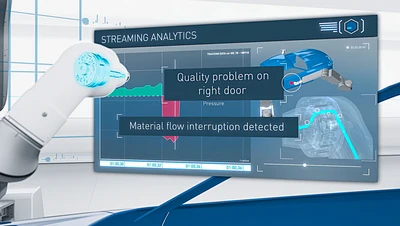
Smart painting
Mar 20, 2020
Dürr is bringing artificial intelligence to the painting lines of OEMs. Right at the forefront are young experts like Simon Alt.
Bright colors, stylish design. In the meeting room, six people dressed in jeans, shirts and t-shirts gather around in a circle – seven others dial in via the Internet. The programmers, data experts and painting specialists provide an update on where they are with their work. Short questions, quick answers. After 15 minutes, the men and women once again disappear behind their screens. Fingers fly across keyboards, keys clatter, eyes scan over graphics and rows of numbers. The soccer table and comfortable chairs in the colorfully furnished rooms on the Dürr campus in Bietigheim-Bissingen look deserted.
Simon Alt holds a PhD in control engineering. He and his team work in the Digital Factory, an important future-oriented field at Dürr, consisting of around 100 employees. They develop applications to make OEMs’ painting lines more efficient – including with the help of artificial intelligence. Their programs make quick work of scrutinizing entire manufacturing systems. They scan ongoing production processes, analyze them and identify systematic quality defects.
Alt joined Dürr three years ago. Today, he manages a team of six people. He already learned about artificial intelligence at university, where he studied engineering cybernetics, a mixture of mathematics, information technology and engineering. This field of study deals with the analysis and targeted control of technical systems – including their modeling and simulation. One day, these systems are likely to solve problems like humans can today. For Alt this is a fascinating thought. Dürr products offer him the right environment for this. “Paint shops are so complex that they provide an ideal platform for the use of artificial intelligence.” This topic has high priority at Dürr: “The use of artificial intelligence in the painting process currently occupies several teams, with whom we are in close consultation.”
The software experts quickly realize whether or not an idea works in practice, since they have the support of experienced painting process specialists. “This is where we have an advantage over many other companies that offer software for the painting industry”, says Alt.
Paint shops are so complex that they provide an ideal platform for the use of artificial intelligence.
Dr.-Ing. Simon Alt
Structured work instead of science fiction
When Alt talks about artificial intelligence, it doesn’t sound like science fiction but rather like structured work. “We can use artificial intelligence to analyze production data and gain important insights from it.” Does a valve in a dip tank need to be serviced? Why is the temperature in the oven not right? Is there a link between paint color and error rate? Finding answers to questions like these currently costs OEMs a great deal of time and money, as they must check each machine and each system individually. With the help of intelligent algorithms, it will be possible to answer these questions ever faster, better and more easily.
Big data plays a crucial role in finding solutions. Alt points to a chart. “For us, data primarily includes everything that can be measured in a plant.” This could be temperature, pressure or the quantity of liquids. Hundreds of probes and sensors already measure this kind of data at all important points in a Dürr painting line. “This information is the raw material for artificial intelligence”, says Alt. It is stored in a database and analyzed automatically.
The smart algorithms rely on a wealth of experience. They compare current with past data. They identify any discrepancies and check whether these kinds of patterns have led to errors before. One example would be the spray pressure of a robot dropping for a few milliseconds. In this case, the system would know that the most likely cause is a defective valve. A quick check of the painting results would prevent a potential quality issue from going unnoticed until final inspection – by which point many vehicles would already have been affected. “Plus, the intelligent search for causes allows for predictions to be made on how much longer a component is likely to last”, says Alt. Costly failures in ongoing production could thus be prevented, for example by replacing parts during idle periods. Such an analytics function is currently being presented to customers in the form of the → DXQequipment.analytics software.
Dürr’s → DXQplant.analytics software monitors not only individual machines but the entire paint shop. The algorithms record if there is an increase in, say, the number of defects on car bodies painted blue every Monday. They analyze millions of data and search for the cause. The source of error can be narrowed down. Unusual measurements in the paint mixing room might indicate that the same error always occurs during routine cleaning at the weekend. Employees responsible for optimization in car factories normally spend days searching for such causes, which is hugely time-consuming. Going forward, this will be much quicker, thanks to → DXQplant.analytics.
Can machines act like humans?
Up to now, software has analyzed information and presented recommendations for action. But the responsibility for implementing these recommendations still chiefly lies with humans. What Alt and his colleagues are working on is for Dürr plants to self-regulate one day. “When it comes to these questions, artificial intelligence is still in its infancy”, says Alt. His team is conducting research using the method of reinforcement learning, among others. In this method, software is programmed to feel rewarded whenever it makes any progress. Just like a dog that gets a treat for good behavior.
“It is even conceivable for the entire automotive factory to be included in a self-regulating system”, says Alt. In this case, production processes would be automatically modified to ensure, for example, that a problematic machine causes minimum hindrance to the production process. It might even be possible to divert supply chains.
However, Simon Alt and his team still have a lot to do before this becomes reality. Until then, they will no doubt find some time for the odd game of table soccer.
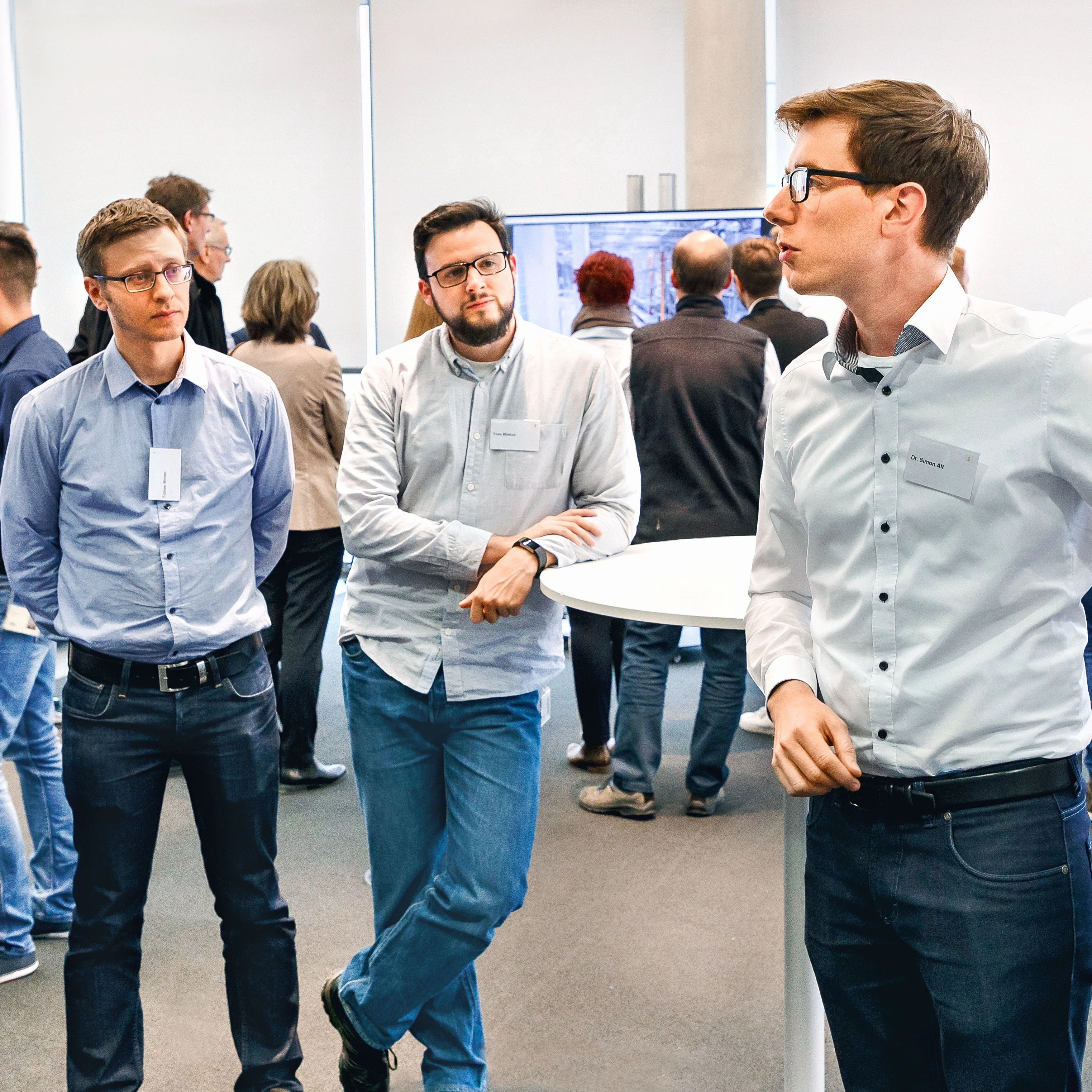