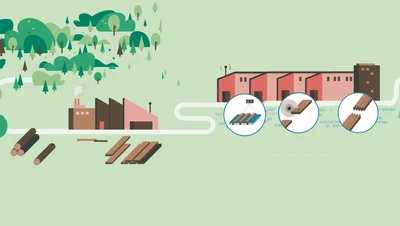
From the forest to the house
A house made of wood? For a long time, that seemed old-fashioned. Thanks to the trend towards sustainable building, this naturally grown material is once again very popular. With machines and systems such as those offered by the HOMAG Group, freshly felled trees can be turned into prefabricated houses in just a few days.
1. Forest & Sawmill
In the forest, forestry companies cut down the trees. The logs thus created are called round timber.
In the sawmill, the round timber is cut into boards, square timbers and beams, and dried.
2. Scanning, Sawing out & Finger joints
Sensors scan the wooden boards with high precision and speed. In this way, they find weaknesses, such as knotholes, cracks, resin deposits, discoloration and edges.
The machine cuts out up to 420 flaws per minute.
The now flawless – but short – boards are joined together with the help of “finger joints” to form a long, stable board.
3. Timber framing, Framework & Creation of elements and modules
The beams must be cut and precisely prepared. This work is carried out by automated production lines.
In modern manufacturing, robots assemble the framework – the skeleton of the house wall.
Panels close the framework, and insulation material is placed in the gaps. The result: finished wall, roof and ceiling elements that are assembled into modules.
4. Last stop: construction site
In just 24 hours, the complete house is created from the elements and modules.
Rooms from the conveyor belt
Blumer Lehmann manufactures wooden elements as if from the conveyor belt. A visit to a HOMAG customer in Switzerland.
Material with a promising future
Wood as a natural resource offers enormous potential says Prof. Dr. Heinrich Köster