
Creative minds welcome
Mar 1, 2019
The mechanical and plant engineering industry is changing faster than ever. Networked technology is making production operations smart. Eighty people in Dürr’s digital factory are the driving force behind this development. Markus Hummel is a member of the management team. The engineer values experience and fresh ideas from young employees, who are keen to shape this change.
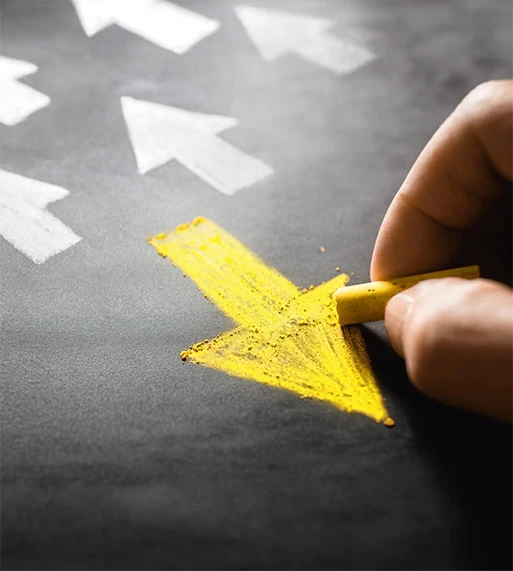
Markus Hummel - Department Head Software Engineering & Solution Development
The mechanical engineer has been with Dürr for 17 years. He is heavily involved in manufacturing execution systems but also more complex programs used for controlling and managing the production processes of entire factories. At Dürr’s digital factory, Hummel is also responsible for developing digital products – one of the Group’s most important areas of the future.
DIGITIZATION IS EVOLVING AT AN EVER-INCREASING PACE. WHAT EFFECT DOES THIS HAVE ON THE REQUIREMENTS FOR YOUR STAFF?
The effects are far-reaching. Twenty years ago, automation engineers would pick up the necessary programming skills on the fly – they were generalists. Today, that’s no longer enough. We need #experts who specialize in certain areas and master them perfectly. For example, they must plan entire software systems and know how the components work together.
ASIDE FROM TECHNICAL SKILLS, WHAT ELSE IS REQUIRED?
Apart from technical qualifications, today’s employees must be more creative and open than before. They must identify new trends quickly and be able to assess the opportunities of technical developments. This is because our industry is changing at an ever-increasing pace. And we want to help shape this change – through fresh and unconventional ideas. We therefore welcome #creative minds as part of our team.
HOW HAVE PERSONALITY REQUIREMENTS CHANGED?
Communication skills have become particularly important. In a complex digital project, nobody knows every single detail. Specialists are mainly familiar with their own fields. They must therefore be able to describe accurately and clearly what they are working on and what their issues are. Only then can managers keep track of what’s going on and lead the team successfully.
WHY DO YOUNG IT EXPERTS OPT FOR DÜRR?
Because we work on the big ideas of the future. We are quite similar to the well-known software and Internet companies. But I believe that the work here is more exciting. Apart from the new and further development of our products, we also work closely with our customers and adapt our software to their requirements. To this end, we need to travel to their production sites. When you work with us, you also see the world.
New Prototype
Digital transformation will only happen with the help of qualified people. This is why the Group is preparing employees specifically for the digital workplace. Julian Spöcker is one of them.
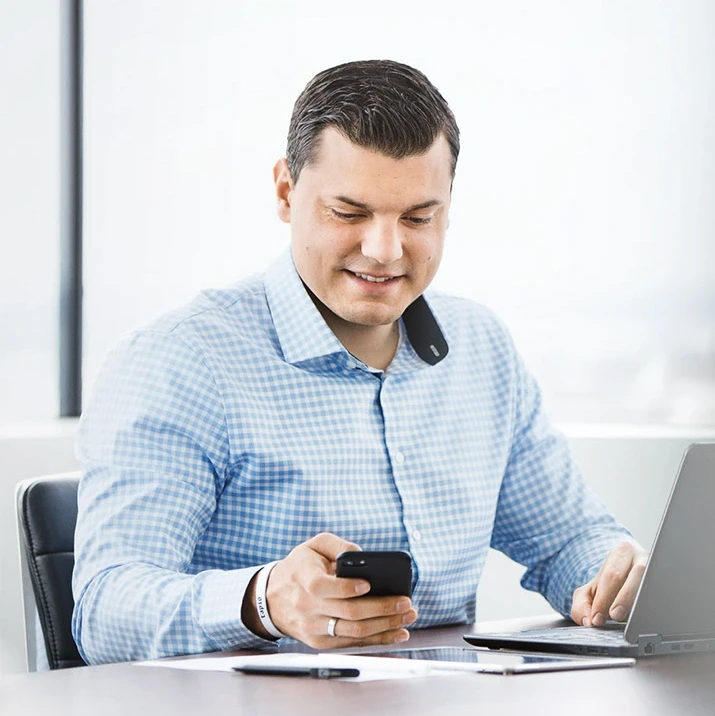
Julian Spöcker is only 30, but he already has a keen knowledge of the HOMAG Group. The Dürr subsidiary builds woodworking machinery, which can be found in factories and workshops all over the world. Today, these systems can do much more than just saw, drill and glue. They are networked and produce furniture automatically – almost as if by magic. Spöcker is passionate about his work. During the interview, he keeps reaching for his marker and going up to the wall to draw squares, circles and arrows on the whiteboard. The machine here, the customer there. Here is the digital platform that connects furniture producer, mechanical engineering firm and supplier. And there is a digital marketplace, which can be accessed using a cell phone or tablet.
# 1987: Born in Freudenstadt (Germany)
# 2008: Joined the HOMAG Group
# 2011: Completed his cooperative state university bachelor’s degree
# 2011: Started in Life Cycle Service at the HOMAG Group
# 2015: Completed his cooperative state university master’s degree
# 2017: Began working on tapio
→ tapio offers such a digital marketplace and brings different companies from the woodworking industry together via the Internet of Things. “tapio helps the woodworking industry to take the next step on their digitization journey”, says Spöcker – and talks about a whole evolving ecosystem.
→ tapio helps customers analyze their production, plan more flexibly and video call service engineers. Going forward, the plan is to add more features. It will be possible to predict exactly when maintenance is due and to optimize production. Spöcker heads up the tapio sales operations, but his responsibilities are not limited to selling: one of the key tasks for his team is, together with partners, to develop digital products for the woodworking industry.
FRESH IDEAS FOR THE TRANSFORMATION
In the traditional mechanical engineering sector, this is not a classic approach. Here, high-quality technology has always been developed in-house over many years and then sold. “Nowadays, applications are often tested at the customer’s site early on, and improved together”, says Spöcker. It’s a way of working that he is used to.
Experienced engineers regard Spöcker more as a creative mind. But people like him are needed more than ever. Everyone knows this industry is undergoing far-reaching change and that fresh and unconventional ideas are important. “I’m keen to help develop them”, says Spöcker and laughs.
Dürr is specifically promoting employees like him. The industrial engineer, specializing in mechanical engineering, began a cooperative state university program with the HOMAG Group after finishing high school with an IT qualification. During his cooperative studies, university lectures alternated with practical sections – which even took him to Singapore for several months. While studying, Spöcker was already exploring whether Facebook or Twitter could be used to boost sales in mechanical engineering. He smiles. “The time was not yet ripe for it.”
The focus today is on digital features that can be added to machines at a later stage.
Julian Spöcker, Head of Sales at tapio
SUCCESS AT THE DEEP END
Spöcker’s first permanent job with the HOMAG Group threw him in at the deep end. He was tasked with introducing a digital system for worldwide customer service. Remote maintenance, service tickets, the engineers’ work – all of which was to be handled uniformly. He visited 14 foreign subsidiaries, traveling as far as Australia, to train his colleagues. “There I was dealing with xperienced engineers.” They were used to doing their own thing and were thus skeptical toward him. Did he have to prove himself? Spöcker nods.
He completed the job successfully and was motivated by his colleagues’ praise. He had also gained valuable knowledge. “I learned what needs our customers have.” Today, he is often approached for internal advice – even by more experienced colleagues. Sometimes he joins members of the Board of Management around the conference table. A good opportunity to show what he can do.

GO-GETTERS WELCOME
Over the next few years, Spöcker would like to build and manage a market segment. In a mid-sized but global company such as Dürr, this is not a pipe dream, but a realistic goal. Go-getters are welcome.
Alongside his job, he also completed his master’s degree in international management three years ago. The Group supported him in gaining his second degree – also financially. Spöcker believes that “here, everyone is given the opportunity to achieve something.”
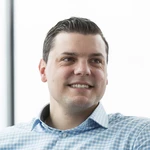
Julian
Spöcker
Director Value Added Services
HOMAG GmbH
Homagstrasse 3-5
72296 Schopfloch
Germany
Homagstrasse 3-5
72296 Schopfloch
Germany