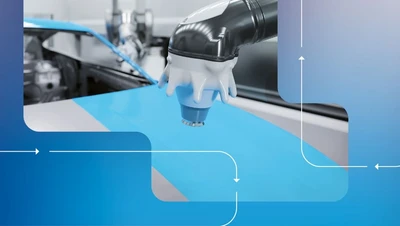
The future is bright and colorful
Apr 8, 2025
For a long time, it was just a vision — now it is becoming a reality: The paint shop of the future is ushering in a new era in automotive production. Rigid systems are giving way to modules that allow for flexible access, making them even more efficient. The paint shop of the future boasts features such as compact painting boxes, energy-saving ovens, instant color changes, and the use of excess heat.
In automotive paint shops around the world, one workstation follows the next like beads on a string. Robots spray paint onto car bodies according to a strict cycle, and the paint is then cured in ovens.
This rigid logic of the assembly line has proven itself over decades. However, it is out of step with a time when more and more model variants need to be produced in existing facilities. In addition, new competitors are entering the market and environmental regulations are becoming more stringent. This is why Dürr has long been working on a concept that addresses this transformation.
The paint shop of the future began many years ago as a sketch that developers scribbled on a napkin while taking a break at a Japanese café on a business trip. Today, it is becoming a reality. Its outstanding feature is its flexibility. “It consists of various solutions that our customers can continually tailor to their needs,” says Product Manager Corinna Maier. The paint shop can adapt to changing quantities or modified models without stopping production. In addition, the use of efficient products, innovative energy network systems, and intelligent software saves resources. These are some of its components:
< 5 minutes
The EcoProBooth paint booth requires no more than this amount of maintenance downtime per day. With conventional paint booths, the daily production stoppage is up to two hours.
Painting box unlocks new possibilities
The paint shop of the future is designed very differently from the way it has been up to now. Instead of long, linear painting lines, it features painting boxes arranged side by side. This box concept saves space and makes painting more flexible.
The painting boxes of the current generation are called EcoProBooth. They are compact and equipped with four painting robots that can paint both the exterior and interior of the car body in a single operation. Until now, this has required three painting cycles.
The paint shop of the future boasts flexibility and modularity as its key features. The traditional painting line operates continuously. With the modular box concept, individual booths can be temporarily shut down when fewer cars are ordered. This lowers operating costs. If demand increases, the manufacturer can quickly ramp up production again. And if demand continues to grow, the scenario still works: “Additional painting boxes can be set up in no time at all,” says Frank Herre, Head of Application Development. Modifications no longer result in week-long production downtime, as was necessary with rigid painting lines.
The EcoProBooth has another advantage: Automakers produce different models on the same line, with larger vehicles determining the duration of each work stage, even if they only account for a portion of the production. Even though small car bodies can be painted more quickly, they have to follow the pace of the larger ones. This takes time. The innovative box concept allows for varying cycle times, as the car body is painted in just one station and immediately moved out. The next model can follow without delay. This saves time and increases production volume.
Another important element is the inclusion of small maintenance windows in the paint booth. They allow the robots’ paint atomizers to be easily cleaned or repaired without stopping the entire line. Only the dirty robot interrupts its work and places its head into the maintenance window. The atomizer can be cleaned from a well-ventilated cell, according to Product Manager Daniel Ackermann. “Until now, a worker wearing respiratory protection has had to enter the booth, perhaps bringing in contaminants that landed on the fresh paint and had to be laboriously repaired or polished out.” A conventional paint booth remains idle for an average of one-and-a-half to two hours per day just for cleaning. With the maintenance windows, the daily production downtime lasts less than five minutes.
Additional painting boxes can be set up in no time at all.
Frank Herre, Head of Application Development at Dürr
Flexible flooding and rinsing: A new approach to pretreatment
EcoProWet integrates into the paint shop of the future
Before a car body receives its colored paint coat, it must undergo a pretreatment process consisting of several steps. It is cleaned, degreased, and rinsed, followed by corrosion protection in the form of cathodic dip coating.
With its ten steps, pretreatment is the most expensive part of the painting process. “We therefore asked ourselves how the process stages could be designed in a more flexible, efficient, and space-saving way,” says Product Manager Klaus Heinsohn.
The answer is the new EcoProWet system, which integrates into the paint shop of the future. Instead of dip tanks arranged in a row, the system consists of individual treatment chambers positioned side by side.
Two types of chambers are available for the process. In the spray chamber, the car bodies are sprayed with the liquid designated for the specific process stage. In the flood chamber, the car bodies are completely immersed in liquid flowing at high speed. “The chambers can be optimally adjusted to the type of car body,” says Heinsohn.
If production is scaled up or a model change occurs, automakers can expand the system as required. This makes the process more efficient and economically sustainable. Customers benefit from enhanced quality while reducing resource consumption at the same time.
The all-rounder
To enable car bodies to be painted both inside and out in the same booth, robots need a particularly versatile high-performance atomizer. It must direct and regulate its spray jet in such a way that it covers every area as quickly and thoroughly as possible — without wasting any paint.
This capability is provided by the new generation of atomizers, EcoBell4. It could be described as the premier class among Dürr’s 120 atomizers and can apply all known automotive paints. During its development, experts devised a technology for which they have filed a patent: “A color change takes just four seconds," says developer Thomas Buck. Older systems require between 15 and 25 seconds for this process. In a factory that produces 60 vehicles per hour, the time saved is considerable.
The color change is one of the work stages that need to be completed with particular speed. Rinsing agent shoots through the nozzles of the atomizer at lightning speed before the paint residue is removed with compressed air. The new paint then flows in through a separate paint channel.
Another new feature is the digital documentation of the atomizers’ life cycle using RFID technology. It records the data of the components, e.g. how long they have been in use, and displays the remaining service life. This allows components to be replaced in good time, which avoids unplanned production downtime.
A new era in automotive production begins
Compact painting boxes, energy-saving ovens, instant color changes, and the use of excess heat. Let's zoom into the paint shop of the future and reveal some of its components.
A transverse journey through the oven
Once the paint has been applied, the car body needs to dry. This takes place in ovens heated up to 190 degrees Celsius. Compared to conventional ovens, the electrically powered EcoInCure can reduce energy consumption by up to 70 percent. This not only leads to a significant reduction in operating costs. The EcoInCure can lower the CO2 emissions of the entire paint shop by up to 40 percent when using green electricity.
Powerful nozzles direct the hot air flow in the oven into and onto the car body, allowing it to heat up faster. This saves both time and space, as the system requires only half the length and height of a conventional oven. Unlike before, the car bodies pass through the oven tunnel transversely. “This allows hot air to flow through the windshield opening and reach areas inside the car body that are difficult to access. These include massive cast parts, known as gigacastings, as well as the tunnel reinforcement,” says Product Manager Heiko Dieter.
This is particularly advantageous for electric cars. “Due to their heavy batteries, electric cars are reinforced below the door sills,” explains Dieter. These so-called rocker panels are difficult to access for conventional ovens. The intelligently targeted heat flow in the EcoInCure reaches the adhesive joints of the rocker panel and cures them. This is important for crash safety.
The EcoInCure processes a wide range of car bodies with virtually unchanged drying performance: from sleek sports cars to SUVs.
The paint shop of the future consists of solutions that customers can continually tailor to their needs.
Corinna Maier, Product Manager at Dürr
A conversation with Corinna Maier and Dietmar Wieland
The product manager and the research and development expert discuss how the paint shop of the future was created. An out-of-the-box concept based on boxes.
How did the idea of the paint shop of the future come about?
Dietmar Wieland: We started exploring the idea of a flexible, modular box concept many years ago. When a major German car manufacturer expressed interest in an adaptable and sustainable paint shop, we validated the idea in joint workshops. We thus developed the first modular box-concept solution for the customer — but initially only for a paint booth where the base coat is applied. We used the knowledge we gained to develop the concept further.
What was the outcome?
D.W.: We found that flexible painting boxes meet customer needs better than conventional line production. This also applies when integrating new car models into an existing plant. It takes an immense amount of effort, along with long production downtimes, when manufacturers want to produce new models on old painting lines. We asked ourselves how we could improve this sustainably and came up with the box concept. We continued to explore this in the research and development department, in close cooperation with product management. This ultimately led to the creation of the EcoProBooth.
Corinna Maier: With the modular painting box, we struck a chord with our customers. This was the crucial factor that prompted us at Dürr to break up other rigidly sequenced work stages in the paint shop. With a radically different approach, we managed to develop a completely new layout to meet ever-changing requirements.
Corinna Maier has been working for the Dürr Group since 2012. As Product Manager, she is responsible for the paint shop of the future and the sustainability of paint shops.
Dietmar Wieland has been working for the Dürr Group since 1991. He is director in the research and development department, responsible for innovation and development of paint shop technology.
What does the new layout look like?
C.M.: The painting process consists of around 120 work stages. Instead of arranging these rigidly along a production line, the paint shop of the future divides the work stages into smaller sections. These, in turn, are carried out in compact boxes. Once you start thinking in terms of a modular layout, you quickly realize how much more flexible the design of a paint shop can be. We have thus gradually incorporated additional products and work stages into the box concept.
D.W.: The paint shop of the future revolves around the core ideas of productivity, sustainability, flexibility, modularity, and scalability, while maintaining the highest level of quality. The plant is optimally utilized at all times. Conversely, this means lower resource consumption: Processes run in parallel and are no longer dependent on the longest cycle time of the largest car body. This results in maximum flexibility for customers — regardless of the size of the paint shop: Whether for large or small production volumes, the concept can be adapted to the specific requirements of each manufacturer.
What other products can be found in the paint shop of the future?
C.M.: One example is a central high-bay warehouse for car bodies. It serves as a car body storage system and ensures that there is always a car body at each box, ready to be processed next. Our flexible, automated guided vehicles, EcoProFleet, maneuver the car bodies to the corresponding workstations.
D.W.: Our paint shop of the future also includes the EcoProWet modular pretreatment system, the high-performance EcoBell4 generation of paint atomizers, the energy-saving EcoInCure car body oven, and the innovative EcoQPower combined heating and cooling system.
The lifelines of a paint shop
Since painting consumes a lot of energy, Dürr is continuously working on more efficient systems. One of its innovations is the EcoQPower energy network system. It focuses on the entire energy flows of the paint shop. With the help of specially developed software, specialists analyze the cooling and heating requirements of the individual modules and network them intelligently, ensuring that very little energy remains unused.
This theoretical concept is illustrated by the example of cathodic dip coating (CDC). In the dip tank, paint is applied using an electric current, as this protects the car body particularly well against corrosion. This process generates heat, which has until now escaped with the exhaust air. EcoQPower makes this energy usable: Heat pumps extract the heat from the tank and redirect it to other process stages. The system operates in a similar way in other areas.
The intelligent combined heating and cooling system has recently been put into operation for the first time by a manufacturer in Europe. Tests have shown that the factory equipped with EcoQPower will cut CO2 emissions by almost a fifth over its entire life cycle. The new paint shop is therefore the first to comply with the requirements of the EU Taxonomy, the classification system for sustainable economic activities.
Of course, EcoQPower not only lowers emissions, but also cuts costs. This is particularly important when switching from gas to green electricity. Since gas is generally cheaper than electricity, switching would lead to higher operating costs. “The increase in ongoing operating costs can be partially or even fully offset by the energy savings of EcoQPower,” says Product Manager Corinna Maier.
Dürr experts are working on further innovations to expand the system. For example, heat and cold storage systems are being added to store energy when electricity can be sourced at a low cost.
This would lead to even more flexibility. And that is ultimately the most important goal for the paint shop of the future.
21%
The paint shop optimized with the EcoQPower energy network system is around 21% more energy efficient than a comparable modern standard paint shop.
More about
- Learn more about the idea behind EcoQPower, its development, and its use by customers: → A green nervous system for the paint shop
- Meet Imke Kuschel and Oliver Iglauer-Angrik who work together on the paint curing oven EcoInCure — from different angles: → Teamwork is the cure
- Dürr is paving the way for the climate-neutral painting of cars — meet the → Greenabler
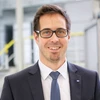
Dr.
Heiko
Dieter
Product Management
Dürr Systems AG
Carl-Benz-Str. 34
74321 Bietigheim-Bissingen
Germany
Carl-Benz-Str. 34
74321 Bietigheim-Bissingen
Germany
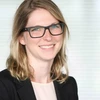
Corinna
Maier
Product Management
Dürr Systems AG
Carl-Benz-Str. 34
74321 Bietigheim-Bissingen
Germany
Carl-Benz-Str. 34
74321 Bietigheim-Bissingen
Germany