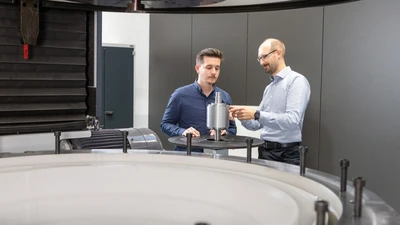
Spun, not stirred
Apr 8, 2025
E-cars, energy storage systems, or electric flight — efficient and reliable rotors are key to the technologies of the future. At the new Green Technology Center of the Group’s subsidiary Schenck RoTec in the German city of Darmstadt, everything revolves around sustainability.
The rotor spins faster and faster in the spin test system. At first, everything runs smoothly. But suddenly, a small crack forms on its outer surface. Just a moment later, it bursts into pieces. “We can push every rotor to its load limit,” says Matthias Hartnagel with a grin. He heads up the Technical Consulting team. The test results are not always as spectacular as the ones captured by a high-speed camera in this particular case. Sometimes, the rotors simply deform. But even the slightest deformation can be meticulously examined in the specially equipped measuring room of the new Green Technology Center.
Under the motto “Enabling sustainable rotating technology,” everything here revolves around sustainability. After all, reliable rotors are crucial for the future. This does not just apply to innovative motors in e-mobility, where the new generation of rotors requires much more performance and less weight than before. Rotors also play a major role in energy storage systems and hydrogen compressors. In addition, there are new rotors from the aerospace industry, such as those used for electric flight. And they all need to be tested.
“The demand for our services has grown steadily in recent years,” says Hartnagel. “To meet the demand, we have set up several new spin test systems. At the time, however, they were being installed across the site, wherever there was space and the environmental conditions were right. At some point, it became clear that this was very inefficient due to the long distances.” As there were also plans to expand the measuring room as part of the certification center, the idea arose to combine both services within one building.
After around two years of planning how to make a 1960s factory building suitable for the new purposes, plus a further year of construction, the Green Technology Center opened in July 2024. The bright space with wooden cladding looks friendly and welcoming. “We wanted to create a certain showroom character while also meeting the stringent requirements of information security. Here, first-class service is provided in a pleasant working atmosphere," says Project Manager Marcel Uhl.
We can push every rotor to its load limit.
Matthias Hartnagel, Head of Technical Consulting at Schenck RoTec
Colleagues roll up their sleeves
The planning and construction of the building were conceived by a project team consisting of five Schenck employees and an architect. Depending on requirements, specialists for shell and drywall construction as well as for heating, ventilation, and sanitation (HVAC), plus electricians, painters, or carpenters were brought in. Coordinating the various trades required a lot of communication and sometimes mediation. Another challenge was minimizing downtime caused by the construction and relocation. For the project team, the work was largely uncharted territory, where the members essentially became builders themselves. “We’ve all become HVAC specialists, as it were,” laughs Melanie Wahl. As head of the certification center and the measuring room, she was part of the project team.
The ambitious schedule was constantly challenged by unforeseen events that required a rethink. One such surprise was the discovery of old foundations beneath the existing factory floor that nobody knew about beforehand. However, the effort paid off. “It was a great opportunity to create optimal working conditions. We were able to design the building according to our needs," recalls Hartnagel. “This inspired us to invest such a lot of energy.”
The building is divided into two halves, with one side housing the four spin test systems. This is where rotors weighing up to 400 kilograms can be tested and speeds of up to 250,000 revolutions per minute can be achieved by using various gearboxes. All spin test systems are placed on their own foundations, which can absorb the immense forces generated during a burst. On the other side, there are four balancing machines designed to correct any unbalance directly on site, along with the certification center and integrated measuring room equipped with three high-precision coordinate measuring machines.
IT'S EVERY µ THAT COUNTS
“We look at the µ, i.e. the thousandth of a millimeter,” says Wahl. Since even slight temperature differences, among other factors, can influence the measurement results, it takes time to bring the parts to be tested to the right temperature. This is done in advance in a specially equipped room. As a result, the parts already have the required standard temperature when they arrive in the measuring room. To protect against external vibrations, which could also distort measurement results, the measuring room's foundation is decoupled from its surroundings.
The spin testing service and the certification center are two separate areas of work that sometimes serve different customers. While rotors are spinning on the left side of the building, the right side is used to test customers’ working standards for balancing technology, such as rotors and test masses. “To a certain extent, our work at the certification center is comparable with technical inspections carried out on vehicles. Every car undergoes regular checks of all function-critical features to ensure, for instance, whether the brakes and steering are working properly and the vehicle's emission levels comply with prescribed standards. The inspection seal confirms that the car is roadworthy. What we do here is quite comparable,” explains Melanie Wahl. Traceable testing is used to verify whether the rotors and balancing machines comply with internationally recognized metrology norms and standards. Testing covers geometry, mass, and the measurement variable of unbalance — a unique selling point for Schenck RoTec that is unmatched worldwide. This reassures the customers that all function-critical features of their machine and the associated working standards are in good condition.
Of course, there are also overlaps with the spinning processes. “After our colleagues have conducted the spin test, the rotors often come to our work area so we can examine them for geometric deformations that may have been caused by the spinning,” explains Wahl.
Discretion is a top priority throughout the Green Technology Center. The bays of the spin test systems are equipped with film-coated glass panels to prevent outside visibility while still letting in plenty of light. Curtains can be drawn in the measuring room. On arrival, rotors are immediately moved to a protected area. This ensures that only individuals who are directly involved know about the work being carried out, as prototypes are often handled there.
Once we have gained a customer, they usually stay with us.
Marcel Uhl, Project Manager at Schenck RoTec
Test, test, and test again
Supporting customers to achieve progress in developing a product — that's what fascinates Marcel Uhl. “We often receive the first version of a rotor for testing. The customer then improves this version using our data. Afterward, we receive the modified version and test it again. If we find that the enhanced rotor can handle 50 percent more speed, for example, that's a great sense of achievement.”
The entire process can take months — until the customer is satisfied. “Eventually, there are no more prototypes, but a product ready for series production,” says Uhl. But even this needs to be tested, especially for its durability. “To demonstrate that the product will last for years and more, it is repeatedly accelerated to maximum speed and then decelerated. This typically happens 50,000 times, up to 14 days straight."
Uhl sees technical consulting as one of Schenck RoTec's strengths. "We don’t just run tests, but we work with the customer to figure out what the real challenges are. Our ideas help to create added value," he says. According to Uhl, clarifying the technical details together with the customer and determining the correct sequence of tests is the most time-consuming part. But it pays off, as he points out: “Once we have gained a customer, they usually stay with us.”
We look at the µ, the thousandth of a millimeter.
Melanie Wahl, Head of the Certification Center at Schenck RoTec
More about
- The Dürr Group’s subsidiary Schenck facilitates connecting balancing machines to the cloud: → Finding the right balance
- In the Green Technology Center, Schenck offers services relating to the development and production of rotors: → Green Technology Center opened
- Rotors are an essential component for a motor to work - experts at Schenck RoTec test them in their spin test systems with a special → Stress test

Holger
Mayer
Global Director Digital and Marketing
Schenck RoTec GmbH
Landwehrstr. 55
64293 Darmstadt
Germany
Landwehrstr. 55
64293 Darmstadt
Germany