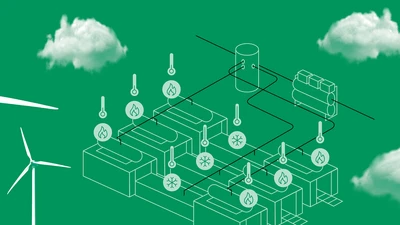
Greenabler
Mar 23, 2023
With new technologies, Dürr is paving the way for the climate-neutral painting of cars. The company is focusing on the intelligent use of energy and the electrification of the plant.
Paint does not make a car faster or easier to maneuver, but no one will deny that it enhances the beauty of a vehicle. That is why manufacturers spend a lot of effort on this production stage. The car body is cleaned, passed through a dip bath, then it is painted several times and dried in between. No wonder that the paint shop accounts for more than 40 percent of the energy required in an automotive plant. But this also means that, being a paint shop manufacturer, Dürr can make a major contribution to reducing greenhouse gas emissions in the automotive industry by offering the right technologies.
For years, the company has been specifically developing technologies that enable its customers to produce in the most sustainable way possible. Dietmar Wieland is a Senior Manager in the research and development team and has been working for Dürr since 1991. He has been dealing with the topic of energy efficiency for just as long. “This continues to be one of the most important drivers of innovation,” the development engineer says. Particularly in view of the high energy prices, automotive manufacturers have a great interest in keeping their operating costs under control.
Another current focus is on the electrification of all process steps during painting. This gives customers the opportunity to become independent of gas as a fossil fuel and to operate their plant in a climate-friendly way by using green electricity. “Many automakers have set themselves the aim of achieving a carbon-neutral production,” says Wieland. “We support them in this effort with the right solutions”. For a German customer, Dürr is currently building the first completely electrified paint shop that can be operated with zero emissions using green electricity. From the paint booth to application technology and digital applications: In every area, the customer relies on the latest innovations from the mechanical and plant engineering firm. Even car body ovens and exhaust air purification systems are heated with electricity instead of gas.
Intelligent paint drying process
The use of the electrically powered EcoInCure oven alone can reduce the CO2 emissions of the entire paint shop by 40 percent when using green electricity. And that is not the only advantage of the new generation of ovens. “By means of air flow simulations, we observed that the car body dries faster when it is heated from the inside out,” Wieland reports. To allow the hot air for curing the paint to flow specifically through the opening in the windshield, the car bodies pass through the oven tunnel transversely, resulting in optimal heat transfer to parts that are difficult to access. This is particularly helpful in the case of EVs, as the electrically powered vehicles are reinforced underneath the door threshold on account of their large battery. The so-called rocker panels dry much better in the EcoInCure.
Many automakers have set themselves the aim of achieving a carbon-neutral production.
Dietmar Wieland, Senior Manager in Dürr's R&D team
Green nervous system for the paint shop
As a systems supplier, Dürr looks not only at individual processes and products on the way to a sustainable paint shop, but also at the plant as a whole. The latest result and a milestone in energy efficiency: EcoQPower, a combined heating and cooling system individually optimized for each paint shop.
In automotive plants, energy has so far been provided centrally and often based on a blanket approach. “This results in most process steps being supplied with the same temperature level — even though it is not needed by all of them,” says the 59-year-old. In the case of the hot water supply of a paint shop, for example, the particularly high heat requirement of the intermediate ovens is taken into account, which is around 80°C. However, the high-temperature water is then also used to supply ventilation systems, which only need to heat the room air to 21°C.
So why not supply each process step with only the amount of energy and the temperature level that is actually needed? EcoQPower can do just that. Cooling and heat are generated in a decentralized manner in the paint shop using electricity. Moreover, the intelligent system prevents the loss of energy. For example, in cathodic dip-coating, paint is applied using an electric current, generating heat that has remained unused until now. EcoQPower uses these and other waste heat sources, supplying other areas of the paint shop with the recovered energy.
Before the Dürr specialists equip a new paint shop with EcoQPower, they have to investigate the climatic conditions of the location. After all, it is hotter and more humid in a tropical region than in Scandinavia. The necessary statistics are provided by weather stations. In addition, data such as production quantity and vehicle type are included in the calculation. This overall picture provides an indication of how the energy flows need to be interconnected in order to achieve the most efficient operation. On this basis, heat pumps, hot and cold water tanks, and cooling towers are installed. They are interconnected by intelligent software — and the paint shop’s green nervous system is ready.
EcoQPower has enabled Dürr to minimize the energy consumption of a paint shop by up to 19 percent. This largely compensates for the additional costs of electricity, which is a more expensive energy source. “Even at locations that are climatically ideal for operating a paint shop, we can achieve energy savings in the double-digit range,” says Wieland, summarizing the potential of the innovative system.
EcoQPower: The intelligent energy network for the paint shop
With an individually optimized combined heating and cooling system, Dürr can significantly reduce the overall energy consumption in the paint shop. The innovative EcoQPower system enables plant operators to electrify the paint shop efficiently, thus becoming independent of gas as a fossil fuel.