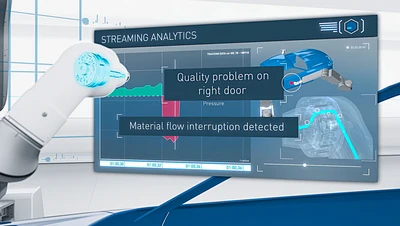
Smartes Lackieren
20.03.2020
Dürr bringt künstliche Intelligenz in die Lackierstraßen der Autohersteller.
Ganz vorne dabei sind junge Experten wie Simon Alt.
Knallige Farben, stylische Ausstattung. Im Meeting-Raum stellen sich sechs Leute in Jeans, Hemd und T-Shirt im Kreis auf – sieben weitere wählen sich per Internet ein. Die Programmierer, Datenexperten und Lackierspezialisten berichten, wo sie mit ihrer Arbeit stehen. Kurze Fragen, schnelle Antworten. Nach 15 Minuten verschwinden die Männer und Frauen wieder hinter ihren Bildschirmen. Finger fliegen über Tastaturen, Tasten klicken, die Augen gleiten über Grafiken und Zahlenreihen. Tischkicker und Sessel in den bunt eingerichteten Räumen auf dem Dürr-Campus in Bietigheim-Bissingen sind verwaist.
Simon Alt ist promovierter Regelungstechniker. Zusammen mit seinem Team arbeitet er in der Digital Factory, einem wichtigen Zukunftsbereich von Dürr, der aus rund 100 Mitarbeitern besteht. Sie entwickeln Applikationen, um die Lackierstraßen der Autohersteller effizienter zu machen – auch mit künstlicher Intelligenz. Ihre Programme durchblicken in kurzer Zeit ganze Fertigungssysteme. Sie scannen die laufende Produktion, analysieren sie und erkennen systematische Qualitätsmängel.
Alt hat vor drei Jahren bei Dürr begonnen. Heute leitet der 32-Jährige ein Team von sechs Leuten. Mit künstlicher Intelligenz beschäftigte er sich bereits an der Uni, wo er Technische Kybernetik studiert hat, eine Mischung aus Mathematik, Informatik und Ingenieurwesen. In dem Fach geht es um die Analyse und gezielte Beeinflussung technischer Systeme – einschließlich deren Modellierung und Simulation. Eines Tages werden solche Systeme womöglich Probleme lösen können wie heute ein Mensch. Für Alt eine faszinierende Vorstellung. Die Produkte von Dürr bieten ihm dafür das passende Umfeld. „Lackieranlagen sind so komplex, dass sie für den Einsatz künstlicher Intelligenz ein ideales Feld sind.“ Das Thema genießt bei Dürr hohe Priorität: „Der Einsatz von künstlicher Intelligenz im Lackierprozess beschäftigt derzeit gleich mehrere Teams, mit denen wir uns eng abstimmen.“
Die Software-Experten merken schnell, ob eine Idee in der Praxis funktioniert oder nicht. Denn ihnen stehen erfahrene Spezialisten für Lackierprozesse zur Seite. „Das ist unser Vorteil gegenüber vielen anderen Firmen, die Software für die Lackierbranche anbieten“, sagt Alt.
Lackieranlagen sind so komplex, dass sie für den Einsatz künstlicher Intelligenz ein ideales Feld sind.
Dr.-Ing. Simon Alt
Strukturierte Arbeit statt Science-Fiction
Wenn Alt über künstliche Intelligenz spricht, klingt das nicht nach Science-Fiction, sondern nach strukturierter Arbeit. „Mit künstlicher Intelligenz können wir Produktionsdaten analysieren und wichtige Erkenntnisse daraus gewinnen.“ Muss ein Ventil am Tauchlackierbecken gewartet werden? Warum stimmt die Temperatur im Trockner nicht? Gibt es einen Zusammenhang zwischen Lackfarbe und Fehlerquote? Antworten auf Fragen wie diese zu suchen kostet die Autohersteller heute viel Zeit und Geld, denn sie müssen jede Maschine und jede Anlage einzeln prüfen. Mithilfe intelligenter Algorithmen werden sich diese Fragen immer schneller, und besser und einfacher beantworten lassen.
Bei der Lösungssuche spielen unvorstellbare Datenmengen die entscheidende Rolle. Alt zeigt auf ein Schaubild. „Daten sind für uns in erster Linie alles das, was sich in einer Anlage messen lässt.“ Zum Beispiel Temperatur, Druck oder die Menge von Flüssigkeiten. Hunderte Fühler und Sensoren messen solche Werte schon heute an allen wichtigen Punkten einer Lackierstraße von Dürr. „Diese Informationen sind der Rohstoff für künstliche Intelligenz“, sagt Alt. Sie werden in einer Datenbank abgelegt und automatisch ausgewertet.
Die klugen Algorithmen setzen auf den Erfahrungsschatz. Sie vergleichen die aktuell ermittelten Werte mit denen der Vergangenheit. Sie merken, wenn Differenzen auftreten, und prüfen, ob solche Muster schon einmal zu Fehlern geführt haben. Beispielsweise lässt der Sprühdruck eines Roboters für einige Millisekunden nach. Dann wüsste das System, dass die Ursache höchstwahrscheinlich ein defektes Ventil ist. Ein schneller Check der Lackierergebnisse würde verhindern, dass ein mögliches Qualitätsproblem erst in der Endkontrolle aufgedeckt wird – und viele Fahrzeuge bereits davon betroffen sind. „Außerdem erlaubt die intelligente Ursachensuche Prognosen darüber, wie lange ein Bauteil vermutlich noch hält“, sagt Alt. Teure Ausfälle der laufenden Produktion ließen sich beispielsweise durch einen Teiletausch an betriebsfreien Tagen verhindern. Eine solche Analytics-Funktion wird aktuell mit der → Software DXQequipment.analytics den Kunden vorgestellt.
Die → Dürr-Software DXQplant.analytics nimmt nicht nur die einzelne Maschine in den Blick, sondern die gesamte Lackieranlage. Die Algorithmen erfassen, wenn sich beispielsweise jeden Montag die Mängel bei blau lackierten Karosserien häufen. Sie werten Millionen von Daten aus und forschen nach der Ursache. Die Fehlerquelle kann eingegrenzt werden. Womöglich deuten ungewöhnliche Messwerte im Farbmischraum darauf hin, dass bei der Routinereinigung am Wochenende immer derselbe Fehler passiert. Normalerweise fahndet das für die Optimierung zuständige Personal in den Autowerken oft Tage nach solchen Ursachen. Ein riesiger Aufwand. Zukünftig wird das viel schneller gehen. Dafür steht → DXQplant.analytics.
Können Maschinen wie Menschen handeln?
Bislang wertet die Software Informationen aus und gibt Handlungsvorschläge. Noch müssen meistens Menschen diese Vorschläge in die Tat umsetzen. Alt und seine Kollegen arbeiten jedoch daran, dass die Anlagen von Dürr sich eines Tages selbst regulieren. „Bei diesen Fragen steckt die künstliche Intelligenz noch in den Kinderschuhen“, sagt Alt. Sein Team forscht beispielsweise mit der Methode des Reinforcement Learning (Bestärkendes Lernen). Eine Software wird dabei so programmiert, dass sie sich belohnt fühlt, wenn sie Fortschritte macht. So wie ein Hund, der ein Leckerli bekommt, wenn er gehorcht.
„Vorstellbar wäre sogar, dass das gesamte Automobilwerk in ein sich selbst regelndes System einbezogen wird“, sagt Alt. Produktionsprozesse würden dann automatisch so umgestellt, dass beispielsweise eine Problemmaschine die Fertigung möglichst wenig behindert. Eventuell ließen sich sogar Lieferketten umleiten.
Bis es so weit ist, bleibt Simon Alt und seinem Team noch einiges zu tun. Mit Sicherheit finden sie bis dahin auch mal wieder Zeit für ein Spiel am Tischkicker.
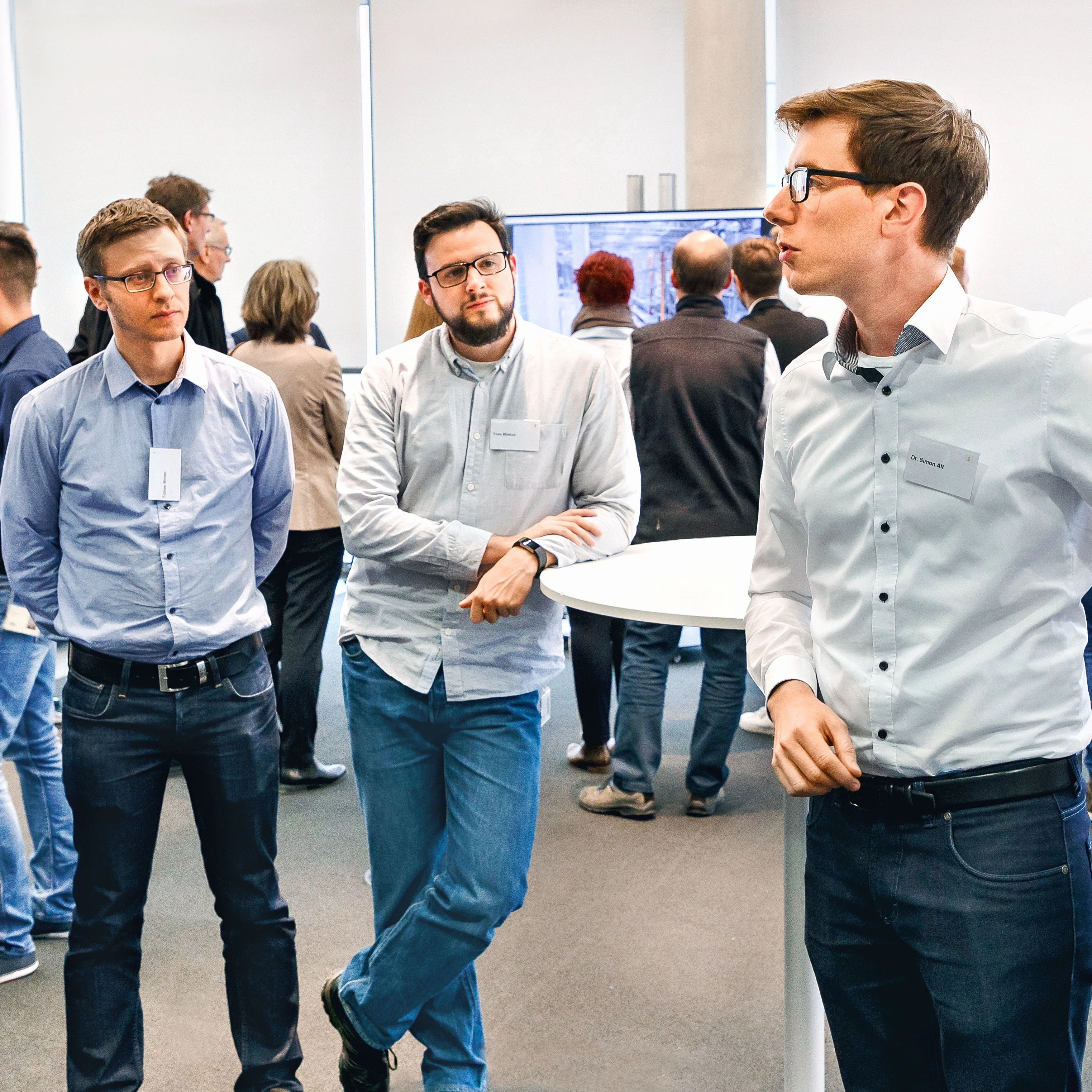