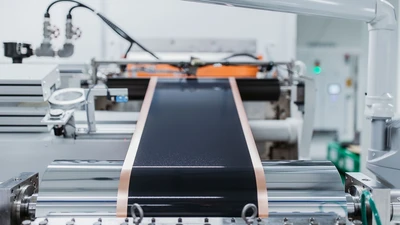
Die Europa-Fabrik
10.04.2024
Zusammen mit seinen Partnern Grob und Manz bietet Dürr künftig komplette Batteriefabriken an. Dabei decken sie die gesamte Wertschöpfungskette von der Zelle bis zum fertigen Speicher ab. Das dafür notwendige Technologiespektrum ist ein Alleinstellungsmerkmal dieser Firmenallianz – kein anderer europäischer Anbieter verfügt über ein vergleichbares Angebot.
Der Besuch in der Batteriefabrik erfolgt im Vogelflug, denn sie existiert bislang nur als Videoanimation. Doch ihr Bau aus einer Hand kann nun Wirklichkeit werden. Bei der Kooperation zwischen den drei Unternehmen steuert jedes seine Expertise bei. So kann die gesamte Wertschöpfungskette der Batterieproduktion abgebildet werden – von der Zelle bis zur Integration ins Fahrzeug.
Komplette Produktionsstätten für Lithium-Ionen-Batterien konnten bislang nur asiatische Unternehmen liefern. Das Trio Dürr, Grob und Manz stößt nun im Verbund als erster europäischer Anbieter hinzu. „Wir haben besonders die Bedürfnisse der Autoindustrie im Blick, die hohe Ansprüche an Sicherheit und Qualität stellt“, sagt Dr. Hannes Schmüser, Chef der Dürr-Division Clean Technology Systems, in der dieser Geschäftsbereich angesiedelt ist. Seit die Nachfrage nach strombetriebenen Autos so richtig in Fahrt kam, entstehen weltweit neue Batteriefabriken – allein in Europa waren Ende 2023 rund 60 Vorhaben in 20 Ländern geplant.
Die Fabrik haben Dürr, Grob und Manz gemeinsam konzipiert. Das digitale Fertigungsmanagement kommt von der Dürr-eigenen Softwaretochter iTAC. Ende 2023 wurden die Kompetenzen nochmals ausgebaut: Mit dem Zukauf des französischen Maschinenbauers Ingecal und einer neuen Partnerschaft mit dem US-Beschichtungsexperten LiCAP erweitert Dürr sein Technologieportfolio für die Elektrodenbeschichtung. Dürr Consulting berät die Kunden bei der Fabrikplanung, der Standortsuche und in der laufenden Produktion.
Wir haben besonders die Bedürfnisse der Autoindustrie im Blick, die hohe Ansprüche an Sicherheit und Qualität stellt.
Dr. Hannes Schmüser, Chef der Dürr-Division Clean Technology Systems
Knifflige Prozesse
Batteriezellen zu fertigen, ist anspruchsvoll. Dürr und seine Partner bieten den Kunden deshalb eine gründliche Beratung an. Sie ist wichtig für den Aufbau der Fabrik. Hier geht es auch darum, welche Batterien man überhaupt herstellen will. „Je nach Zweck weisen Batteriespeicher unterschiedliche Zusammensetzungen und Formen auf. Sie können flach sein, prismenförmig oder zylindrisch“, erklärt Yannick Wildermuth, der das Projekt strategisch begleitet.
Jede Batterie hat einen Minuspol (Kathode) und einen Pluspol (Anode). Heute werden Anoden bei Lithium-Ionen-Akkus aus Grafit und Kohlenstoff hergestellt, die Kathode aus einem Gemisch von Lithium, Nickel und anderen Metallen. Aber auch Mixturen wie Eisenphosphate werden sich künftig durchsetzen. Deshalb muss jede Fabrik ganz individuell gestaltet werden.
Gerührt, nicht geschüttelt
Ausgangsstoffe sind Pulver, die zu Pasten gerührt auf Kupfer- oder Alufolie aufgetragen werden. Die beschichteten Folienbänder gehen durch einen Trockner, eine Walze presst sie anschließend mit tonnenschwerem Druck zusammen. Dann wird das Folienband in Längsstreifen geschnitten. Aus diesem Material entsteht später eine Batteriezelle.
Für diesen ersten Fertigungsabschnitt bringt Dürr das Wissen und die Technologie mit. Um das Beschichten und Trocknen geht es auch in der Lackiertechnik, wenngleich die Prozesse natürlich nicht identisch sind. Und auch in der Abluftreinigung kennt sich Dürr aus – sie ist in der Batterieproduktion wichtig, denn noch sind schädliche Lösemittel unverzichtbar.
Wenn die Folien fertig sind, kommen Systeme der Partnerfirmen Manz und Grob zum Zuge. Eine Maschine schneidet die Streifen in die exakte Länge und legt sie übereinander – abwechselnd Kupferfolie (Anode) und Alufolie (Kathode). Dazwischen kommt immer ein Stück Separatorfolie zum Isolieren – ähnlich wie beim Schichten von Lasagne.
Dann wird gerollt, geschnitten, geklebt, geschweißt, versiegelt oder abgedichtet – je nachdem, welche Form die Batterie am Ende haben soll. Was noch fehlt, ist der Elektrolyt, eine Flüssigkeit, die dafür sorgt, dass Ionen beim Be- und Entladen zwischen Plus- und Minuspol hin und her wandern können.
Die Spannung steigt
Noch hat die Zelle kein Leben. Beim Formieren wird sie elektrisch aufgeladen. Nur der Qualität entsprechende und gereifte Zellen sollen weiterverarbeitet werden. Das ist mit Arbeitsschritten verbunden, die sich je nach Art der Batterie unterscheiden und durch Technik von Dürr, Grob oder Manz abgedeckt werden.
Die Batteriezelle muss vollständig dicht sein. Weder darf Nässe eindringen noch der Elektrolyt entweichen. Eine Prüfung der elektrischen Eigenschaften schließt die Zellfertigung ab. Die Tests erledigen Maschinen der Konzerntochter Teamtechnik.
Dann sind die Zellen fertig zum Versand. In den meisten Fällen werden sie an anderen Orten zu Modulen zusammengesetzt, dann zu Batteriepacks verschaltet und ins Fahrzeug eingebaut. Auch diese Arbeitsschritte übernehmen Maschinen und Anlagen des Dreierbündnisses.
In Zukunft wird es trocken
Die Batterietechnik entwickelt sich ständig weiter. Durch die Akquisition von Ingecal kann Dürr nun auch Kalandrieranlagen liefern, die bei der Beschichtung von Elektrodenfolien eine zentrale Rolle spielen. Im Moment arbeitet die Fachwelt zudem an der sogenannten Trockenbeschichtung. Dürrs neuer Partner LiCAP hat eine Methode entwickelt, mit der sich Elektroden ohne flüssiges Material herstellen lassen. „Das Material wird unter Druck zusammengepresst und danach auf die Metallfolie laminiert“, sagt Wildermuth. Die aufwendige Trocknung der Materialien nach der Beschichtung entfällt, der Energieverbrauch der Fabrik sinkt.
Die Trockenbeschichtung ist auch ein Meilenstein auf dem Weg zur Feststoffbatterie, bei der der Elektrolyt aus festem Material besteht und die deshalb leistungsfähiger, sicherer und klimafreundlicher ist als ihre Vorgänger. Sie gilt als nächster großer Innovationsschritt der Batterietechnik – und sie wird sich künftig auch in einer Fabrik aus dem Hause Dürr, Grob und Manz finden.
BATTERIE-
FAKTEN
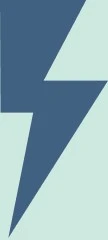
1800
Erfindung der Batterie
durch den Physiker Alessandro Volta
~1830
Verwendung der
Batterie in der Technik,
zum Beispiel für
die Stromversorgung von Telegrafen
~1832
Robert Anderson baut den „Elektrokarren“,
der als erstes
E-Auto der
Geschichte gilt
38 %
der Autos in den USA waren
um 1900 E-Autos
(40 % dampfbetrieben,
22 % mit Benzin)
100 km/h
Geschwindigkeits-
rekord:
Das E-Auto war bis
1920 ein echter Konkurrent
zu dem
Verbrennungsmotor
4.900
Gigawattstunden
Batteriespeicher-
kapazität
werden ab 2030
jährlich produziert
- Produktionstechnologie von Li-Ion Batterien innerhalb der Partnerschaft von Dürr, Grob und Manz: → Einmal eine komplette Batteriefabrik, bitte.
- Mit der Lösemittelrückgewinnung von Dürr lassen sich → Im geschlossenen Kreislauf Batterieelektroden nachhaltig produzieren
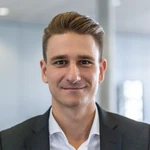
David
Rajtschan
Director
Global Sales Lithium-Ion Battery
Dürr Systems AG
Carl-Benz-Str. 34
74321 Bietigheim-Bissingen
Deutschland
Carl-Benz-Str. 34
74321 Bietigheim-Bissingen
Deutschland