcoProWet fügt sich in die Lackieranlage der Zukunft ein
Bevor eine Karosserie ihre farbige Lackschicht erhält, muss sie sich einer Vorbehandlung unterziehen, die aus mehreren Schritten besteht. Sie wird gereinigt, entfettet und gespült, dann folgt der Korrosionsschutz in Form der kathodischen Tauchlackierung.
Die Vorbehandlung ist mit ihren zehn Arbeitsschritten der teuerste Teil des Lackierprozesses. „Wir haben uns deshalb gefragt, wie sich die Prozessschritte flexibler, effizienter und gleichzeitig platzsparend aufbauen lassen“, sagt Produktmanager Klaus Heinsohn.
Die Antwort ist das neue Anlagensystem EcoProWet, das sich in die Lackieranlage der Zukunft einfügt. Anstelle von aneinandergereihten Tauchbecken besteht das System aus einzelnen, nebeneinander angeordneten Behandlungskammern.
Für den Prozess stehen zwei Arten von Kammern zur Verfügung. In Spritzkammern werden die Karosserien mit der für den Prozessschritt vorgesehenen Flüssigkeit besprüht. In Flutkammern werden die Karosserien mit hoher Dynamik gänzlich von Flüssigkeit umspült. „Die Kammern lassen sich optimal auf die Art der Karosserie einstellen“, sagt Heinsohn.
Wird die Produktion ausgeweitet oder findet ein Modellwechsel statt, können Autohersteller das System nach Bedarf erweitern. Das macht den Prozess effizienter und wirtschaftlich nachhaltiger. Die Kunden profitieren von verbesserter Qualität bei gleichzeitig niedrigerem Ressourcenverbrauch.
Der Alleskönner
Damit die Karosserien in derselben Box von innen und außen lackiert werden können, brauchen die Roboter einen besonders variablen Hochleistungszerstäuber. Er muss seinen Sprühstrahl so lenken und dosieren, dass er jede Stelle möglichst schnell und gründlich trifft – aber ohne dass Farbe verschwendet wird.
Diese Fähigkeit bringt die neue Zerstäubergeneration EcoBell4 mit. Sie ist so etwas wie die Königsklasse unter den 120 Dürr-Zerstäubern und kann alle bekannten Automobillacke auftragen. Bei der Entwicklung haben die Fachleute eine Technologie erarbeitet, die sie zum Patent angemeldet haben: „Die Farbe ist in nur vier Sekunden gewechselt“, sagt Entwickler Thomas Buck. Ältere Systeme benötigen für diesen Vorgang zwischen 15 und 25 Sekunden. Bei einer Fabrik, die 60 Fahrzeuge pro Stunde fertigt, ist die Zeitersparnis enorm.
Der Farbwechsel gehört zu den Arbeitsschritten, die besonders schnell gehen müssen. Blitzschnell schießt Spülmittel durch die Düsen des Zerstäubers, bevor die Farbreste mit Druckluft entfernt werden. Dann strömt der neue Lack durch einen eigenen Farbkanal ein.
Neu ist auch die digitale Dokumentation des Lebenszyklus der Zerstäuber über RFID-Technologie. Sie erfasst die Daten der Bauteile, etwa wie lange sie im Einsatz waren, und zeigt die verbliebene Restlebensdauer an. Komponenten lassen sich so rechtzeitig austauschen, was ungeplante Fertigungsunterbrechungen vermeidet.
Eine neue Ära in der Automobilproduktion beginnt
Kompakte Lackierboxen, sparsame Trockner, sekundenschnelle Farbwechsel sowie die Nutzung überschüssiger Wärme. Lassen Sie uns in die Lackieranlage der Zukunft eintauchen und einige Komponenten entdecken.
Querfahrt durch den Trockner
Ist der Lack aufgetragen, muss die Karosserie trocknen. Das geschieht in bis zu 190 Grad heißen Trocknern. Im Vergleich mit konventionellen Lacktrocknern kann der elektrisch betriebene EcoInCure bis zu 70 Prozent Energie einsparen. Nicht nur die Betriebskosten werden damit enorm reduziert. Mit dem Einsatz des EcoInCure lässt sich bei Verwendung von Ökostrom der CO2-Ausstoß der gesamten Lackieranlage um bis zu 40 Prozent senken.
Starke Düsen lenken den Heißluftstrom im Trockner so in und auf die Karosserie, dass sie sich schneller erwärmt. Das spart Zeit, aber auch Platz, weil die Anlage mit der halben Länge und der halben Höhe eines herkömmlichen Trockners auskommt. Anders als bisher bewegen sich die Karosserien quer durch den Trocknertunnel. „Dadurch kann heiße Luft durch die Öffnung für die Windschutzscheibe einströmen und erreicht schwer zugängliche Teile im Innern der Karosserie. Darunter fallen massive Gussteile, sogenannte Gigacastings, oder auch die Tunnelverstärkung“, sagt Produktmanager Heiko Dieter.
Das ist besonders bei Elektroautos von Vorteil. „Wegen ihrer schweren Batterien sind E-Autos unterhalb des Türeinstiegs verstärkt“, erläutert Dieter. Diese sogenannten Schweller sind für herkömmliche Trockner schwer erreichbar. Die intelligent gerichtete Wärmeströmung im EcoInCure erreicht die Klebestellen des Schwellers und härtet diese aus. Das ist wichtig für die Crashsicherheit.
EcoInCure behandelt mit nahezu unveränderter Trockenleistung verschiedenste Karosserien: vom flachen Sportwagen bis hin zum SUV.
Die Lackieranlage der Zukunft besteht aus Lösungen, die Kunden immer neu auf ihre Bedürfnisse zuschneiden können.
Corinna Maier, Produktmanagerin bei Dürr
Im Gespräch mit Corinna Maier und Dietmar Wieland
Die Produktmanagerin und der Forschungs- und Entwicklungsexperte über die Entstehung der Lackieranlage der Zukunft. Ein Out-of-the-Box-Konzept in Boxen gedacht.
Wie ist die Idee der Lackieranlage der Zukunft entstanden?
D.W.: Mit der Idee eines flexiblen, modularen Boxenkonzepts haben wir uns schon vor vielen Jahren beschäftigt. Als sich ein großer deutscher Autohersteller für eine anpassungsfähige und nachhaltige Lackieranlage interessierte, haben wir die Idee in gemeinsamen Workshops validiert. So haben wir für den Kunden die erste modulare Lösung mit dem Boxenkonzept entwickelt – allerdings zunächst nur für eine Lackierkabine, wo der Basislack aufgetragen wird. Mithilfe der gewonnenen Erkenntnisse haben wir das Konzept weiterentwickelt.
Mit welchem Ergebnis?
D.W.: Wir konnten ermitteln, dass flexible Lackierboxen die Kundenbedürfnisse besser erfüllen als eine herkömmliche Linienfertigung. Auch im Hinblick auf die Integration neuer Automodelle in eine bestehende Anlage. Es ist ein immens großer Aufwand mit langen Produktionsstillständen, wenn Hersteller neue Modelle auf alten Lackierstraßen fertigen wollen. Wir haben uns gefragt, wie wir das nachhaltig verbessern können, und kamen dabei auf das Boxenkonzept. Das haben wir im Bereich Forschung und Entwicklung Hand in Hand mit dem Produktmanagement weitergesponnen. Bis daraus schließlich die EcoProBooth entstand.
Corinna Maier: Mit der modularen Lackierbox haben wir bei den Kunden einen Nerv getroffen. Das hat bei Dürr den Ausschlag dafür gegeben, dass wir weitere starr aneinandergereihte Arbeitsschritte in der Lackieranlage aufbrechen wollten. Mit radikalem Umdenken haben wir es geschafft, ein ganz neues Layout für immer wieder wechselnde Anforderungen zu entwickeln.
Corinna Maier arbeitet seit 2012 im Dürr-Konzern. Als Produktmanagerin ist sie für die Lackieranlage der Zukunft und die Nachhaltigkeit von Lackieranlagen verantwortlich.
Dietmar Wieland arbeitet seit 1991 im Dürr-Konzern. Er ist Director im Forschungs- und Entwicklungsteam und verantwortet den Bereich Innovation und Entwicklung der Lackieranlagentechnik.
Wie kann man sich das neue Layout vorstellen?
C.M.: Der Lackierprozess besteht aus rund 120 Arbeitsschritten. Anstatt diese starr an einer Linie entlang aufzureihen, werden die Arbeitsschritte bei der Lackieranlage der Zukunft in kleinere Abschnitte unterteilt. Diese wiederum werden in kompakten Boxen durchgeführt. Denkt man erst einmal in einem modularen Layout, merkt man schnell, wie viel freier sich der Aufbau einer Lackieranlage gestalten lässt. So haben wir nach und nach weitere Produkte und Arbeitsschritte in das Boxenkonzept einbezogen.
D.W.: Die Lackieranlage der Zukunft kreist um die Kerngedanken Produktivität, Nachhaltigkeit, Flexibilität, Modularität und Skalierbarkeit bei gleichbleibend höchster Qualität. Die Anlage ist zu jeder Zeit optimal ausgelastet. Das bedeutet im Umkehrschluss einen geringeren Ressourcenverbrauch: Prozesse laufen parallel ab und sind nicht mehr von der längsten Taktzeit der größten Karosserie abhängig. Für Kunden ergibt sich daraus maximale Flexibilität – ganz egal, welche Größenordnung die Lackieranlage hat: Ob eine große oder eine kleine Produktion, das Konzept ist auf die spezifischen Anforderungen eines jeden Herstellers anpassbar.
Welche Produkte sind in der Lackieranlage der Zukunft noch zu finden?
C.M.: Wir haben zum Beispiel ein zentrales Hochregallager für Karosserien eingebaut. Es dient als Karosseriespeicher und sorgt dafür, dass an jeder Box immer eine Karosserie steht, die als nächste bearbeitet werden kann. Unser flexibles fahrerloses Transportsystem EcoProFleet manövriert die Karosserien zu den entsprechenden Arbeitsplätzen.
D.W.: Außerdem sind das modulare Vorbehandlungssystem EcoProWet, die leistungsfähige Lackzerstäubergeneration EcoBell4, der energiesparende Karosserietrockner EcoInCure sowie das innovative Wärme- und Kälteverbundsystem EcoQPower Teil unserer Lackieranlage der Zukunft.
Lebensadern der Lackieranlage
Da das Lackieren viel Energie verbraucht, arbeitet Dürr laufend an sparsameren Anlagen. Zu den Innovationen gehört das Energieverbundsystem EcoQPower. Es richtet den Blick auf die gesamten Energieströme der Lackieranlage. Mithilfe einer eigens entwickelten Software analysieren Spezialisten den Kälte- und Wärmebedarf der einzelnen Module und vernetzen sie intelligent, sodass nur wenig Energie ungenutzt bleibt.
Was theoretisch klingt, macht das Beispiel der kathodischen Tauchlackierung (KTL) deutlich. In den Tauchbecken wird Lack mithilfe von elektrischem Strom aufgetragen, denn das schützt die Karosserien besonders gut gegen Korrosion. Dabei entsteht Wärme – die bislang mit der Abluft nach draußen ging. EcoQPower macht diese Energie nutzbar: Wärmepumpen entnehmen dem Becken die Wärme und führen sie anderen Prozessschritten zu. In ähnlicher Weise arbeitet das System an weiteren Stellen.
Das intelligente Wärme-Kälte-Verbundsystem ist seit Kurzem erstmalig bei einem Hersteller in Europa in Betrieb. Tests haben ergeben, dass die Fabrik mit EcoQPower über ihren gesamten Lebenszyklus hinweg knapp ein Fünftel der CO2-Emissionen einsparen wird. Die neue Lackieranlage ist damit die erste, die konform mit den Anforderungen der EU-Taxonomie ist, dem Klassifizierungssystem für nachhaltige Wirtschaftstätigkeiten.
Natürlich senkt EcoQPower nicht nur die Emissionen, sondern auch die Kosten. Das ist insbesondere beim Umstieg von Gas auf Grünstrom wichtig. Da Gas in der Regel günstiger ist als Strom, würden durch die Umstellung höhere Betriebskosten anfallen. „Der Anstieg der laufenden Betriebskosten lässt sich durch die Energieeinsparungen von EcoQPower teilweise oder sogar ganz kompensieren“, sagt Produktmanagerin Corinna Maier.
Fachleute von Dürr tüfteln auch an anderen Innovationen, die das System erweitern. Zum Beispiel werden Wärme- und Kältespeicher ergänzt, um Energie zu speichern, wenn Elektrizität günstig bezogen werden kann.
Das würde zu noch mehr Flexibilität führen. Und das ist schließlich das wichtigste Ziel für die Lackieranlage der Zukunft.
21 %
Die mit dem Energieverbundsystem EcoQPower optimierte Lackieranlage ist um rund 21 % energieeffizienter als eine vergleichbare moderne Standardanlage.
- Erfahren Sie mehr über die Idee hinter EcoQPower, die Entwicklung und den Einsatz beim Kunden: → Grünes Nervensystem für die Lackieranlage
- Themen- und generationenübergreifende Zusammenarbeit in der Entwicklung des Lacktrockners EcoInCure: Imke Kuschel und Oliver Iglauer-Angrik sind → Das Trocknerduo
- Mit neuen Technologien ebnet Dürr den Weg zur klimaneutralen Lackierung von Autos: Lernen Sie mehr über den → Greenabler
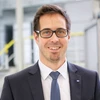
Dr.
Heiko
Dieter
Product Management
Dürr Systems AG
Carl-Benz-Str. 34
74321 Bietigheim-Bissingen
Deutschland
Carl-Benz-Str. 34
74321 Bietigheim-Bissingen
Deutschland
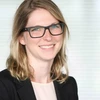
Corinna
Maier
Product Management
Dürr Systems AG
Carl-Benz-Str. 34
74321 Bietigheim-Bissingen
Deutschland
Carl-Benz-Str. 34
74321 Bietigheim-Bissingen
Deutschland