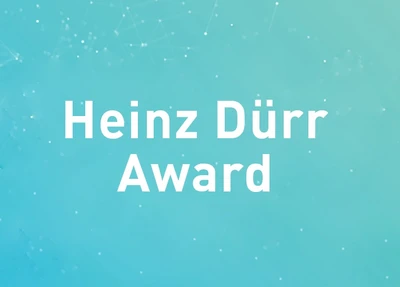
Service-oriented, digital, sustainable, innovative
Sep 17, 2021
Heinz Dürr Awards for outstanding performance by employee teams
The Heinz Dürr Awards represent an award with a long-standing tradition in the Dürr Group. A jury honors outstanding achievements by teams of employees. Our customers and the environment also benefit from innovative and sustainable products, digital solutions or special service efforts – as the current winning projects prove.
Innovation category
Project: Overspray-free painting with EcoPaintJet / EcoPaintJet Pro robot painting system
The EcoPaintJet robot painting system applies paint over large areas or in simple patterns with high edge definition. 100% of the paint lands on the surface without any waste, two-tone painting can be applied fully automatically with this technology – and all this in a faster, more energy-efficient and resource-saving manner than before.
The treatment of the air inside the paint shops and the disposal of the overspray, which is produced during paint application with atomizers, leads to a tremendously high energy consumption. In addition, up to 15 sqm of masking tape is used for multicolored paintwork. When masking, the manual fixing and removal of the masking tape takes about 50 minutes. In the end, the tape becomes hazardous waste. Since much less air has to be treated during overspray-free painting, the energy consumption in a paint booth can be reduced by 50 to 65 percent and prior masking is no longer necessary.
The EcoPaintJet robot painting system has already reached series production and is used for the two-tone painting of the car bodies. The further development EcoPaintJetPro is currently being tested by three automotive manufacturers. One of them will be using it next summer in series paint application.
Project: 100% production transparency with digital value stream optimization
Moving parts, short throughput times and different types of machines of different ages – all this makes production data collection and value stream measurement in the wood and furniture industry a challenge.
The HOMAG subsidiary SCHULER Consulting – part of the Dürr Group – has developed a simple solution for the analysis of the value stream – i.e. all value-adding and non-value-adding work stages for the manufacture of a product. With the help of digital technologies, production data is captured regardless of the machine type, manufacturer or area of application – and without a great deal of personnel effort or high implementation costs.
Here, the smartphone takes over the external sensory monitoring of machines and workstations. It captures vibration, acceleration and many other movement data. The smartphone does not have any software interfaces and can therefore run completely externally. In interaction with Bluetooth low energy beacons as a signal station, it can locate objects such as stacks in production. Based on these movement profiles and location data, SCHULER Consulting identifies redundant and cost-intensive processes and develops optimization measures. At the touch of a button, customers can find material stacks they are looking for in their production, view the progress of current orders or obtain processing times and automatically generated unit costs.
Project: Dynamic expansion measurements of rotors: Spin test system functions extended
In spin test systems, technicians test the load limit of rotors – at up to 240,000 revolutions per minute. Naturally, deformations occur in the process, but these must remain within defined limits.
In the past, spin test systems were used exclusively to determine the speed at which the material bursts. A development team at Dürr’s subsidiary Schenck RoTec has now supplemented these systems with digital measuring technology and modern software, turning them into high-tech products. By using optical sensors, laser beams and electrical fields, deformations of the rotor surface can be traced in detail at any speed. The insights acquired are incorporated into the development of the rotors. In this way, costs can be reduced, and the energy efficiency and service life of these high-speed drives can be improved, for example for electric vehicles, but also for aircraft engine components.
With the additional features, the spin test systems have established themselves as service products that are in very high demand. Some customers have even bought the complete system from Schenck RoTec.
Customer Experience category
Project: Service deployment: Emergency at Volvo Truck in Dublin, Virginia
A massive water ingress in the compressed air system at Volvo Truck in Dublin, Virginia, damaged 67 regulation units (transducers), among other things, and caused a production stop. The regulation units precisely control the compressed air that drives the atomizers of Dürr painting robots. Around 2,500 employees had to suspend their work after the incident.
Therefore, the service hotline of Dürr in the USA received an urgent emergency call. The 67 regulation units had to be replaced as quickly as possible. However, such a large quantity could only be flown in from Germany. Overnight and with great effort, German and US- employees organized the spare parts and the international transport. After just over 24 hours, Volvo Truck received the delivery of the new equipment.
In a thank-you letter, the site managers applauded Dürr for this outstanding achievement. The service team had thus spared Volvo Truck a lengthy production downtime and arranged for the replacement of the numerous control units in record time.
Newly introduced Sustainability category
Project: Process for the provision of district heating by reduction and utilization of landfill gas
The main cause of climate change is greenhouse gases – these include methane and carbon dioxide. Both substances are also produced in landfills. In Sweden, 2% of the country’s greenhouse gas emissions originate from landfills. The landfill operators therefore burn the waste gases in purification plants and in this way feed district heating networks.
However, this process is reaching its limits due to a decrease in the proportion of organic waste. As a result, the methane content is no longer high enough to ignite a flame and initiate combustion. The result: The operators have to add fossil fuels – which is inefficient and harmful to the environment.
Dürr Megtec installed a flameless system called the Vocsidizer at Gotland Energy (Sweden). The system (new product name: Oxi.X RV) works according to the principle of regenerative thermal oxidation (RTO) but does not require a burner or combustion chamber. The ignition takes place with an electrically-powered heating coil. This means that the plant needs less methane but can still ignite and burn the exhaust gases. The heat generated in this way is sufficient to heat 100 single-family homes throughout the year.
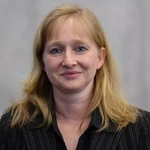
Martina
Bausch
Officer Online Magazine
Corporate Communications & Investor Relations
Dürr Aktiengesellschaft
Carl-Benz-Str. 34
74321 Bietigheim-Bissingen
Germany
Carl-Benz-Str. 34
74321 Bietigheim-Bissingen
Germany