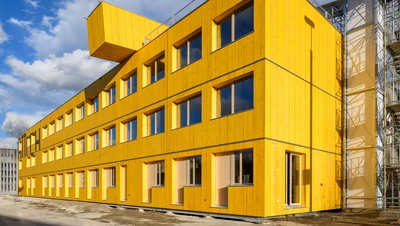
Rooms from the conveyor belt
Buildings made of wood are environmentally friendly, affordable and can be quickly constructed. Prefabricated elements are used to create, among other things, comfortable apartments and offices. Dürr subsidiary HOMAG supplies the required technology, for example, to the Swiss timber construction company, Blumer Lehmann.
Many hundreds of tree trunks are stored on the company's premises. Boards, square timbers and beams are piled up next to the workshops. Trucks are maneuvering, machines are humming, the smell of spruce and fir is in the air. Visitors notice immediately: It’s all about wood at Blumer Lehmann in Gossau, a town near St. Gallen, about 25 kilometers south of Lake Constance.
The family business does not, however, build tables, chairs or cabinets. Blumer-Lehmann belongs to the Swiss Lehmann Group and is one of the leading timber construction companies in the country. “We are convinced that wood is the building material of the future,” says Katharina Lehmann, who has been running the business for 24 years.
When the boss talks about wood, she is completely in her element. “I grew up in the company,” she says. The business has been in her family for five generations. The former residential building with its pistachio green shutters now houses the cafeteria. Her ancestors started out in 1875 with a sawmill on a creek; later roof trusses, then barns for agriculture were added to the portfolio. “For about 20 years, we have been constructing complete buildings made of wood, including apartment buildings, school buildings, office buildings and industrial buildings,” Lehmann says, adding: “We take care of every step of the process – from the felled tree to the finished house.”
Timber construction – the advantages in brief
1. Renewable raw material
Wood from sustainable forestry preserves the natural resources of the earth.
2. CO2 reservoir
Wooden buildings store CO2 for many decades. If construction timber is recycled, the greenhouse gas is permanently removed from the CO2 cycle.
3. Speed
Finished modules can be set up in just a few hours. If required, they can simply be moved to a new location.
4. Nice and warm
A 20-centimeter-thick prefabricated wooden wall filled with insulation material insulates as well as a concrete wall five times as thick.
The portfolio not only comprises breathtaking arch constructions like the Swatch headquarters in Biel or the Apple store in Bangkok – “Free Form” is what the experts call it. A large part of the business consists of comfortable buildings made of wooden modules. “We manufacture the complete modules individually in our factory according to the customer’s wishes,” says Lehmann – with digitally controlled plants that produce the elements quickly and efficiently.
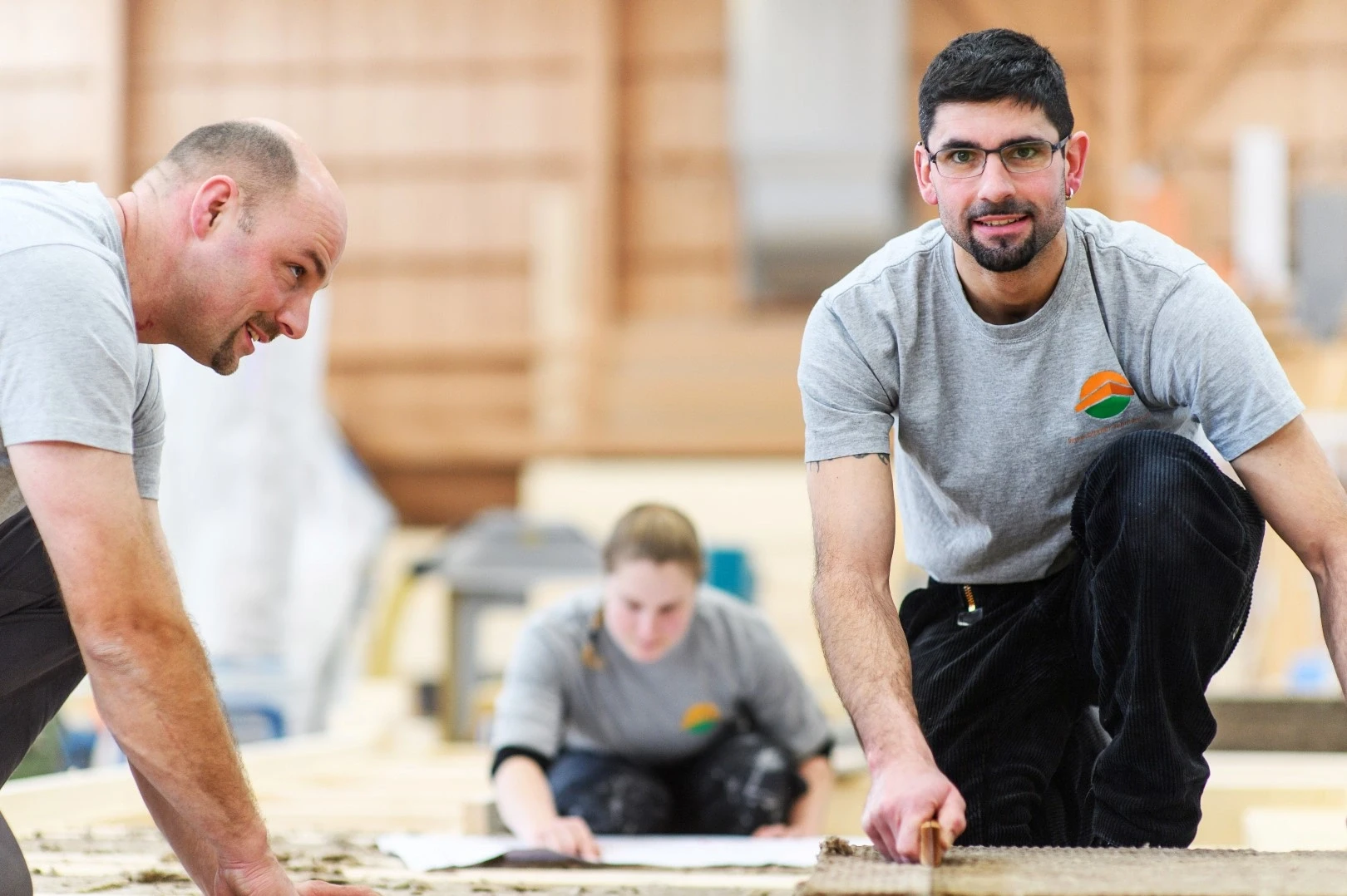
The process is much faster than spending months building brick walls or pouring concrete into steel frames. It also shifts work from the construction site to the shop floor. The premises are dry, kept at a constant temperature, and the professionals are permanently present, thus guaranteeing the consistently high quality of the modules.
The environment and climate also benefit from the trend to timber construction. “Wood is a raw material that is abundant here,” Lehmann says. Swiss forests offer large quantities of wood that is used sustainably. What is processed in Gossau comes from within a radius of 80 kilometers of the company's headquarters.
Huge carbon reservoir
There is no doubt among experts that wood is a sustainable building material. Unlike in the production of steel and cement, hardly any climate-damaging CO2 is produced. Today, the construction and maintenance of buildings account for almost 40 percent of global CO2 emissions. The cement industry alone is responsible for approximately 8 percent of global greenhouse gas emissions.
A single-family house made of wood, on the other hand, stores up to 25 tons of CO2. That is the amount emitted by two and a half average Germans per year. Extrapolated to entire conurbations, large volumes of CO2 are thus removed from the carbon cycle and can no longer harm the climate. Modular buildings assembled from elements can even be moved and reassembled in a different location. Moreover, wooden houses can be recycled when disassembled. Consequently, administrations are already taking action: In France, for example, public buildings must consist of 50 percent wood starting from 2022.
It is reasons like these that led Katharina Lehmann to make timber construction the main pillar of the business. “Even my great-grandfather said that it was our job to find solutions to problems.” She took this sentence to heart when her father suffered a stroke and she unexpectedly had to join the company at the age of 24 – alongside her business studies. “Fortunately, there were trusted and experienced people whose advice I benefited from,” she says. Since then, turnover has increased fivefold and the number of employees has grown from 70 to 350.
Today, the company premises are the size of eleven soccer fields. The tour begins at the timber stacks, where a crane clamps logs in its gripper and places them on a conveyor belt. The logs disappear into the sawmill where they are cut up. The boards are then stored in the drying chamber for three to four days.
Troubleshooting with digital eyes
Houses must be stable. The wood used for them must be free from defects. Looking for individual knotholes, cracks or resin deposits and sawing them out takes far too long. “That is why we bought a machine sorting system in order to better refine the wood,” Lehmann says.
The dried boards shoot through the planing machine on a conveyor belt. Watching over them are digital eyes, scanning the wood. Smart software detects errors immediately and reliably. But there is more: The machines from the Danish supplier System TM, which is part of the HOMAG Group, instantly saw out the flaws. The machine can eliminate more than seven defects per second.
Another System TM machine immediately glues the parts together again. To this end, it cuts serrations into both ends of the board, which perfectly fit together like a lock and key. This so-called finger-jointing process thus produces standardized boards – ideal for use where maximum stability or aesthetics are required.
In a further processing step, several of the pieces of wood joined together in this way are glued together in layers at right angles to the wood grain or nailed together in an environmentally friendly way with hard beechwood pins. This results in 20-centimeter-thick beams. Blumer Lehmann has this production step carried out by an external company.
About a special project
The spectacular building on the Lattich site in St. Gallen: In the area around the freight railway station, 45 modules provide space for small businesses in the creative industries. Especially cities can really benefit from the advantages of modular construction. Obstacles to traffic caused by construction work are short-term. Blumer Lehmann was able to assemble the modules within a short period of time using the flexible modular system.
Timber house elements from the conveyor belt
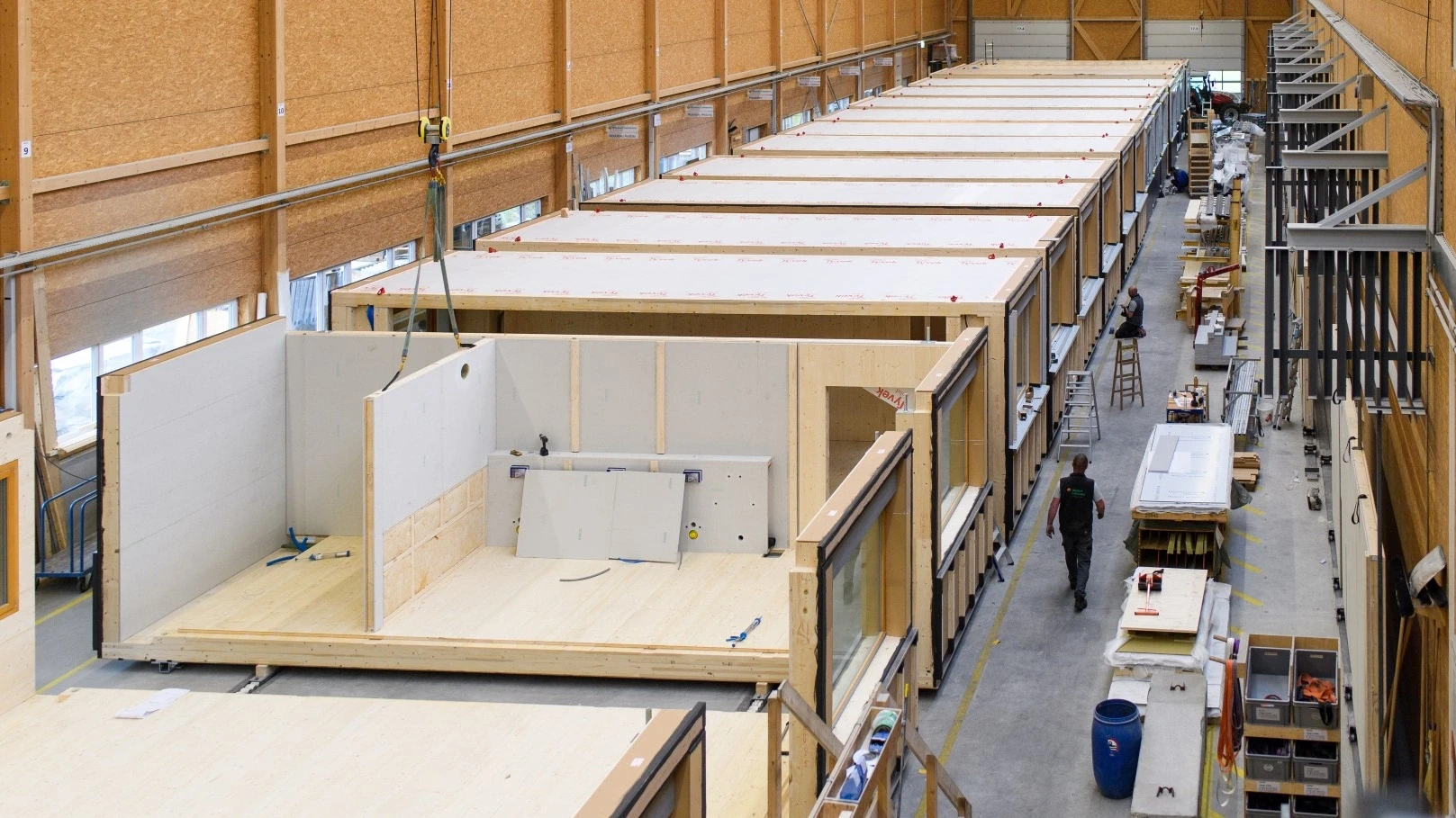
HOMAG subsidiary Weinmann has relied on the trend towards timber house construction for a long time. Among other things, the company offers machines and equipment for timber framing. That is what carpenters call the sawing and preparation of beams for roof trusses. Their portfolio also includes automated production lines for wooden construction elements for small carpentry companies, large prefabricated-house manufacturers – and customers such as Blumer Lehmann.
How this works can be observed in the next hall. Employees assemble the frame of a wooden element from beams of different lengths and cover it with a panel. Then the Weinmann multifunction bridge slides over the wall – and nails, drills, saws, mills, and marks. Within a few seconds, it affixes the panel and provides the openings for doors, windows and shafts. The semi-finished element is then turned and the cavities are filled with insulation material. A second panel closes the wall.
After a short finishing process, the wall is automatically erected and then transported to the intermediate storage. The carpenters in the factory assemble walls, ceilings and floors into finished modules or pack them individually. Then the journey to the construction site by truck begins. With the help of a crane, the fitters will erect the prefabricated elements there. It takes two to three days for the complete building to be erected – an advantage especially in narrow inner cities or when things have to move quickly for customers, for example in hotel extensions.
That is why Blumer Lehmann goes one step further. “We often deliver the individual modules already equipped with electrical wiring, water pipes, wallpaper, tiles and kitchen units,” says Lehmann. Craftspeople commissioned by the company will take care of that while the modules are still in the factory. “We even send the toilet brush along, if that is desired,” she says, laughing.
Making careful use of limited resources is very important for the company. Therefore, it ensures that nothing goes to waste. “We can only use about 60 percent of a complete tree in production,” Lehmann says. What remains is residual wood. The tour leads past two towers that look like silos. “This is where we store the wood pellets that are produced at our plant.” And what happens to the tree bark? That is also taken care of. It is shredded into mulch and goes into landscaping. Or it is processed into briquettes and, like the pellets, used in the company’s own power plant. An ecosystem in which nothing is thrown away.
In the coming years, Katharina Lehmann plans to further digitalize her production. She will then be able to manufacture individual rooms in large quantities even more efficiently – in the long run, not only in Switzerland. Lehmann is receiving an increasing number of orders from abroad and is expanding – for example to Germany, where a second location for module production is to be built as early as this year.