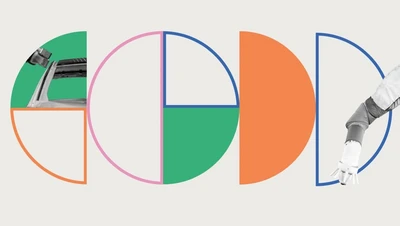
Always the right type at hand
Apr 8, 2025
Automation is a strong growth driver for industrial equipment suppliers such as the Dürr Group. The strength of automation is its versatility: Sometimes it makes production faster, sometimes more precise. Sometimes it handles heavy loads, sometimes it impresses with its endurance. And in any case, it is unbeatably efficient. We present a selection of types.
The Dürr Group has risen to a leading position in the global automation industry in recent years. Not only by acquiring renowned companies. Automation has also become a growth driver in established business areas such as painting technology and woodworking.
What is the reason? In synergy with artificial intelligence and large amounts of data, automated processes will be able to solve many of the industry’s problems in the future. This includes, for example, the lack of skilled workers in Western countries. Automated production also ensures the consistent quality of products that are manufactured on a large scale. In addition, population and prosperity are growing in many regions of the world. This increases the demand for goods and forces companies to produce more quickly.
In the Dürr Group, the face of automation is characterized by a wide variety of features: They can be found in machines and systems of different sectors — from woodworking to paint shops and medical technology. We present selected types, each with its own characteristics.
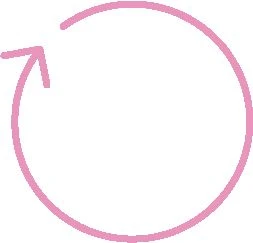
The enduring one
All over the world, people are laying huge quantities of parquet, laminate, and designer flooring. Estimates range up to 900 million square meters per year. That is more than the surface area of Singapore. This requires billions of boards, which are usually simply “clicked” into place during installation.
In order to produce these huge quantities, the production lines of companies must be in constant operation. Group subsidiary HOMAG offers a system that requires only two or three short maintenance breaks per year and runs continuously the rest of the time. “The unfinished boards go in at the front and the packed boxes with the boards ready for transportation come out at the back,” says Andreas Winter, who works in technical sales and product management. The system produces up to 300,000 boards fully automatically per day. Calculated over the course of a year, it would mean that you could circle the world almost three and a half times if you laid the boards end to end. Part of the system is the TENONTEQ D-800 — a master of endurance running.
The entire system consists of several components. First of all, a rip saw cuts the raw boards into strips, then a cross cut saw divides them into individual boards. High-precision profiling machines mill the click profiles on the longitudinal and transverse edges of the boards — the locking systems. “The boards are moved through the longitudinal profiling at up to 300 meters per minute,” says Winter. This is equivalent to a speed of 18 kilometers per hour, or more than three boards per second. The surface is checked once again, then the parts are stacked and automatically packaged.
What sounds simple is controlled by the technology in a sophisticated way. This is important so that the floor covering later results in an attractive pattern. Sensors and cameras detect markings in the raw boards and align them precisely before processing, so that the decor of the boards fits precisely during installation.
Although the system is particularly suitable for the production of floorboards, it can also be used to produce furniture components — wherever angles, rebates, grooves, or other contours are cut into a wooden workpiece. And all that while running with endurance.
The unfinished boards go in at the front and the packed boxes with the boards ready for transportation come out at the back.
Andreas Winter, Technical Sales & Product Management at HOMAG
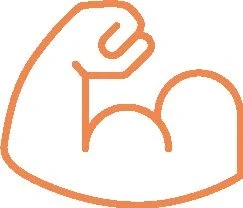
The strong one
Watching the driverless transport vehicles maneuver around the paint shop feels like you’re in a science fiction movie. The smallest of the fleet are only slightly wider than a toboggan and are so flat that they drive under a car body, lift it up and move it to the next workstation. “The small vehicles carry loads of up to one ton,” says Stefano Bell. The product manager is responsible for driverless transport systems at Dürr — the fleet of Automated Guided Vehicles (AGV) is called ProFleet.
The rolling power packs replace rigid conveyor technology. It is replaced by total flexibility: An AGV always drives to the painting box that is free, ready for operation, and suitable for the next work step. The control system complements and changes the route plan as required. So, if one workstation suddenly fails, the other stations can continue their work undisturbed. The AGV simply moves to the next available box. “This increases flexibility in production tremendously,” says Bell.
In order to prevent accidents, the AGV is equipped with sensors. Laser scanners immediately detect obstacles. If necessary, it brakes or drives around the obstacle. Charging also takes place automatically — the AGVs use the transfers at the stations and recharge their energy storage independently. This means that they can be used almost non-stop.
The driverless transporters can be used not only in the paint shop, but also in the final assembly of cars. Here, they transport a vehicle including wheels, engine, and battery from one workstation to the next. Of course, finished cars are much heavier. This is why a different version of the AGV fleet is used here. One that can carry up to six tons. Talk about strong!
This increases flexibility in production tremendously.
Stefano Bell, ProFleet Product Manager at Dürr
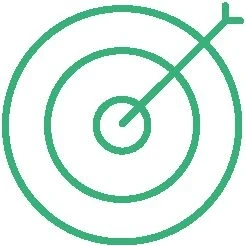
The precise one
Robots have to apply the paint evenly and precisely to the car body. This is particularly important for multi-colored cars — for example, if the roof is to have a different color.
What is visually striking in road traffic is a laborious process in conventional production: First, the car body passes through the painting line. “When it is dry, employees apply a protective film and leave only the desired areas exposed,” explains Dürr painting expert Timo Beyl. The vehicle is then painted in a second painting process. A lot of effort when you consider that hundreds of car bodies are painted in several colors every day in a car factory.
With the EcoPaintJet Pro, this work can be simplified. A nozzle plate attached to the robot’s applicator works so precisely that the painting paths can be applied without missing a single drop. Masking is no longer necessary. This saves material, time, and energy.
Before the robots begin their work, optical sensors measure the entire car body. Software compares the real car body with a model stored in virtual form and corrects the painting paths accordingly. “Even car bodies for the same vehicle type have differences that could lead to painting errors without this correction process,” says Beyl. Only when it is clear how all deviations can be compensated for does the robot guide the applicator over the car body with high precision. The permitted tolerance for the paint application corresponds to approximately 0.1 millimeters.
Vibrations in the vicinity of the system must be avoided at all costs. Therefore, the conveyor technology and the rails on which the robots move must be carefully matched to the system environment. Only then can the EcoPaintJet Pro make full use of its precision.
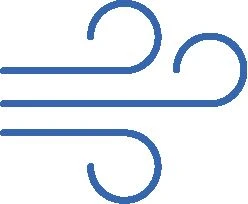
The fast one
Diabetes is a widespread disease of our time. Almost half a billion people are affected by the condition. They have to measure their blood sugar level regularly. Medical technology offers various possibilities of doing this. For example, a small device with a built-in cartridge containing ten tests. Those affected simply have to press a button with their finger. The device then pricks the fingertip, draws a tiny amount of blood, and displays the result shortly afterwards.
The cartridge is the heart of the device and consists of micro components. The ten tests included are arranged in a circle and resemble the drum of a revolver. They consist of a mechanism, a spring, an ultra-thin needle, and a reagent paper. The production of the tiny cartridges is highly complex. The manufacturing process must be fast. The product must function with absolute reliability and has to be produced in huge quantities.
Kahle Automation, a Dürr Group subsidiary that will operate under the name of BBS Automation from June 2025, specializes in machines and systems that meet these requirements. The customer of the Italian company comes from the pharmaceutical industry and receives production technology tailored precisely to its needs. “All our machines and systems are unique,” explains product manager Marco De Priori.
The system designed for producing the cartridges consists of three machines that share a total of 30 work steps. In the process, the micro components are precisely assembled, inspected, and moved further along. In each step, each machine processes up to 30 parts at the same time. This is the only way to keep up the pace: The system produces around 45 cartridges per minute, each one consisting of 10 sub-assemblies. That adds up to around 450 parts per minute. Meanwhile, cameras check the quality of the work at every stage. Workpieces with even the slightest deviations are ejected from the production process. Because ultimately, only the parts that meet the high safety requirements should find their way to the patient.
Typically Automation
0,1
millimeter tolerance
For a precise paint application, the EcoPaintJet Pro does not deviate from the calculated starting point by more than a tenth of a millimeter.
136,000
kilometers per year
The TENONTEQ D-800 produces floor boards while running with endurance. Over the course of a year, you could circle the world 3.4 times if you laid the boards end to end.
6
tons
From 500 kilograms to 6 tons, the powerful driverless transport systems of the ProFleet can maneuver anything that needs to be moved.
45
cartridges per minute
At top speed, the system from Kahle Automation produces complex micro components for measuring blood glucose levels.
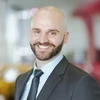
Stefano
Bell
Product Management
Dürr Systems AG
Carl-Benz-Str. 34
74321 Bietigheim-Bissingen
Germany
Carl-Benz-Str. 34
74321 Bietigheim-Bissingen
Germany
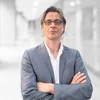
Alexander
Sedlak
Marketing & Documentation Director
BBS Automation
Parkring 22
85748 Garching
Germany
Parkring 22
85748 Garching
Germany
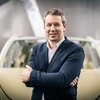
Jens
Reiner
Senior Vice President
Sales
Dürr Systems AG
Carl-Benz-Str. 34
74321 Bietigheim-Bissingen
Germany
Carl-Benz-Str. 34
74321 Bietigheim-Bissingen
Germany
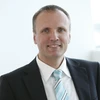
Achim
Homeier
Director
Global Marketing & Product Management
HOMAG Group AG
Homagstraße 3
72296 Schopfloch
Germany
Homagstraße 3
72296 Schopfloch
Germany