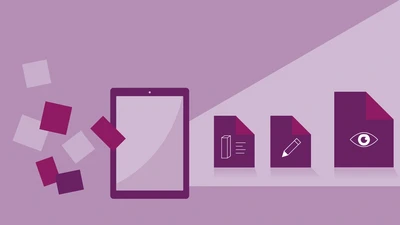
Say goodbye to messy paperwork!
Mar 23, 2023
The productionManager, HOMAG’s digital job folder, always shows carpentry workshops and joineries the current status of orders.
Whether they have 10 or 100 employees, many companies still use paperwork in everyday operations. Let’s assume, for example, that a customer makes a last-minute decision to change the cabinet on order to a white instead of a gray one. In such a case, the information is often written down on a piece of paper and passed on to the person in charge. If everything goes smoothly, the change will be accommodated in production. But what if the note is lost or the information is forgotten? Then chaos is inevitable.
The Binsch carpentry workshop from Baden-Württemberg knows this issue all too well. During a large project with many components, the overview was lost at some point. It was almost impossible to keep track of what had been manufactured, painted, finally assembled or already installed on the construction site. “We expect the productionManager to provide us with transparent parts tracking,” says Julian Roob, Head of Work Preparation and Project Manager at Binsch. The carpentry workshop has been using the web app since the summer of 2022. An initial appraisal came to a positive conclusion.
Instead of loose slips of paper, any order changes and progress are recorded directly in the productionManager for everyone to see. This enables traceable and consistent workflows — from work preparation to production. Everyone has the same, up-to-date status and knows where which order is located. Employees can see on their tablets or computers which components and articles need to be processed next. This allows them to get straight to work, without time-consuming handover meetings.
Tracking the progress of orders in real time — that is what Manuel zum Buttel, founder and Managing Director of ZB Holzsysteme, also wanted to do. And not just in the executive office, but throughout the entire company. “The crucial point was to keep an eye on the whole order,” says zum Buttel, explaining the decision in favor of the productionManager. “No other system offers this level of transparency.”
The productionManager is tailored to the needs of small and medium-sized companies, as Hendrik Albers, software expert at HOMAG, explains: “The web app is intuitive to use and doesn’t require a lot of onboarding. In addition, it can be integrated into any existing workshop environment.” This means that the productionManager is also an interesting option for companies that don’t have HOMAG machines. Because nobody needs messy paperwork in the carpentry workshop.