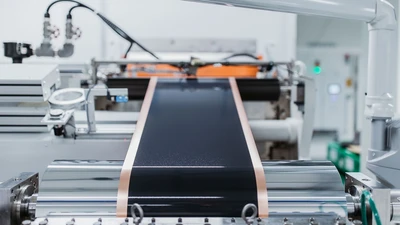
A factory made in Europe
Apr 10, 2024
Together with its partners Grob and Manz, Dürr will offer complete battery factories in the future. In doing so, they will cover the entire value chain from the cell to the finished storage unit. The range of technologies required for this is a unique selling point of this business partnership — no other European provider has a comparable offering.
The visit to the battery factory takes place with a bird’s-eye view, as it currently only exists as a video animation. But its construction from a single source can now become a reality. In their cooperation, each of the three companies contributes its expertise. This enables the entire battery production value chain to be mapped — from the cell through to integration into the vehicle.
So far, only Asian companies have been able to supply complete production facilities for lithium-ion batteries. Joining forces, the Dürr, Grob, and Manz trio is now the first European supplier to enter this field. “We are particularly focused on the needs of the automotive industry, which places high demands on safety and quality,” says Dr. Hannes Schmüser, CEO of Dürr's Clean Technology Systems division, to which this business area belongs. Since the demand for electric cars really took off, new battery factories have been emerging worldwide — in Europe alone, around 60 projects were being planned in 20 countries by the end of 2023.
The factory has been jointly designed by Dürr, Grob, and Manz. The digital production management comes from Dürr's own software subsidiary iTAC. The end of 2023 saw a further expansion of competencies: With the acquisition of the French mechanical engineering company Ingecal and a new partnership with the US coating expert LiCAP, Dürr has increased its technology portfolio for electrode coating. Dürr Consulting advises clients on factory planning, site selection, and ongoing production.
We are particularly focused on the needs of the automotive industry, which places high demands on safety and quality.
Dr. Hannes Schmüser, CEO of the Clean Technology Systems division
Challenging processes
Manufacturing battery cells is a demanding undertaking. Therefore, Dürr and its partners offer customers comprehensive advice, which is essential for the factory setup. It is also about deciding which batteries to produce in the first place. “Depending on their purpose, battery storage units have different compositions and shapes. They can be flat, prism-shaped, or cylindrical,” explains Yannick Wildermuth, who is providing strategic support for the project.
Every battery has a negative pole (cathode) and a positive pole (anode). Today, the anodes of lithium-ion batteries are made from graphite and carbon, while the cathode is made from a mixture of lithium, nickel, and other metals. However, mixtures such as iron phosphates will also become more widely used in the future. Therefore, each factory must be completely customized.
Stirred, not shaken
The source materials are powders that are stirred to form pastes and applied to copper or aluminum foil. The coated foils pass through a dryer before a roller presses them together using several tons of pressure. The foil is then cut into longitudinal strips. This material is later turned into a battery cell.
Dürr provides the expertise and technology for this first production stage. Coating and drying are also relevant in painting technology, although the processes are of course not identical. Dürr also knows a thing or two about exhaust-air purification — it is important in battery production because harmful solvents are as yet indispensable.
When the foils are ready, systems from the partner companies Manz and Grob come into play. A machine cuts the strips to the exact length and stacks them on top of each other — alternating between copper foil (anode) and aluminum foil (cathode). A piece of separator foil is always added in-between for insulation — similar to layering lasagna.
This is followed by rolling, cutting, gluing, welding, or sealing — depending on the final shape the battery should have. What is still missing is the electrolyte, a liquid that ensures ions can move back and forth between the positive and negative poles during charging and discharging.
The energy is rising
There is no life in the cell yet. It is electrically charged during the formation. Only cells of the right quality and maturity are to be processed further. This involves work steps that vary depending on the type of battery and are covered by technology from Dürr, Grob, or Manz.
The battery cell must be fully sealed. Moisture must not penetrate, nor must the electrolyte escape. Testing of the electrical properties concludes the cell production process. The tests are performed by machines from the Group’s subsidiary Teamtechnik.
The cells are then ready for dispatch. In most cases, they are assembled into modules at other locations, then interconnected into battery packs and installed in the vehicle. These work steps are also performed by machines and systems from the three partners.
A new, dry process
Battery technology is constantly evolving. With the acquisition of Ingecal, Dürr can now also supply calendering systems, which play a central role in the coating of electrode foils. At the moment, experts in the field are also working on what is known as dry coating. Dürr's new partner LiCAP has developed a method for producing electrodes without the use of liquid material. “The material is compressed under pressure and then laminated onto the metal foil,” says Wildermuth. The resource-intensive drying of materials after coating is eliminated, reducing the factory's energy consumption.
Dry coating is also a milestone on the way to solid-state batteries, where the electrolyte consists of solid material, making them more powerful, safer, and more climate-friendly than their predecessors. It is regarded as the next major innovation step in battery technology — and it will also be available in a factory from the Dürr, Grob, and Manz partnership in the future.
BATTERY
FACTS
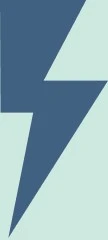
1800
Physicist Alessandro Volta
invented the battery
Around 1830
Batteries were used in technology,
for example for
powering telegraphs
Around 1832
Robert Anderson built the “electric carriage”,
which is considered the
first electric car
in history
38%
of cars in the United States were electric vehicles around 1900
(40% steam-powered,
22% running on gasoline)
100 km/h
speed record: Until 1920,
the electric car was a real
competitor to vehicles
with internal
combustion systems
4,900
gigawatt-hours of battery
storage capacity
to be produced
annually from 2030
More about
- Lithium-ion battery production technology within the partnership of Dürr, Grob and Manz : → One complete battery factory, please.
- Dürr's technology for solvent recovery for the → Sustainable production of battery electrodes in a closed loop.
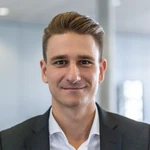
David
Rajtschan
Director
Global Sales Lithium-Ion Battery
Dürr Systems AG
Carl-Benz-Str. 34
74321 Bietigheim-Bissingen
Germany
Carl-Benz-Str. 34
74321 Bietigheim-Bissingen
Germany