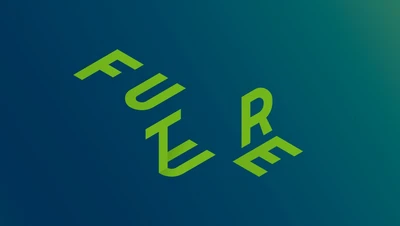
Secret research laboratory
Apr 25, 2024
In the factory of the future, HOMAG shows what the development teams are currently working on. Here people can experience the woodworking industry of the future at first hand. The Group subsidiary is thus also looking for new ideas — together with its customers.
HOMAG’s factory of the future is located 150 meters underground. Visitors are first plunged into the depths with an elevator and are later propelled through a vacuum tube from one station to the next. In hidden halls, travelers get a glimpse of tomorrow’s products. They learn how processing times can be shortened, how manual saws can cut even more precisely, and how intelligent technology saves money and protects the climate. The tour of the future world of woodworking takes half an hour. Then the headsets are taken off again. Welcome back to the present.
The factory of the future, also known as the Innovation Center, is, of course, an illusion created by tiny LED lights and giant projection screens. The 400-square-meter labyrinth of partitions, backdrops, and movie theater seats was built for LIGNA 2023 — the world’s largest trade fair for the woodworking market. HOMAG is at the forefront of this industry. The company supplies machines and systems for a wide range of businesses — from carpentry workshops to industrial furniture and timber house manufacturers with automated production lines.
The journey through time to the factory of the future is not just an entertaining event. Above all, it provides a setting in which customers and HOMAG experts can meet at eye level. “We want to get an even better feel for the industry and test how our innovations are received by customers,” says Daniel Hofius, Marketing Manager Trade Fairs and Events. Together, they consider what challenges woodworking companies face and what technical solutions they need. The insights they gain together are incorporated into the development work at HOMAG.
But enough of the preliminaries. Hold on tight, the journey through time begins.
Faster and more accurate
The first stop is about machine technology that makes cutting faster and more economical. This includes HOMAG’s Measuring System Cutting Quality (MSQ). It uses intelligent algorithms to automatically determine how accurately a saw blade is still working. Replacement can therefore be scheduled and is neither done too early nor too late. MSQ is currently used in automated systems. In the future, it may also be available for manual saws.
Greater efficiency is also provided by Edge Printing. This innovation also meets the increasing demand for individual design options. Edges, for example of shelves, can thus be printed separately and in high quality after they have been attached to the furniture part. The advantage: The furniture manufacturer no longer has to stock dozens of edge bands in different patterns and colors, but only a few neutral types.
The powerLine X-treme throughfeed drilling machine increases the speed of automated furniture production lines. In the future, parts will be accelerated and decelerated even faster as they are transported to the next processing station, further increasing machine throughput. This is made possible by an electromagnetic system that replaces the conventional belt drive.
We want to get an even better feel for the industry and test how our innovations are received by customers.
Daniel Hofius, Marketing Manager Global Fairs & Events at HOMAG
The tension is rising. Now a virtual transport system takes you at the speed of sound to the next station — a deck with 3D simulations. Here, you can see machines that not only use tool and material data, but also self-adjust. A great advantage in times of skilled labor shortages.
The machine can do it all
The first product is an advanced version of the intelliGuide digital assistance system. It uses cameras to take pictures that are analyzed by software. If the machine operator inserts a panel incorrectly, a laser immediately projects an arrow symbol onto the workpiece. The arrow indicates the direction in which to rotate the panel. The operator stays focused on the panel and doesn’t even have to look up at a monitor.
For even better detection and elimination of errors, intelliGuide can be combined with other solutions, such as the MSQ mentioned above. Another option is toleranceCheck. This system detects the tension in the panel and indicates how the saw should be set to ensure the right cutting quality.
Errors can occur when gluing edges. For example, if the panel or glue temperature is unfavorable. In such cases, the Digital Gluing system tells the operator what to do or automatically adjusts the temperatures.
Machine and material data can be collected on a large scale. They indicate the condition of the technology. This allows measures to be initiated at an early stage in order to minimize disruptions and production downtimes. With the help of the serviceAssist system, it will even be possible to predict the optimum maintenance time in the future. This is done in close collaboration with the HOMAG service team, whose specialists plan all further steps together with the customer. In this way, operational safety and maximum machine and system availability are ensured. The virtual tour through the factory of the future continues.
Sustainable and climate-friendly
In addition to efficiency and quality, sustainability and climate protection will also be priorities for woodworking companies in the future. This is what the third room of the factory of the future is all about. One example: Furniture manufacturers often vacuum dust and chips from their production lines continuously, in some cases even when no workpiece is being processed. This accounts for up to 30 percent of energy consumption. HOMAG’s Intelligent Dust Extraction system is designed to ensure that only the amount of power required is provided.
Similarly, almost any modern machine can be operated in an energy-optimized manner. HOMAG’s energyGuide supports companies in this endeavor. The software checks the settings during production and makes recommendations for action. In this way, energy guzzlers can be switched off.
We don’t know the energy consumption of the elevator that brings the guests back to the surface. Never mind, this means of transportation is certainly economical. After all, it’s just an illusion — unlike the products presented, which are already available now or will be in the near future.
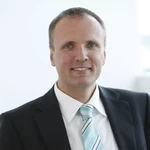
Achim
Homeier
Director
Global Marketing & Product Management
HOMAG Group AG
Homagstraße 3
72296 Schopfloch
Germany
Homagstraße 3
72296 Schopfloch
Germany