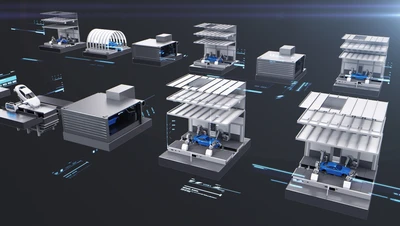
„Künstliche Intelligenz hilft, Produktionsprozesse zu optimieren“
Interview mit Dr. Simon Alt von der Dürr Digital Factory
Dürr gehört beim Thema künstliche Intelligenz zu den führenden Industrieunternehmen in Deutschland. Das ist das Ergebnis einer im Mai veröffentlichten Studie der RWTH Aachen. Die Hochschule hat bei 145 Unternehmen untersucht, wie die künstliche Intelligenz (KI) in der Forschungs- und Entwicklungsarbeit genutzt wird und wo sie bereits Eingang in neue Produkte findet. Dabei wurde Dürr als eines von fünf Successful-Practice-Unternehmen ausgezeichnet. Dr. Simon Alt von der Dürr Digital Factory in Bietigheim-Bissingen erklärt, was KI bedeutet und welche Rolle sie bei Dürr künftig spielen wird.
Der Begriff künstliche Intelligenz (KI) ist in aller Munde. Was versteckt sich dahinter?
Künstliche Intelligenz hilft uns, Produktionsprozesse besser zu verstehen und zu optimieren. Man sammelt viele verschiedene Daten aus der Produktion, zum Beispiel mithilfe der Anlagensensorik, und ermittelt Zusammenhänge und wiederkehrende Muster. Solche Daten sind zum Beispiel Prozesswerte, Stillstandzeiten oder Wartungs- und Qualitätsinformationen. Eine KI-Software erkennt, wie sich Veränderungen an einer Stelle des Prozesses auf andere Bereiche auswirken. Auf das reine Beobachten von Daten und Zusammenhängen folgt das aktive Eingreifen, also die Veränderung des Produktionsprozesses auf Grundlage der Datenanalyse. Letzteres ist im Anlagenbau momentan noch eher selten, wird aber künftig ein großes Thema werden. Dabei geht es darum, dass eine Anlage durch die Datenanalyse selbst lernt und ihre Prozesse optimiert. Die Methodik, durch die KI realisiert wird, nennt man auch maschinelles Lernen – ein Begriff, der mir besser gefällt als Künstliche Intelligenz.
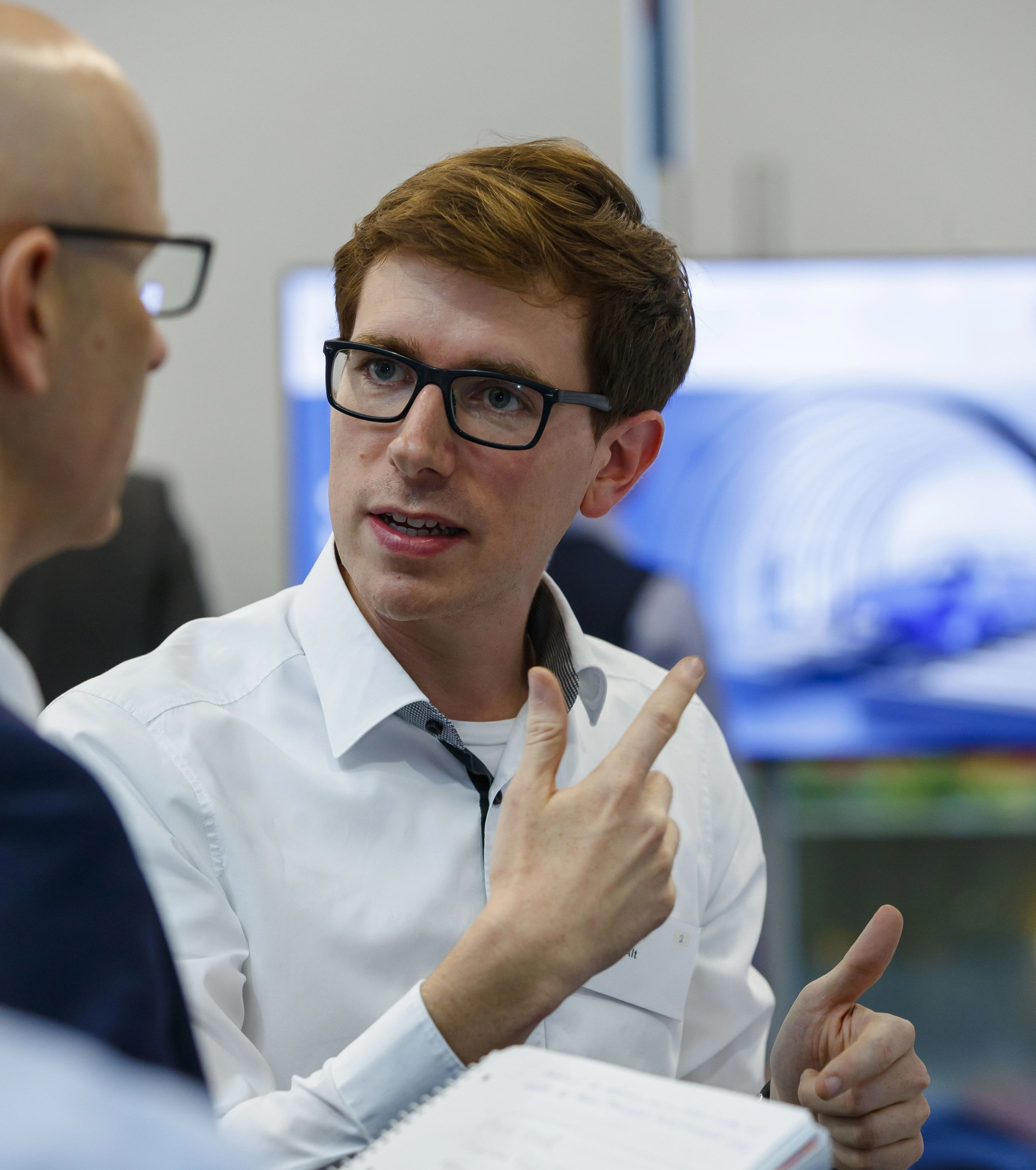
Können Sie uns ein Beispiel geben, wie KI bei Dürr eingesetzt wird und welche Vorteile das den Kunden bringt?
Ein gutes Beispiel ist unsere neue Software DXQplant.analytics für den Lackierprozess. Sie nutzt maschinelles Lernen, um systematisch auftretende Qualitätsmängel zu erkennen. Dabei werden in einer Qualitätsprüfstation wiederkehrende Mängel erfasst, zum Beispiel Läufer oder Kratzer im Lack. Dann untersucht man die aufgezeichneten Daten aus dem Lackierprozess, zum Beispiel der vergangenen zwei Jahre, um herauszubekommen, was zu dem Fehler geführt hat. DXQplant.analytics sucht also nach Prozess-Zusammenhängen in der Lackieranlage: Welche Fehler treten auf? Welcher Schritt ist der Grund für den Fehler? Man kann aus den Daten auch Vorhersagen treffen, wie sich die Anlage in naher Zukunft verhalten wird.
Die Nutzung von KI für die Verbesserung von Produktionsprozessen steht noch am Anfang. Welche Chancen sehen Sie für die Zukunft?
Momentan ist es meist so: Bei einem Fehler, zum Beispiel bei einem Qualitätsdefekt ermittelt die KI, an welcher Stelle der Anlage die Ursache liegt, und meldet das dem Betreiber. Dann wird diese Fehlerursache von einem Mitarbeiter behoben. Zukünftig wollen wir diese manuellen Eingriffe automatisieren. Das heißt, dass die Anlage selbst entscheidet, was bei einem Defekt zu tun ist und die entsprechende Einstellung eigenständig verändert. Unsere Vision ist ein geschlossener Qualitätsregelkreis. Das bedeutet: Wir verfolgen alle Prozesse – sowohl in den einzelnen Stationen als auch in der Gesamtanlage – und die Anlage ist in der Lage, auf Defekte selbstständig zu reagieren und sich selbst zu regulieren. Hierfür ist ein Zusammenspiel aller Produkte der Digital Factory notwendig.
Über die Studie „Künstliche Intelligenz in der F&E“
Die Studie untersuchte, wie die Künstliche Intelligenz (KI) in der Forschungs- und Entwicklungsarbeit von Unternehmen genutzt wird und wo sie bereits Eingang in neue Produkte findet. Durchgeführt wurde sie von der Complexity Management Academy, die beim Werkzeugmaschinenlabor (WZL) der RWTH Aachen angesiedelt ist.
Zunächst wurden 145 Fragebögen zum KI-Einsatz ausgewertet und 30 Top-Performer identifiziert. Aus dieser Gruppe ermittelte die Complexity Management Academy der RWTH die fünf führenden Unternehmen. Zu ihnen gehören neben Dürr auch 3M, ABB, Airbus und Wacker Chemie.
Dürr punktete beim Bewertungskriterium „Applikationen im Portfolio“ unter anderem mit der Software DXQplant.analytics für die Qualitätssicherung in Automobillackierereien. Ein weiteres Argument für Dürr war die gemeinsam mit Partnerunternehmen gegründete Plattform ADAMOS für das Industrielle Internet der Dinge. Sie fiel beim Kriterium „Technologische Voraussetzungen“ ins Gewicht.