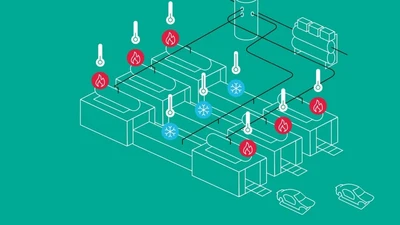
A green nervous system for the paint shop
Jul 18, 2024
In order to operate automotive paint shops as energy-efficiently as possible, Dürr looks not only at individual processes and products, but also at the plant as a whole. EcoQPower is a combined heating and cooling system that can be individually optimized for each paint shop and interconnects all components in such an intelligent way that virtually no energy is left unused. In an initial customer project, the total energy consumption was reduced by around 21%. Three Dürr employees from engineering, research & development, and sales report on the idea behind EcoQPower, its development, and its use by customers.
Mr. Hammen, you work in engineering and developed the idea behind EcoQPower. How did you come up with the idea of equipping paint shops with a holistic green nervous system?
Alexander Hammen: The whole idea started about five years ago with a simple question that I couldn’t get out of my head: Why do paint shops have such high temperatures in the hot water and such low temperatures in the cold water? Wouldn’t it be more efficient to combine the hot and cold water systems and use the energy not needed in one place elsewhere?
When I visited a paint shop in a climatically challenging region, I took the idea a step further: Each location and its climatic conditions must be considered individually. In hot and humid subtropical locations, the conditions are different from those in Scandinavia, for example. That was the starting point for an initial concept that I developed based on an existing plant system. My calculations included all relevant data from the project, such as energy consumption and costs, as well as the readings from the weather station at the location. It turned out that major energy savings were possible if the system was intelligently networked. I shared this insight with my colleagues in research & development. Dietmar Wieland ran the numbers again and came up with the same results. That finally got the ball rolling.
All of a sudden, Mr. Wieland, you were right in the middle of the action when an idea was turned into a product. How did the development proceed and what exactly is behind the system?
Dietmar Wieland: It became concrete very quickly: The customer, on whose data our calculations were based, commissioned a feasibility study for a new paint shop. This led to the result that the concept works. The plant is currently being built — for the first time with the EcoQPower green nervous system.
Our planning approach is as follows: We determine the heating and cooling requirements taking into account the climatic conditions at the location and data such as the production volume, the vehicle type, and the painting process. This is also known as the source-sink profile. It is used to define the optimum temperature levels and to determine where to install hot and cold water tanks, heat pumps, and cooling towers. This completes the EcoQPower system.
In the past, energy supply in automotive paint shops was centralized and often based on a one-size-fits-all approach. Most process steps are supplied with the same temperature level, although not all of them need it. With EcoQPower, each process step only receives the temperature level that is actually needed. Cooling and heating are generated electrically on a decentralized basis in the paint shop, recovered to a large extent, and redistributed to the components via an energy network. Even previously unused energy is not lost thanks to this intelligent system: Heat generated as a by-product of various process steps was previously wasted. EcoQPower now makes it usable and supplies other areas of the paint shop with the recovered energy. In a nutshell: Plant operators benefit from many energy-related advantages. My colleague Bertram Benning from the sales team, who deals intensively with the sustainability of Dürr products, has the figures.
The first paint shop optimized with EcoQPower is currently being built at a German automotive manufacturer’s plant. In general, interest in the intelligent energy network is very high. Mr. Benning, what do customers expect from using EcoQPower?
Bertram Benning: The keyword is decarbonization. The EU wants to be climate-neutral by 2050, and many automotive manufacturers have set themselves ambitious climate targets. In order to achieve these goals, they need to make their production processes as energy-efficient as possible. In the entire car manufacturing process, the paint shops consume the most energy, because cleaning and priming the car bodies, applying the paint and drying it are very energy-intensive — every kilowatt hour not consumed is the best climate protection! This is where EcoQPower comes in, and its use can make a real difference. This is shown by the figures from our first customer project: The paint shop optimized with the energy network system is around 21% more energy efficient than a comparable modern standard system.
This is just the first application, as EcoQPower can be used worldwide depending on customer requirements. Systems optimized with EcoQPower can be operated with both gas and electricity — a big advantage! After all, electrifying the painting process makes customers independent of the fossil fuel gas and is the second most important lever for climate protection alongside energy efficiency. For example, we have developed a fully electrified paint shop for our customer that will be operated using green electricity with zero emissions. Although the operating costs are initially higher due to the purchase of green electricity compared to gas operation, this is offset by the energy savings resulting from the increased energy efficiency thanks to EcoQPower. At the same time, it is the first paint shop to meet the requirements of the EU Taxonomy. This shows once again: With pioneering technologies such as EcoQPower, we are paving the way for operating cost-optimized and climate-neutral automotive production.
The paint shop optimized with the energy network system is around 21% more energy efficient.
Bertram Benning
EcoQPower – verifiably sustainable
Sustainability is often promised, but in retrospect it often turns out to be greenwashing. Scientific analyses can provide clarity here. Johanna Meier and Thomas Betten from the Fraunhofer Institute for Building Physics IBP took a close look at Dürr's first paint shop optimized with EcoQPower. The scientists report on the procedure for preparing the life-cycle analysis according to the specifications of the EU Taxonomy and on the results of the study.
Life-cycle analyses can be used to determine the environmental impact of products, processes, and services. In the context of the circular economy, the entire life cycle is considered: From the materials used and the transportation routes taken, through production and use, to the end of life. “We conducted the EcoQPower study against the background of reporting on the EU Taxonomy,” explains Thomas Betten. “That is why the focus was on greenhouse gas emissions. We investigated whether the energy savings of the factory optimized with EcoQPower can also reduce greenhouse gas emissions over the entire life cycle.” To prove this, the Fraunhofer team calculated the carbon footprint of two comparable, all-electric factories at the same location and with the same performance data — once with EcoQPower and once without. This was based on a conventional electricity mix. The comparison shows: Over its entire life cycle, the combined heating and cooling system reduces the factory’s carbon footprint by 19.2% over a useful life of 15 years.
The scientists had already analyzed individual Dürr products in the past. However, calculating the carbon footprint of an entire factory was much more complex and time-consuming — a challenge given the fact that they only had three months to complete the calculations. “First, we had to collect a lot of data about the factory,” reports Johanna Meier. “Environmental data on the materials used, such as steel and plastic, can be found in scientific databases, for example. For specific information about the energy requirements of a paint shop or the technical processes, however, we asked Dürr directly.” Thanks to the experience gained from previous projects and the good collaboration of all those involved, the analysis was completed on time.
In other sectors, such as the construction industry, life-cycle analysis has long been common practice. In mechanical and plant engineering, many companies only started calculating and reporting the carbon footprint of their technologies at a later stage. “However, we believe that the relevance of this issue will continue to increase in the future,” concludes Thomas Betten. “After all, both legislators and customers are increasingly demanding well-founded proof of sustainability.”
More information
This article was first published in our → Sustainability Report 2023.
Take a look inside if you want to learn more about our approach to sustainability as well as our goals and activities in this area.
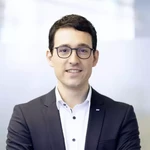
Hanjo
Hermann
Senior Manager Corporate Sustainability
Dürr Aktiengesellschaft
Carl-Benz-Str. 34
74321 Bietigheim-Bissingen
Germany
Carl-Benz-Str. 34
74321 Bietigheim-Bissingen
Germany