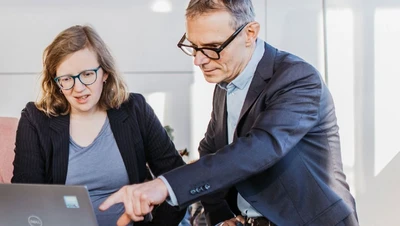
Teamwork is the cure
Apr 10, 2024
You work together on new products, for example on paint curing ovens. How do your roles differ?
Imke Kuschel: I work in Dürr’s digital factory, where we develop software to make machines and systems more efficient and sustainable. But I don't do any programming myself; instead, I work at the interfaces with process experts like Oliver and with our customers.
Oliver Iglauer-Angrik: In my role as senior expert, I am the Group's global contact point for paint curing ovens. I have been involved in this area for 25 years. Nowadays, the development of new drying processes can no longer be separated from their digitalization, as we aim to align both aspects with practical customer needs right from the outset. I see my task in working with the digital factory as rethinking processes digitally while keeping an eye on the added value for the customer. Imke is an important point of contact here.
What kind of innovations are you working on?
I-A.: One example is the EcoInCure paint curing oven — a product that was launched on the market in 2016. It allows hot air to flow into the car body through the windshield opening. This innovative technology enables us to dry complex car bodies faster and more gently, while providing better paint quality. But what was still missing in our view was the digital proof of the drying process — a highlight that has been part of our product portfolio since 2020.
What exactly have you come up with?
K.: We have developed simulation software that analyzes a large amount of data. This allows the paint curing process to be digitally mapped for each car body, starting as early as the production run. This enables an automaker to monitor the quality of the curing process for each individual car body at any time. The software can provide this for any car body model that passes through the oven.
What advantages does the software offer?
K.: In normal operation, our software offers the operator the option to map all body-specific heating parameters. This is used, for example, for documentation in the event of subsequent paint or rust-through warranty claims.
In addition, the oven simulation serves as a decision-making aid to determine whether the paint quality is acceptable or not after process faults have occurred. In the past, in cases of doubt, a car body would continue to be painted after a disruption. It was only discovered at the end of the painting line that the body couldn't be used due to insufficient quality. With our software, car bodies are now immediately removed from the process, thus avoiding any unnecessary further painting. This saves time during analysis and conserves valuable resources.
Is sustainability a personal concern for you?
I-A.: Using the world's resources responsibly is important to me. I’m not the only one who feels this way. I meet many people in the Group who hold the same belief. It is important to me that the concept of sustainability is also an integral part of our “One Vision” corporate statement and must therefore be considered from the outset when developing new products or production processes.
K.: When we develop software in the digital factory, the sustainability aspect plays a prominent role. We also want to convey this to our customers: Opting for software that conserves resources and increases efficiency is an important investment.
Using the world's resources responsibly is important to me.
Oliver Iglauer-Angrik, Senior Expert Research & Development at Dürr
Imke Kuschel
is 34 years old and studied technical cybernetics, a subject that deals with mathematical modeling, simulation, and control of complex systems. At Dürr's digital factory, she works as a member of a scrum team at the interface between process experts and programming specialists. Her extensive product knowledge and specialist expertise in the software field are prerequisites for translating process requirements into functional software in collaboration with the programmers. She is also responsible for implementing and commissioning software from Dürr's DXQ product family at the customer's site.
You have grown up in the digital world, Ms. Kuschel, and have been with Dürr for five years. Mr. Iglauer-Angrik has been with the company five times longer. How does this affect your cooperation with an old-school mechanical engineer?
K.: The age difference isn’t an issue in our cooperation. In fact, we benefit from each other's expertise. Oliver shares his process and system knowledge around paint curing ovens, while our contribution relates to mathematical correlations and data expertise.
I-A.: That’s the great advantage of a company like Dürr: the combination of digital know-how with expert knowledge of production processes. We cooperate very closely at our working level, learn a lot from each other, and can therefore take an effective interdisciplinary approach — perhaps more than other companies.
Oliver Iglauer-Angrik
is 55 years old and has been with Dürr for 25 years. Having studied mechanical engineering, he has held various positions in the company and now works in research and development as a senior expert for drying technology. In addition to heating the bodies of painted electric vehicles, his work focuses on efficiency enhancement and electrification of drying and exhaust-air purification systems in the context of CO2-neutral paint shops. Here, he combines expert knowledge of production processes with digital expertise. His exploration of thermodynamics also led him to teach at the Baden-Württemberg Cooperative State University for several years.
K.: It starts with communication and understanding. When Oliver and I began working together, we explained the technical terms of our respective fields to each other.
I-A.: Web Frontend, NoSQL database, Red Hat — the exact meaning of terms like these have only become clear to me over time and, just like learning vocabulary in a foreign language, I am always learning new things here as well.
K.: I, on the other hand, have learned quite a lot about paint curing ovens. Heat transfer coefficients, air balance, Bernoulli's equation, centralized and decentralized heating concepts — all of these were unfamiliar territory for me. I am now the expert on ovens in the digital factory.
Can you name a situation where you complemented each other exceptionally well?
I-A.: In one customer's paint shop, our simulation tool detected unusual heating behavior during measurement runs performed on an oven. We couldn’t work out why. We spent a long time looking for a theoretical explanation but couldn't find one. Imke then proposed that we have a look on site.
K.: In the plant, we noticed that a worker was alternating the position of the sensors for the oven measurement runs each week between the driver's and the passenger's side.
I-A.: This example illustrates how important mutual exchange is for solving problems. We would have probably kept searching for a theoretical explanation for some time. Imke's suggestion prompted us to look outside the box together.
More about
- Dürr's technologies for the climate-neutral painting of cars: → Greenabler
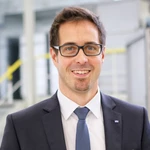
Dr.
Heiko
Dieter
Product Management
Dürr Systems AG
Carl-Benz-Str. 34
74321 Bietigheim-Bissingen
Germany
Carl-Benz-Str. 34
74321 Bietigheim-Bissingen
Germany