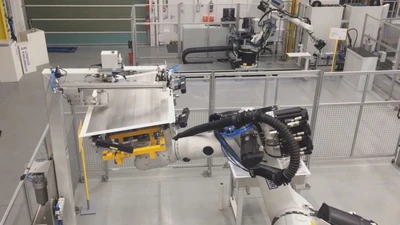
Production technology for electric vehicles
Mar 23, 2020
The Dürr Group offers a broad range to new players and well-established OEMs
The automotive industry is investing large sums in electromobility. In doing so, it is focusing not only on developing battery-powered cars but also on equipping its plants with modern production technology. In 2019, incoming orders of the Dürr Group relating to e-mobility production technology increased by 44% to € 390 million. Aside from well-established OEMs, customers also include many new manufacturers of battery vehicles.
In 2030, around 60% of all new cars will have an alternative drive system. This amounts to a good 70 million cars, compared to 14 million in 2020. The majority of them will be powered by electricity. E-mobility is on the cusp of strong growth, in which the Dürr Group will participate as a technology partner.
New carmakers are emerging, particularly in China and the United States, who have no experience of producing conventional cars but are keen to gain market share with battery-powered vehicles. In 2019, over 20 such e-pioneers ordered production technology from Dürr. In order to mass-produce their cars, they first need the necessary factories. “With our experience, we are the right partner for them. We offer a broad technology range and can provide comprehensive advice to e-mobility players in building their production base”, says Ralf W. Dieter, CEO of Dürr AG.
With our experience we can provide comprehensive advice to e-mobility players in building their production base.
Ralf W. Dieter , CEO of Dürr AG
China is the largest market for electric cars. This year, Dürr has already received a large order there for the construction of a paint shop for battery cars. Demand has also picked up in other regions. In the United States, Dürr received three large paint systems orders from e-mobility manufacturers in the second half of 2019.
Whether the customer is an EV startup or an established automotive group – what is important in most cases is that the paint shop be scalable. This means that, in the initial stage, customers often order paint systems for smaller unit numbers. However, the plant must be expandable by modules, thus enabling customers to install additional capacity quickly when sales figures increase.
Broad range for the final assembly of battery cars
In addition to paint systems, the Dürr Group also offers other technologies for the production of electric vehicles – in final assembly, for instance. Since electric vehicles have a less complex power train than their conventional counterparts, their assembly allows for a higher level of automation. Dürr has already installed automated assembly systems for renowned manufacturers of battery cars. Demand is likely to grow as unit numbers in electric vehicle production increase.
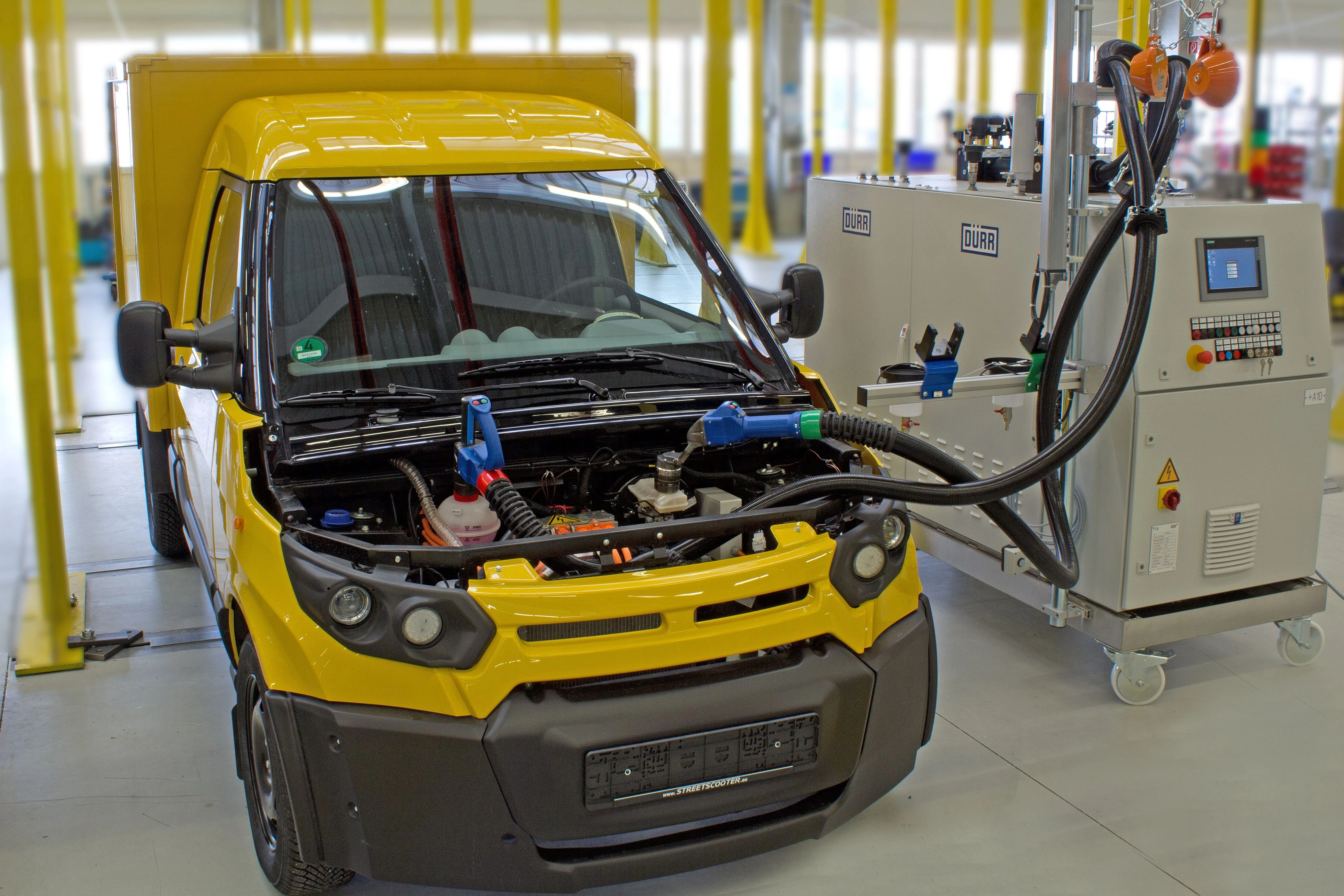
One important stage in the assembly of electrically powered vehicles is the ‘marriage’ stage. This is where the battery is fixed to the underbody using Dürr technology – computer-controlled and with up to 36 bolts, which are delivered to the bolt holes fully automatically. The Group also offers systems for filling batteries with refrigerants. This ensures that the batteries do not get too warm and can achieve their maximum range.
Testing technology for fully assembled cars is also facing new challenges due to the advent of electromobility, especially when it comes to safety. Dürr’s test systems are used to ensure that the high-voltage circuits in battery-powered vehicles do not pose any risks.
Electric motors run quietly thanks to technology by Schenck RoTec
The production of electric motors is supported by Dürr’s subsidiary Schenck RoTec through, for instance, the eTENO balancing system; this measures and corrects unbalance in electric armatures for e-drives. In addition, Schenck RoTec offers the Centrio spin test system for material testing on electric motors. This enables carmakers to determine the maximum rotation loads their motors can be exposed to.
Technology for battery production
To achieve greater unit numbers in electromobility, the automotive industry requires additional capacity for battery production. Here, too, the Dürr Group offers technology for various stages of manufacture. Its subsidiary, Dürr Megtec, offers a system for coating lithium-ion battery electrodes. This process is unique, since it applies the cathode and anode material onto the basic material – a metal foil – simultaneously on both sides.
Dürr supports the manufacture of battery modules through highly precise application technology. Among its products is a coating system for the thermal and electrical insulation of battery cells (insulation can painting). There is also a solution ‘made by Dürr’ for battery glueing. This is where the coated battery cells are arranged next to each other and bonded into a battery module. After that, a thermal interface material (gap filler) is applied. This conducts away the heat generated during battery charging and discharging. Finally, the battery cover is glued into place.
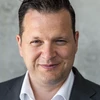
Marcus
Treppschuh
Vice President
Sales
Dürr Systems AG
Carl-Benz-Str. 34
74321 Bietigheim-Bissingen
Germany
Carl-Benz-Str. 34
74321 Bietigheim-Bissingen
Germany
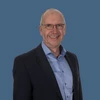
Peter
Böhm
Product Line Manager Electrical Industry / eMobility
Schenck RoTec GmbH
Landwehrstr. 55
64293 Darmstadt
Germany
Landwehrstr. 55
64293 Darmstadt
Germany
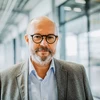
Andreas
Keil
Director Business Development
Dürr Megtec
Carl-Benz-Str. 34
74321 Bietigheim-Bissingen
Germany
Carl-Benz-Str. 34
74321 Bietigheim-Bissingen
Germany