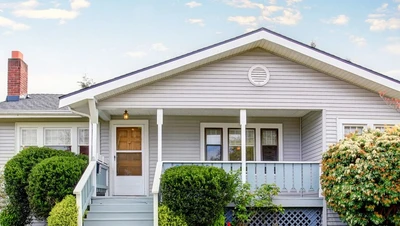
Gold rush in timber house construction
Mar 23, 2023
Using wood in construction is standard practice in North America. But the industry is facing a problem: There is a shortage of workers, even though the construction market is expected to grow. That’s why US companies are promoting the production of floor and wall panels in highly automated facilities. The HOMAG Group can provide the appropriate technology.
Every region of the world has its own way of building. In North America, it usually looks like this: Trucks unload timber, workers assemble the beams and battens on site. These are used to build walls and then entire houses. Building with brick and mortar? That is very rare in North America. The timber construction rate is 85 percent. Almost all houses are built manually — a traditional but laborious method. Sometimes, there are up to 60 people working on a construction site.
But it is uncertain how long this approach will continue to be widely used, because the construction industry in the US is faced with a problem: There are not enough qualified workers. This is mainly due to the consequences of the real estate crisis that shook up the construction sector after the 2008 financial crisis. Many experienced professionals moved to other fields at that time. The industry has still not recovered from this blow. In addition, stricter visa requirements for skilled workers from abroad are further aggravating the staff shortage.
Technology for affordable housing
At the same time, people in numerous regions of the US are searching in vain for affordable homes. According to estimates, there is a shortage of around five million apartments and houses nationwide. Constructing these buildings in the traditional way seems unrealistic in view of the staff shortage. So, what can be done? “Prefabrication and automation can make a decisive contribution to solving the problem,” says Darrin Schramm. The sales expert works at Stiles, a company which is part of the HOMAG Group and sells woodworking technology to the North American market.
This also includes software-controlled machines and systems that can be used in factories to manufacture walls, floors, ceilings, or roof trusses quickly and fully automatically from timber. Trucks then transport the components to the construction site, where they are assembled into a complete house in just a few days. “Faster, more precisely, and with fewer personnel than would ever be possible with manual labor alone,” says Schramm.
Investors with business acumen
Many North American business professionals share this view. Forest owners, timber merchants and sawmill operators are entering the timber construction business to create affordable housing on automated production lines. “They’re either building their own production facility or buying an existing construction company and modernizing it,” Schramm says.
To that end, they need expertise and the right technology. HOMAG also offers machinery and systems for timber construction in North America under the WEINMANN brand. The Schuler Consulting company, which is part of HOMAG, helps new entrants to set up production and select suitable equipment. Often inexperienced, the factory workers can attend seminars at the WEINMANN Academy, where they learn how to properly operate the sophisticated technology.
Until now, the machines and systems have been manufactured exclusively in Germany and Poland. That is about to change. Going forward, instead of sending heavy equipment across the Atlantic, HOMAG intends to run its production as close to the customer as possible. This saves shipping costs, reduces the carbon footprint, and ensures short delivery times, which are very important to US customers. That’s why an alliance has been formed under the umbrella of the Dürr Group as the parent company, to drive the project forward. It includes WEINMANN and Stiles, but also Dürr Mexico.
The North American subsidiary is based in Querétaro, a three-hour drive northwest of Mexico City. The experts there have extensive technical know-how. “We can build on this knowledge to manufacture machines and systems for the production of timber construction elements,” says Evelia Reyes, HOMAG Country Manager at Dürr Mexico.
The plan is to initially manufacture assembly tables in Mexico, as these currently have the longest delivery times. On the tables, timber elements are assembled into frames. These timber frames can be turned on the movable assembly tables, filled with insulation material and covered — and the wall is finished.
In order to make the existing WEINMANN products fit for the North American market, they must be adapted to design and material standards in the US and Canada. This work is carried out by the design experts at Dürr Mexico.
Prefabrication and automation can make a decisive contribution to solving the staff shortage problem.
Darrin Schramm, Sales Manager at Stiles
Space is running out
Production is scheduled to start this year. “As of July, we will be starting with eight tables per month for a customer project in the US,” Reyes says. It is envisaged that initially 13 employees will work for the new segment of Dürr Mexico. By 2027, this number is expected to double.
No wonder space is running out in Querétaro. As a result, the new business segment will move into its own building a few kilometers away as early as mid-2023. The staff is very proud of the subsidiary’s growth, according to Reyes. She promises: “We are highly motivated and will make the project a success.”
More about
- Solving the housing shortage: sustainable and affordable → living space made of timber
- Rooms from the conveyor belt: visiting the swiss: → timber construction company Blumer Lehmann
- Wood as a construction material with a promising future:→ guest contribution from Prof. Dr. Heinrich Köster