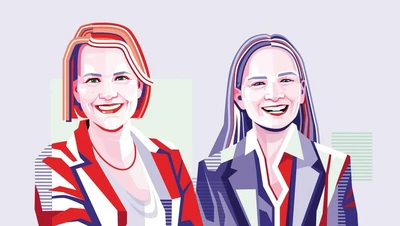
Heading toward true north
Apr 8, 2025
The best information is not to be found at the desk, but in the coffee kitchen. This is where we meet Kathrin Sitzler and Isabella Jochum. The two work as Lean Consultants in the area of Corporate Process Excellence. We want to know what is behind this unusual professional designation.
What do you do as a Lean Consultant?
Kathrin Sitzler: Our main task is to establish a culture of continuous improvement within the company. We work for all areas of the Group, from Dürr to HOMAG to Schenck.
Isabella Jochum: Our projects are all about streamlining processes. To achieve this, we work with a variety of lean management methods. These aim to identify and analyze problems and develop solutions together with the employees.
Can you very briefly explain such a method?
I.J.: One example is the Shop Floor Management. “Shop floor” essentially means “workshop”. The method originally comes from the area of production. Roughly speaking, it’s about having managers in close proximity to their employees — both in production and in the office. This streamlines communication and improves collaboration. If there is a problem of major significance, it has to be presented to the Board of Management within half a day. But the information chain from team leaders to the management floor only works if there is always someone acting in a leadership role at each level.
Is the Dürr Group not sufficiently streamlined?
K.S.: Lean management and its methods aim to make improvement in small steps. We aspire to be a company with which all customers are 100 percent satisfied, in which nothing is wasted, and in which everyone works in line with the strategy. Realistically, of course, we will never achieve this in its entirety. But these goals are our True North, i.e. the central guiding principle by which we orient ourselves.
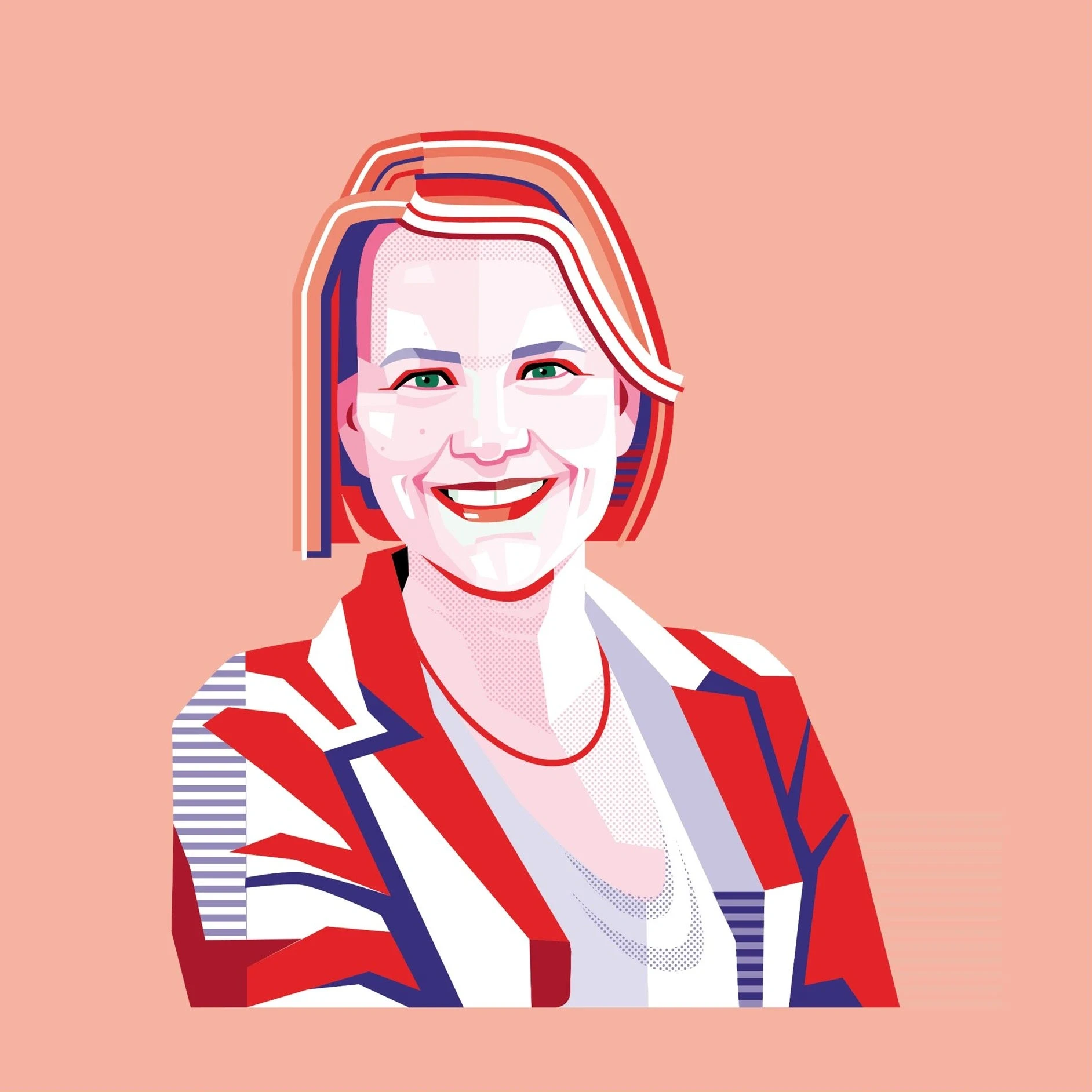
What could this look like in operational practice?
I.J.: One example is the precise definition of processes. For instance, I took a holistic look at the process of repairing products together with employees from the service department and we coordinated all the steps efficiently. Thanks to the revised process, we will be able to act faster and with improved quality for customers in the future.
What does your day-to-day work look like?
K.S.: In addition to my tasks as a team leader, I also work on projects. For example, we train colleagues to spread the culture of lean management in their environment. These are our so-called multipliers.
I.J.: I give Lean workshops and I lead improvement projects. All optimizations of various kinds are aimed at increasing efficiency.
Where did you last accompany an improvement?
I.J.: I was recently involved in a project aimed at improving the ability to track the whereabouts of production accessories. This refers to transport racks or screwdrivers, for example. Their storage locations are often unclear. The solution was to record the production accessories centrally in the SAP system right from the outset. This makes it much easier to find them later.
What are the areas in which you are active?
K.S.: Throughout the Group, both in Germany and worldwide. In the past few years, we have trained multipliers in Mexico and Italy, among other countries. We are currently planning a Lean training program in Germany. We interact with many different people and cultures. No two projects are the same. There is hardly any routine. I like that very much.
What is “Lean Management”?
The main objective of lean management is to make processes in the company more efficient. It takes into account activities along the entire value chain. “Lean management” is designed to create a holistic system with the best possible quality in which waste is minimized.
Continuous improvements are achieved through a variety of methods, mindsets, and tools — across all areas of the company.
How do your projects come about? Are you sent to certain areas of the Group?
K.S.: Most of the time, we are approached by managers with requests for specific topics. But I can also remember a project where an employee pointed out a weakness in the procedures. His concerns found their way into the divisional management meeting. From there, an improvement process was initiated, which we successfully completed together with our colleagues.
How open are the participants to what you are proposing?
I.J.: Most of them are very open. It is important that people trust us. That is why we apply the “Las Vegas rule”: What happens in Vegas stays in Vegas. This means that nothing confidential leaves the room. Participants should be able to address uncomfortable issues and talk openly with each other.
And does that work?
K.S.: Pretty much always. My experience is that after each of our projects, people are a little closer to each other than before.
Thank you very much for the interview!
More about
- Meet Laura Manske, scrum master at Schenck RoTec, for a coffee in the break room: → What does a scrum master do?
- Meet Dürr project manager Kassem Chaou for a coffee in the break room: → Right on the mark
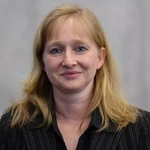
Martina
Bausch
Officer Online Magazine
Corporate Communications & Investor Relations
Dürr Aktiengesellschaft
Carl-Benz-Str. 34
74321 Bietigheim-Bissingen
Germany
Carl-Benz-Str. 34
74321 Bietigheim-Bissingen
Germany