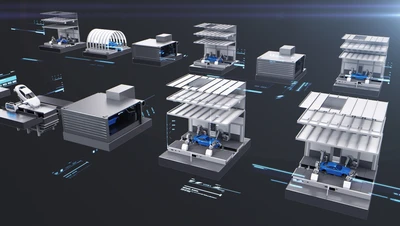
"Artificial intelligence helps to optimize production processes"
Interview with Dr. Simon Alt from the Dürr Digital Factory
When it comes to artificial intelligence, Dürr is one of Germany’s leading industrial companies. This is the result of a study by RWTH Aachen University, which was published in May. The university studied 145 companies to ascertain how artificial intelligence (AI) is used in research and development and where it has already found its way into new products. The study has named Dürr as one of five Successful Practice Companies. Dr. Simon Alt from the Dürr Digital Factory in Bietigheim-Bissingen explains what AI means and what role it will play at Dürr in the future.
Everyone is talking about artificial intelligence (AI). What exactly does it mean?
Artificial intelligence helps us better understand and optimize production processes. A large amount of different production data is collected, for example with the help of sensor systems, and correlations and recurring patterns are identified. This data includes process values, downtime or maintenance and quality information. AI software recognizes how changes that occur at a certain point in the process affect other areas. First the data and correlations are merely observed, which then leads to active intervention, whereby changes are made to the production process based on the data analysis. Such intervention is still rare in plant engineering, but it is set to become a big topic. It means that a plant is self-learning and can optimize its processes on the basis of data analysis. The method, which is based on AI, is also referred to as machine learning – I prefer this term to artificial intelligence.
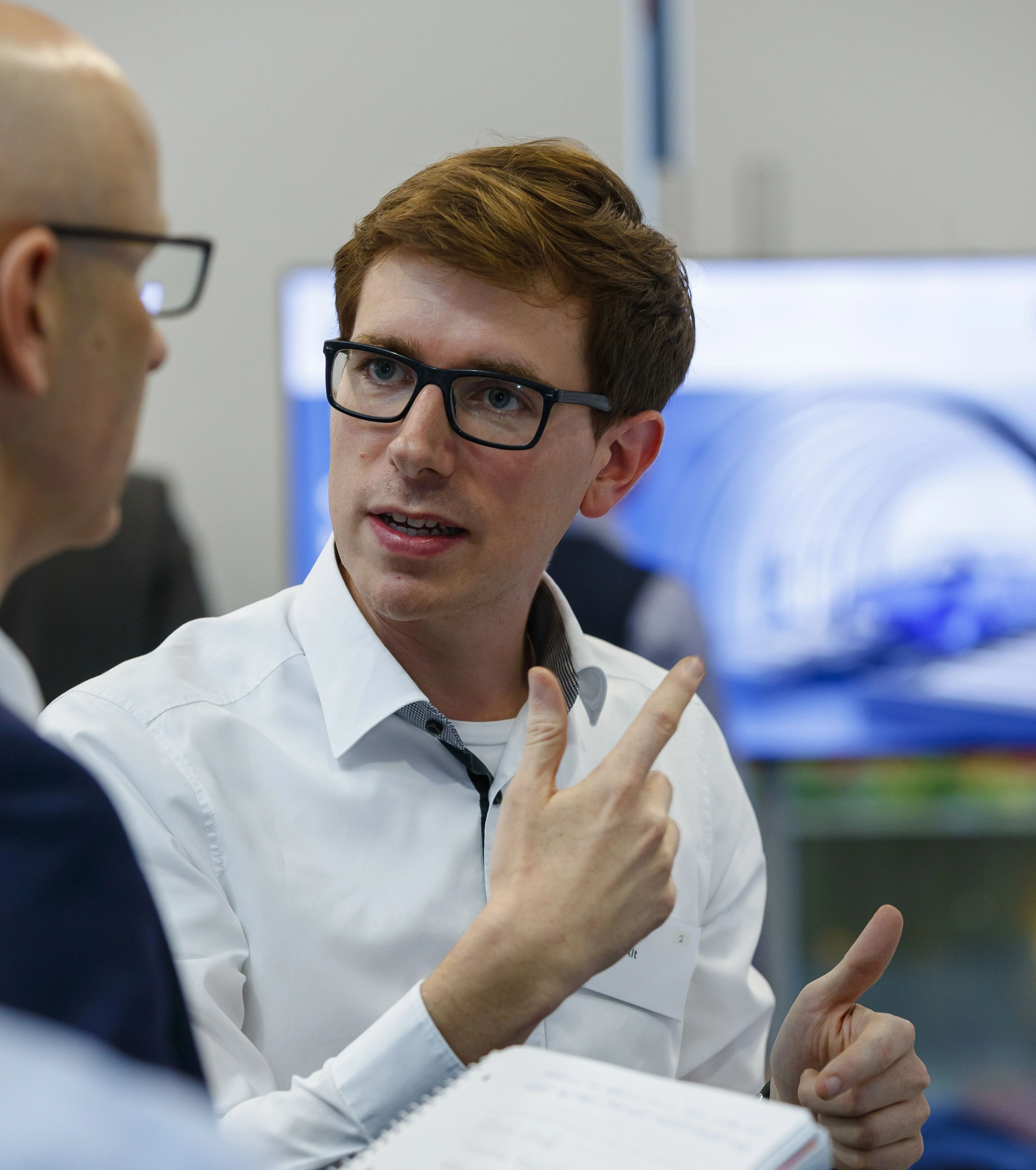
Can you give us an example of how AI is used at Dürr and what benefits it brings customers?
One good example is our new DXQplant.analytics software for the painting process. It uses machine learning to identify any quality issues that occur systematically. To do this a quality test station records any recurring defects, for instance runs or scratches in the paint. Then the recorded data from the painting process, for example from the last two years, is analyzed to ascertain what has led to the defect. So, DXQplant.analytics looks at the painting process for correlations such as: What errors occur? Which step leads to the error? The data can also be used to make predictions on how the plant will behave in the near future.
The use of AI for improving production processes is still in its infancy. What opportunities do you see for the future?
At the moment, what mostly happens is this: When an error occurs, such as a quality defect, AI identifies at which point in the plant it is caused, and notifies the operator accordingly. The cause of the error is then eliminated by a member of staff. In the future, we want to automate this manual intervention, too. This means that the plant itself will decide what needs to be done in the case of a defect and automatically change the relevant setting. Our vision is a closed quality loop. This means we monitor all processes – in the individual stations as well as in the overall plant – and the plant itself will be able to respond automatically to defects and to self-regulate. For this purpose, all Digital Factory products must work in harmony.
About the study “Artificial Intelligence in R&D”
The study examined how artificial intelligence (AI) is used in research and development work by businesses and where it has already featured in the creation of new products. It was carried out by the Complexity Management Academy, which is part of the Laboratory for Machine Tools and Production Engineering (Werkzeugmaschinenlabor – WZL) of the RWTH Aachen University.
First of all, 145 questionnaires on the use of AI were evaluated and 30 top performers identified. From this group, the Complexity Management Academy of the RWTH Aachen University selected the five leading companies. The four other corporations in addition to Dürr were 3M, ABB, Airbus and Wacker Chemie.
As part of the evaluation criterion “Portfolio Applications”, Dürr managed to score e.g. with its DXQplant.analytics software for quality assurance in automotive paint shops. A further argument in Dürr’s favor was the ADAMOS platform jointly established with partner companies for the Industrial Internet of Things. Special importance was assigned to it as part of the criterion “Technical requirements”.