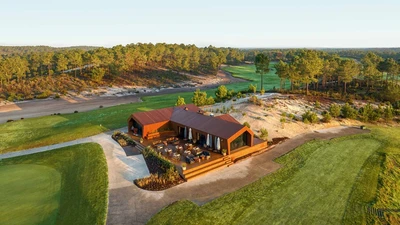
Timber construction without limits
Apr 8, 2025
The Portuguese company Kozowood focuses on the trend toward timber construction in its home country. It has equipped its two new production lines with HOMAG machines and systems. The ambitious project is made possible through the close collaboration of HOMAG subsidiaries from Denmark and Germany.
Kozowood showcases its expertise an hour and a half's drive south of Lisbon. There, in Comporta, you will find white beaches, clear water, and lush meadows. In this area, Kozowood is working with a major real estate company to build high-quality timber houses — architectural masterpieces that blend harmoniously into their natural surroundings. Moreover, the company consciously focuses on the ecological and economic advantages that timber offers.
Not long ago, the company primarily focused on building with concrete. The global trend toward sustainability has prompted it to rethink its business model. In Portugal, where industrialized timber construction is still the exception, the major investment in the industrialization of prefabrication makes Kozowood a pioneer.
Wood is a climate-friendly building material, provided that new trees are planted to replace those that have been felled. Unlike concrete, wood absorbs carbon dioxide from the atmosphere — one cubic meter of wood binds around one ton of carbon dioxide. In buildings, this natural material can last for centuries, thus serving as a carbon store.
Thanks to our broad product portfolio and the advanced technologies, we were able to tailor the project precisely to Kozowood's needs.
Marco André Silva, Head of Sales HOMAG in Portugal
Building a house in just three weeks
Going forward, Kozowood aims to build not only customized villas but also modern single- and multi-family houses made of wood in series production — both in Portugal and abroad. The company is therefore investing a significant sum in the heavily forested north of the country. Near the town of Esposende, around 360 kilometers north of Lisbon, Kozowood is building two new production lines. These will be used to produce wall, ceiling, and roof elements that can be assembled into a building on site in record time. The required machines and systems come from three HOMAG subsidiaries in Germany and Denmark.
The two Danish manufacturers Kallesoe and System TM have been part of the HOMAG Group for a few years now. In close collaboration with the German subsidiary WEINMANN, they were involved in the project in Portugal that was implemented across three countries. “Thanks to our broad product portfolio and the advanced technologies, we were able to tailor the project precisely to Kozowood's needs,” says Marco André Silva, HOMAG's Head of Sales in Portugal.
Framed for success
The project includes a production line for timber frame construction, supplied by WEINMANN. It produces wall and ceiling elements, which form the skeleton of a building. “This construction method is particularly suitable for low- to mid-rise residential buildings, such as detached houses and apartment buildings,” explains Ingemar Bauersfeld, Sales Manager at WEINMANN.
How timber frame construction works for wall, ceiling, and roof elements can be observed in Esposende. Production begins with beam processing. This refers to the cutting, drilling, milling, and preparing of beams, which are then assembled to create a timber frame. Vacuum lifters place a panel on top, which is secured by a multifunction bridge. This is followed by automatic milling, sawing, and drilling to cut openings for doors, windows, and shafts in the partially finished wall.
The wall is then turned and filled fully automatically with insulating materials such as cellulose or wood fiber. A second panel closes the wall, and then it’s off to the storage area, where it awaits further processing, along with other elements. If required, windows can be installed at this stage. With these prefabricated wall and ceiling elements, Kozowood can construct up to 300 houses per year.
Advantages of timber as a building material
Fire resistant
The low thermal conductivity of wood is a natural form of protection and makes wooden buildings very resistant to fire. Modern constructions often exceed statutory fire protection regulations.
Strength
Timber is light and extremely resilient. In relation to the weight of the material, it supports ten times as much weight as steel. Timber also has high compressive strength and elasticity.
Speed of construction
Individual building modules are prefabricated in series in factories and can be assembled on construction sites within a few days. This saves time and lowers costs.
Environmentally friendly
Wood binds CO2 — even after it has been felled. And, unlike other building materials, it can be dismantled and recycled with low energy consumption.
Greater stability for large timber buildings
To construct larger buildings, Kozowood has also acquired a production line for cross-laminated timber (CLT), which went into operation in 2023. This enables the production of more load-bearing components compared to timber frame construction. CLT elements consist of multiple layers that are glued crosswise, one on top of the other, and compressed to form a mass timber element. This makes them so stable that they can even withstand earthquakes.
CLT is used to create entire surfaces for walls or floors. It should not be confused with glulam (glued laminated timber), which consists of multiple solid wood boards glued to form thick beams. These are used as load-bearing elements in large and tall buildings.
The Danish HOMAG subsidiaries System TM and Kallesoe specialize in production technology for these mass timber elements and have jointly planned the processes of the CLT production line for Kozowood. The production process begins with raw, dried lumber that is fed into the production line by a vacuum infeed system. Conveyors carry the wood through a series of scanners that measure certain characteristics, such as moisture content, and detect defects or cracks. "Our automatic saw then cuts out the defective sections according to the optimization process," says Peter Simonsen, Area Sales Manager at System TM. This is done at high speed and precision.
The boards are now between half a meter and three meters long. The finger jointing machine takes care of the next step. It mills finger-joint profiles into both ends. These are special cuts in the wood that run in a zigzag pattern and fit precisely into each other. The pieces are then glued together to form boards, serving as the base material for the next production stage. This is where Kallesoe's machines come into play.
Super glue for greater load-bearing capacity
The finger-jointed boards are cut to lengths suitable for the construction of cross-laminated timber. A vacuum lifter arranges the boards in alternating lengthwise and crosswise layers. Adhesive is applied between each layer to bond them securely. This creates a cross-laminated structure for enhanced stability. The adhesive used is something of a secret weapon in the production process. “Its properties clearly stand out from existing products on the market,” says Chief Sales Officer Jens Kallesøe.
The adhesive mixture consists of two components and is relatively inexpensive. It is fire-resistant and can be processed quickly. Kallesoe is utilizing high frequency press technology for rapidly heating up the glue and with that, quickly cures the glue line in the CLT elements. The technology can be compared to a microwave oven. “The gluing and pressing process is around two times faster than that of a conventional cold press,” says Kallesøe.
At the moment, Kozowood's CLT line has the capacity to produce around 20,000 cubic meters of building material per year. However, the next expansion stage is already being planned. The planned new production line should also be able to produce glulam (glued laminated timber) for creating the load-bearing skeleton of larger buildings — even including those with more than ten stories. This is a sign that Kozowood aims to reach new heights in the future.
More about
- The entire Group pitches in when HOMAG's subsidiary WEINMANN equips a gigafactory with machines and systems for timber construction: → Joining forces for the gigafactory
- The HOMAG Group provides the appropriate technology for the production of floor and wall panels in the US: → Gold rush in the timber construction
- New apartment buildings within a very short time frame - HOMAG's subsidiary WEINMANN offers systems and creates opportunities: → How timber can solve the housing shortage
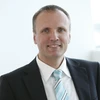
Achim
Homeier
Director
Global Marketing & Product Management
HOMAG Group AG
Homagstraße 3
72296 Schopfloch
Germany
Homagstraße 3
72296 Schopfloch
Germany
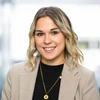
Alisa
Finkbeiner
Global Product Marketing
WEINMANN Holzbausystemtechnik GmbH
Forchenstr. 50
72813 St. Johann
Germany
Forchenstr. 50
72813 St. Johann
Germany