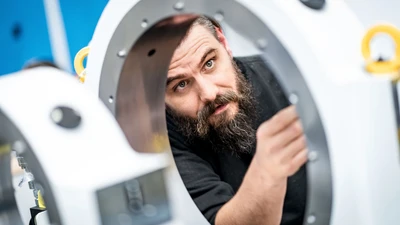
Stress test
Mar 20, 2020
The number of electric cars is rapidly growing. Manufacturers are constantly developing new electric motors. The heart of such motors is a rotor that rotates up to 20,000 times per minute. Experts at the Dürr subsidiary Schenck RoTec test this essential component in their spin test systems – sometimes until it flies apart.
The three-meter-high colossus is housed in steel, its heavy hood secured by 14 bolts as thick as your thumb. One technician is looking at his monitor and following the progression of the test. The atmosphere around the Schenck spin test system is one of concentration and silence. The humming of a motor is all that can be heard. Yet nothing hints at the fact that, inside the closed container, forces of several tons are at work, subjecting the component to extreme stress.
For the developers of rotors, turbines or engines, tests in spin test systems are often indispensable. “With their help, the resilience of materials can be optimally tested,” says Andreas Buschbeck. He manages the spinning service of Schenck RoTec, a small but quickly growing unit of the Dürr Group.
The long-established enterprise from Darmstadt is known for its expertise in balancing technology. The sale of spin test systems has also been part of the business for quite some time. “Since 2010, we have also been offering our customers spin testing as a service,” says Buschbeck. What started out as a niche market alongside the sale of spin test systems is gaining more and more traction. In the past four years alone, sales in this new business line have quadrupled.
With the help of the spin test systems, the resilience of materials can be optimally tested.
Andreas Buschbeck , Head of technical consulting Schenck Rotec
Forces akin to a swing carousel
The reason for this speedy development is the boom in electromobility. Automobile manufacturers are increasingly developing the motors required. At their heart is a rotor which, with its magnetic fields of electric energy, generates kinetic energy. “When cars are in motion, the rotors rotate up to 20,000 times per minute,” remarks Buschbeck. Enormous centrifugal forces impact the metal, similar to a swing carousel, where the chairs are pulled outward when the ride spins quickly. The spin test system enables testing of how well a component can withstand such massive forces.
Can you calculate how strong those forces are? “Sure,” answers Buschbeck, who has a degree in physics, and dictates the correct formula: “F = U ∙ Ω2.” Could we have that in more concrete terms? Andreas Buschbeck laughs and grabs paper and pencil. A few seconds later, he reads out the result: “For a 20-gram magnet in the rotor and at 20,000 revolutions per minute, that’s more than half a ton.” That is an awful lot, considering more than a dozen magnets are installed in a single rotor. These incredible forces pull on the material and deform it. And why are the experts particularly looking at that part of the rotor containing the magnet? “Because that’s where the structure of the material is interrupted and is thus more vulnerable,” explains Buschbeck.
The tiny bulges that develop at high revolutions cannot be detected by the naked eye. And yet they can be decisive when it comes to the stability of the material. Furthermore, it is possible that even the slightest shifting of individual components can lead to unbalance which will cause the motor to vibrate. The vibration is loud and leads to even faster wear. That is why changes are precisely measured in the spin test system using digital technology. Those results show whether the rotor is constructed such that it meets desired specifications, says Buschbeck. If a component deforms to a greater degree than expected in the spin test system, the rotor developers have to go back to the drawing board.
After his studies, 32 years ago, Andreas Buschbeck came to what is now the Dürr subsidiary and initially developed balancing machines. Subsequently, he advanced the company’s spinning technology as an internal consultant. However, not all customers find it worthwhile to buy their own spin test systems. When more and more customers asked for advice on spinning issues, the experts started developing a new business line. Today, in the → Schenck Technological and Industrial Park, four spin test systems are employed on a daily basis to test components and material samples. It is especially important for customers that Schenck experts can precisely analyze the digital data collected. “This consulting service is an integral part of our range,” states Buschbeck.
Traces of the endurance test
Some tests in the spin test system take several weeks – for instance, if they have to simulate continuous operation in an electric car. In such cases, the experts at Schenck perform several thousand test cycles at various speeds. If a customer wishes, Schenck also offers the ultimate test: The object is accelerated until it flies apart. This sometimes requires a speed of 200,000 revolutions per minute. The traces of such endurance tests can be seen on the steel inner walls of the spin test systems: They are speckled with craters.
Spin test systems used to be merely employed to determine the load limit of a material. It was only Buschbeck and his team who further developed the systems by adding digital metrology and modern software. In doing so, they have turned spin test systems into high-tech products. Today, with the aid of optical sensors, laser beams and electric fields, changes to materials can be identified in every phase of testing.
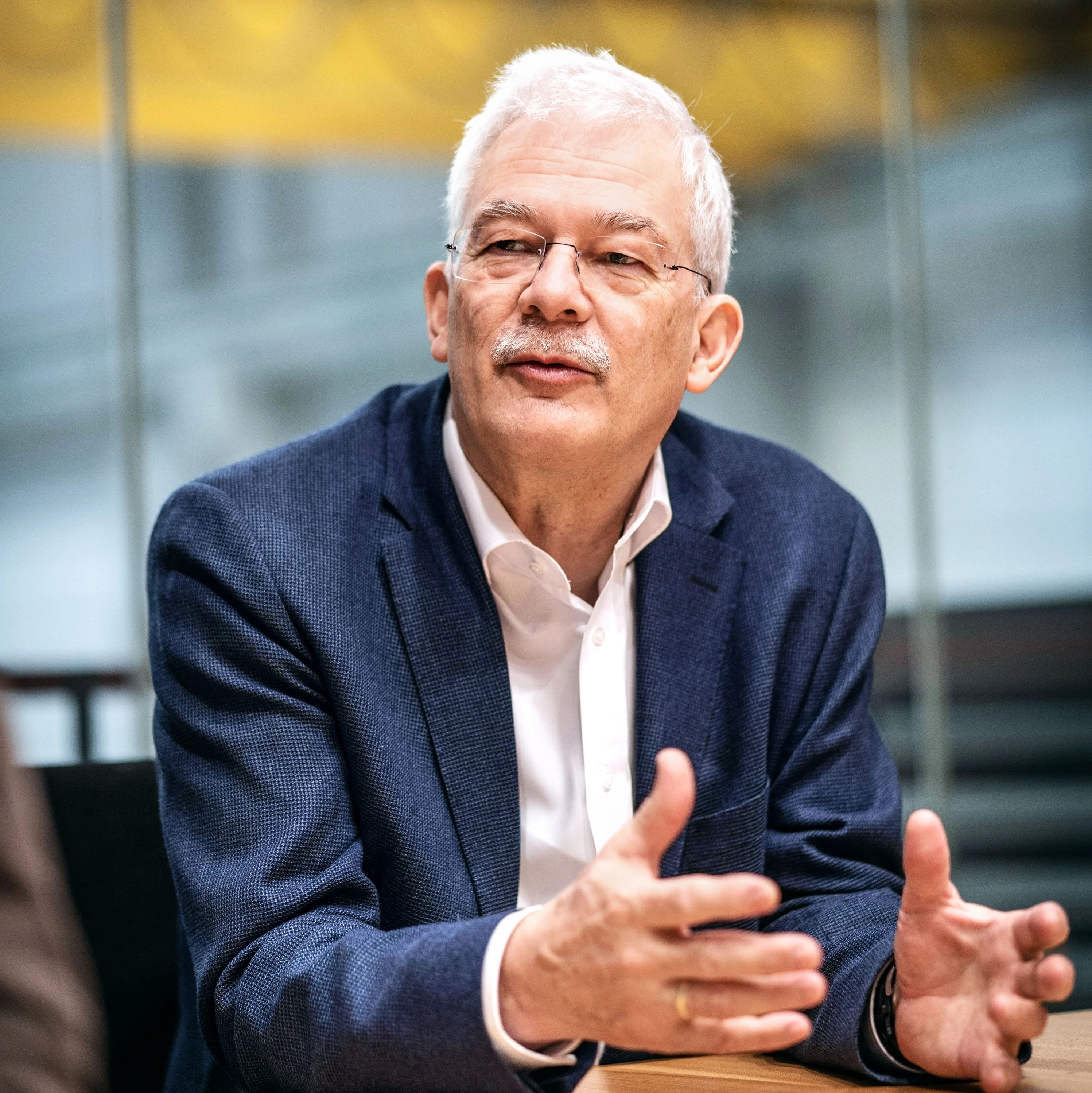
Currently, the developers are working on another innovation. They want to photograph the spinning parts in their spin test systems using unusually short flashes. The results would then not only consist of measurements, but also photos, which would facilitate interpretation.
Time and again, customers also approach the spin test experts with special wishes – such as manufacturers of turbine rotors. They drop off parts of a material with Buschbeck when they need special testing. Schenck RoTec even built a customized spin test system especially for one customer who wanted the pump gear of a rocket tested.
In the past year, the experts from Darmstadt were involved in a veritable project of the future. Students at the Swiss Federal Institute of Technology (ETH) in Zurich had constructed a vehicle with which they wanted to participate in a contest initiated by Tesla founder Elon Musk. The theme of the competition was a new concept for mobility – the → hyperloop. It involves transport pods being propelled through a vacuum tube at speeds exceeding 1,000 kilometers per hour. Before the competition, Schenck tested the rotating parts of the vehicle in the spin test system – thus contributing to the success of the team: The student team was able to travel to California for the finals, where it took second place.