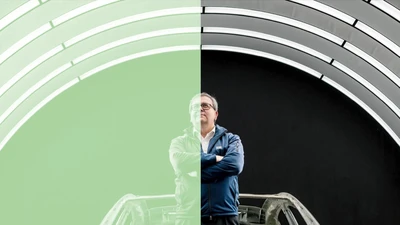
Turning old into sustainable
Mar 17, 2022
Sustainability is becoming a focus of attention also for vehicle manufacturers. Dürr is positioning itself as a partner for the green ambitions of its customers. Damir Wagner is a Key Account Manager in the service department and supports automakers in retrofitting their existing plants with resource-saving and low-emissions technologies.
Damir Wagner prefers to be on site with his customers. Yet due to the coronavirus pandemic, this is currently not always possible as much as usual. And still: Grabbing a cup of coffee in the morning and booting up his computer is the only constant in his workdays. “Every day is different; it always depends on what my customers need at the time,” says the 59-year-old. Wagner is a Key Account Manager at Dürr. In this function, he supports Volkswagen and other automotive manufacturers, offering so-called plant assessments for upgrades of existing paint shops. This is a market that promises strong growth for various reasons.Damir Wagner prefers to be on site with his customers. Yet due to the coronavirus pandemic, this is currently not always possible as much as usual. And still: Grabbing a cup of coffee in the morning and booting up his computer is the only constant in his workdays. “Every day is different; it always depends on what my customers need at the time,” says the 59-year-old. Wagner is a key account manager at Dürr. In this function, he supports Volkswagen and other automotive manufacturers, offering so-called plant assessments for upgrades of existing paint shops. This is a market that promises strong growth for various reasons.
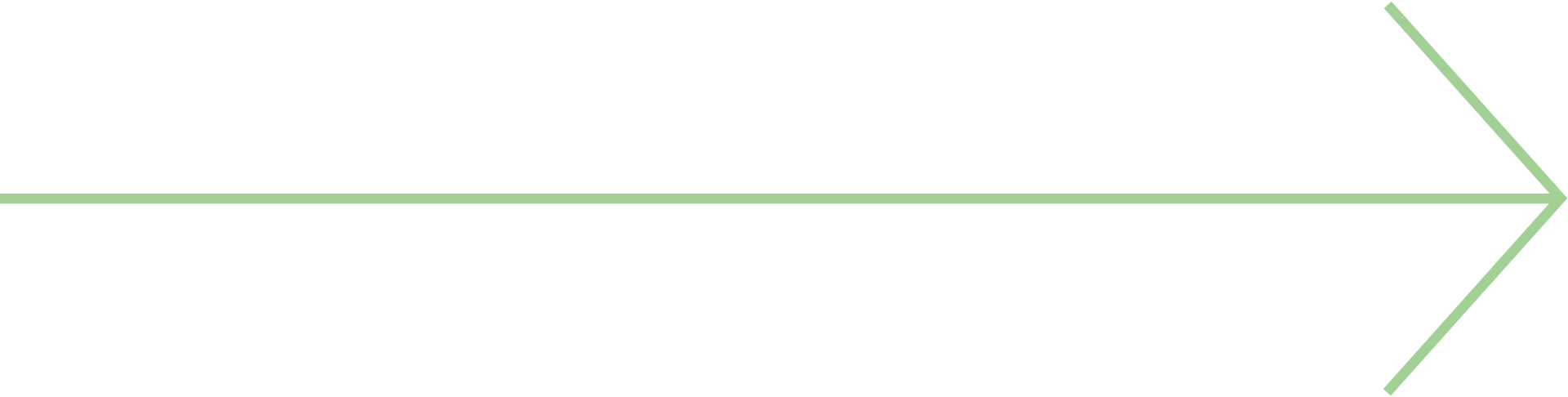
10%
less energy is required by automakers during the entire production of a vehicle, thanks to the EcoDryScrubber
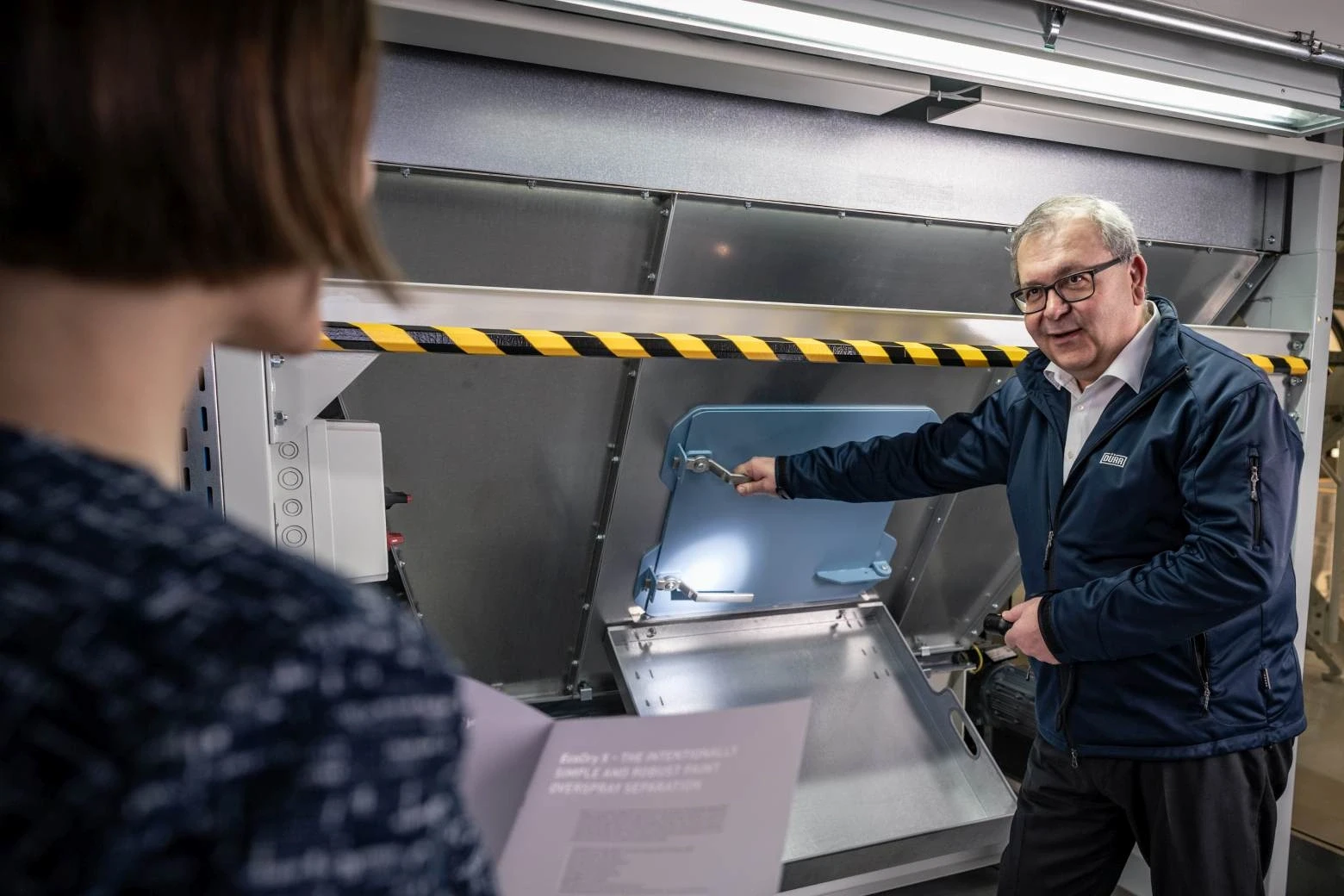
Why an upgrade is worthwhile
More than 60 percent of all paint shops in the automotive industry worldwide are over 20 years old and therefore often no longer up to date. Outdated technologies increase the need for maintenance and cause high operating costs. In addition, there is the risk that old equipment will fall short of the growing environmental standards. Plus, they often no longer meet the automakers’ own requirements for energy-efficient and sustainable production.
But the costs for building a new paint shop are sometimes in the three-digit million euros. With figures like these, it is worthwhile for a company to take a closer look at whether its existing equipment can be modernized for significantly less money. Another advantage: While a new plant usually takes more than a year to build, Dürr can generally carry out necessary upgrades within a few weeks, sometimes even during ongoing operation.
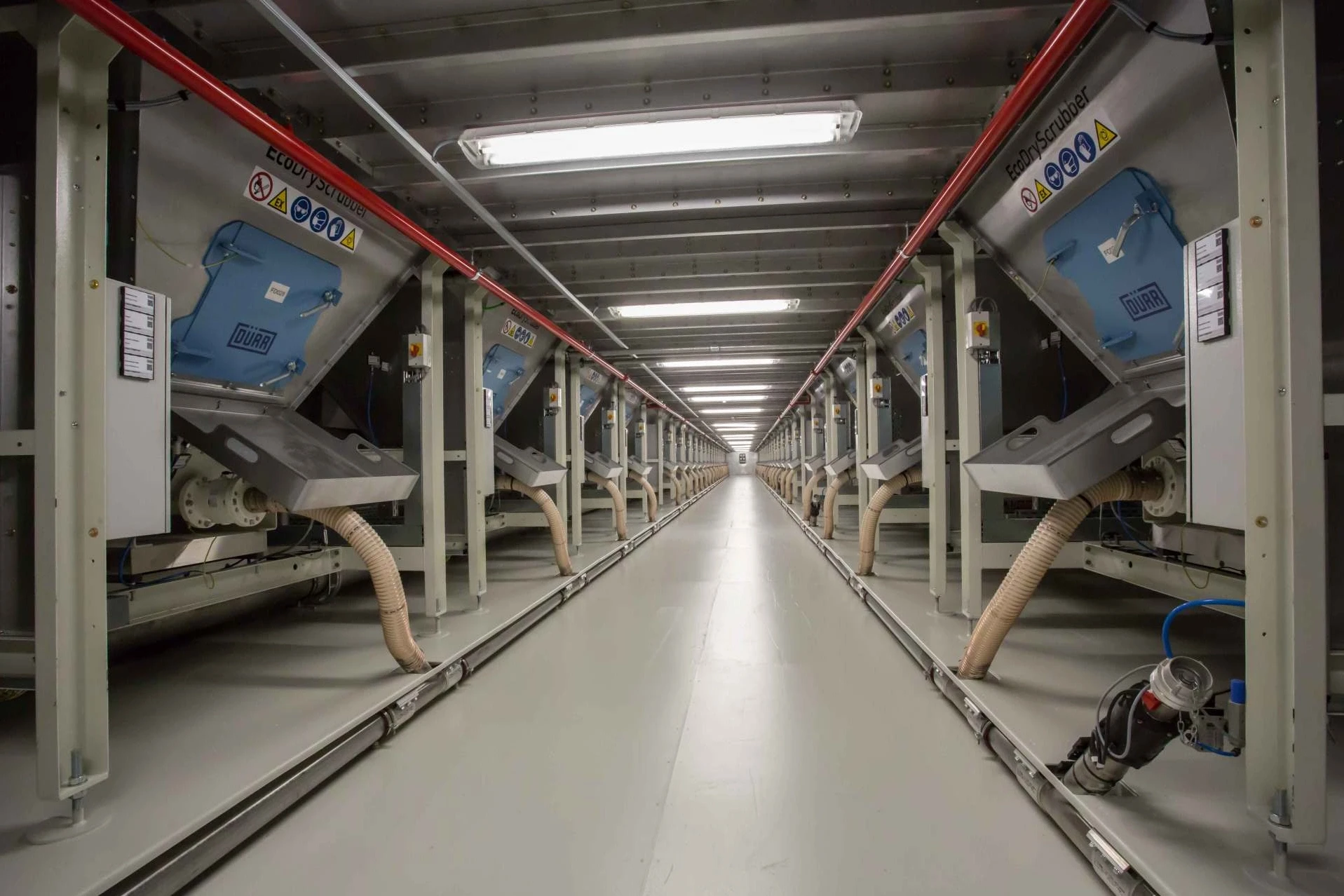
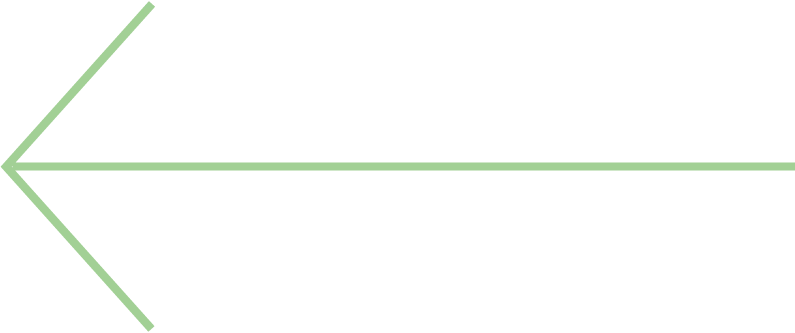
33%
lower CO2 emissions in the paint shop after switching to the EcoDryScrubber
Assessment only takes seven to twelve days
“Today, new paint shops are almost exclusively being built in Asia,” Wagner explains. “In other regions, for example in Europe and North America, we examine the existing plants and see what can be done there.” And there is a wide range of options that Dürr offers its customers, tailored to their needs. During the assessment, which usually takes between seven and twelve days, a team from Dürr first checks the equipment and analyzes the relevant data. Subsequently, a tool calculates the savings potential. On this basis, Dürr experts discuss various measures that are then implemented according to the customer's wishes. “There is no such thing as impossible when upgrading an existing facility,” Wagner says.
In his experience, the automakers’ biggest concern is that the conversion measures will lead to longer production downtimes. For the modernization of paint booths, Dürr has therefore developed a step-by-step conversion concept in which the individual steps can be implemented during the regular plant closures over the company holidays, when the assembly lines in the production halls are at a standstill anyway.
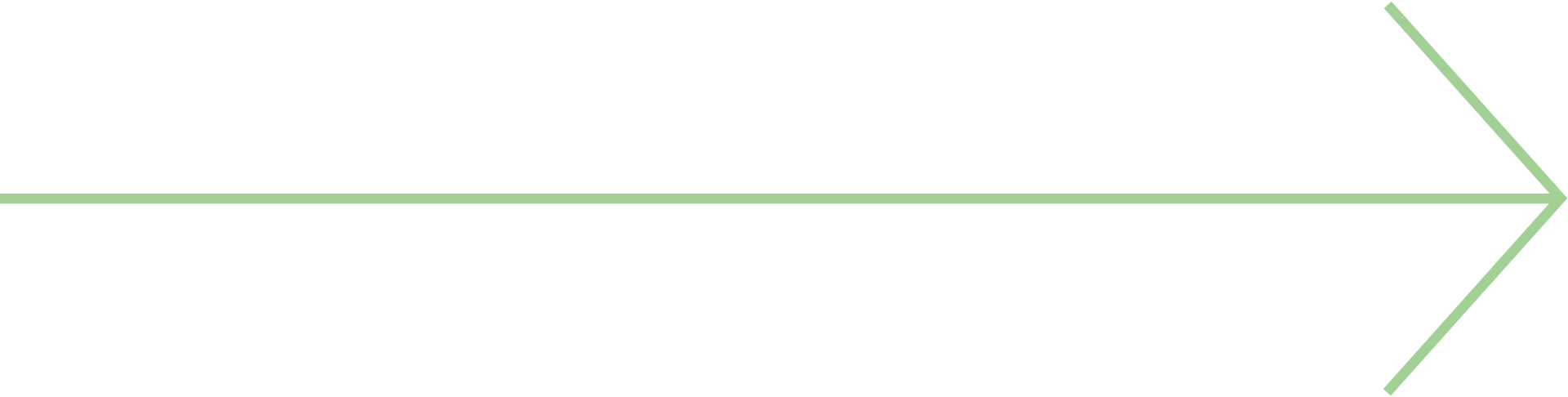
by 2050
many automotive manufacturers want to be carbon neutral
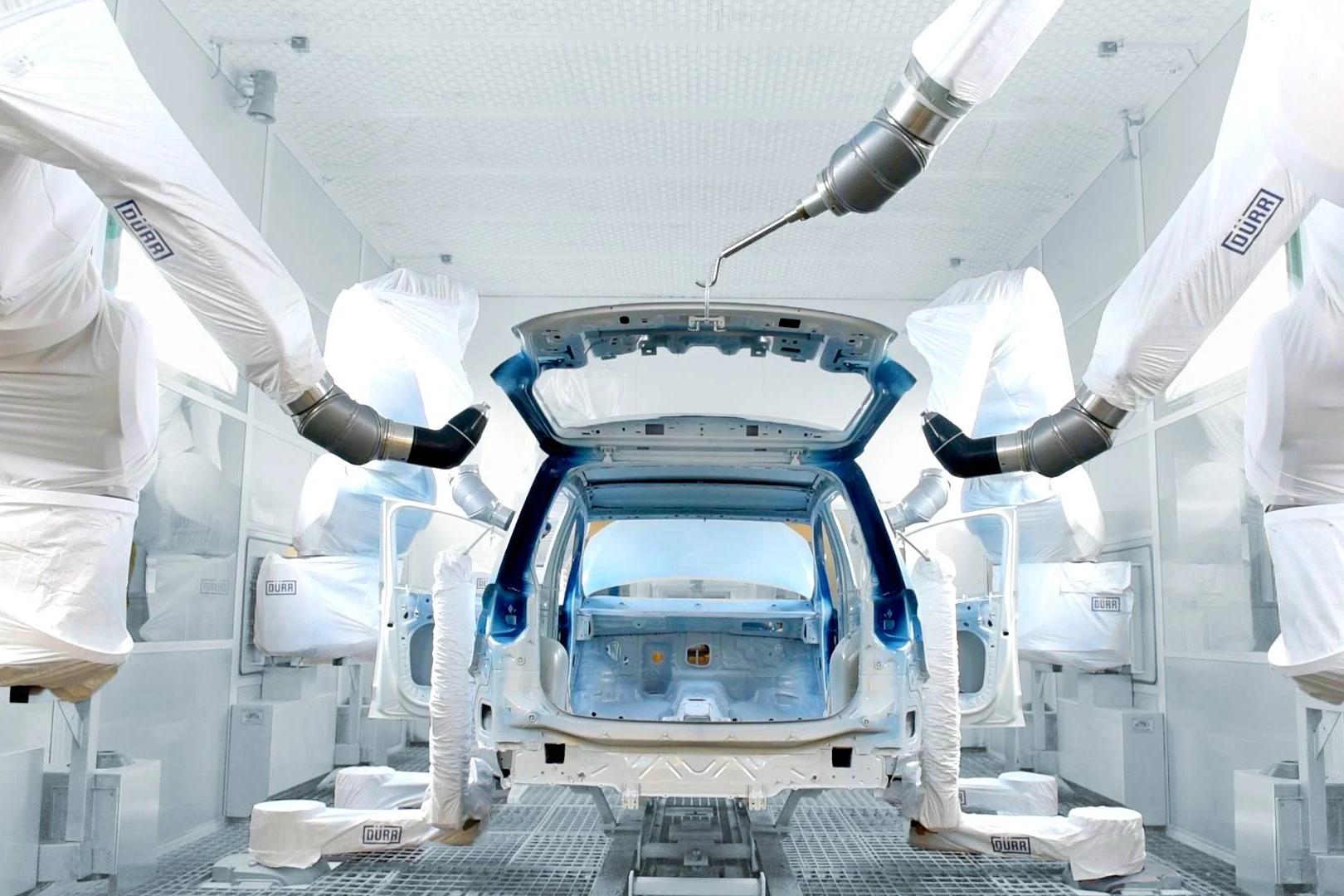
Paint separation as the biggest lever
The most effective step on the way to more sustainability in the paint booth is Dürr’s EcoDryScrubber. Unlike conventional processes, this system does not separate the excess paint particles — the so-called overspray — using water and chemicals. Instead, it uses limestone powder as a natural bonding agent. The effect: The elaborately conditioned booth air remains dry and can therefore be used several times. Wastewater treatment and the disposal of paint sludge are also no longer required.
The switch from wet to dry separation alone reduces energy consumption in the entire paint shop by around 25 percent. CO2 emissions decrease by as much as one third. If you consider the complete manufacturing process of a car, these savings also make a difference: Here, energy requirements can be reduced by 10 percent — a huge lever on the way to a more sustainable automotive factory.
The market for such solutions is considerable: In Europe alone, around 200 painting lines are still operating with wet separation — and Dürr is asserting its position as market leader in the conversion to the dry and significantly more sustainable alternative. Wagner sees several reasons for this.
There is no such thing as impossible when upgrading an existing facility.
Damir Wagner , Key Account Manager in the service department
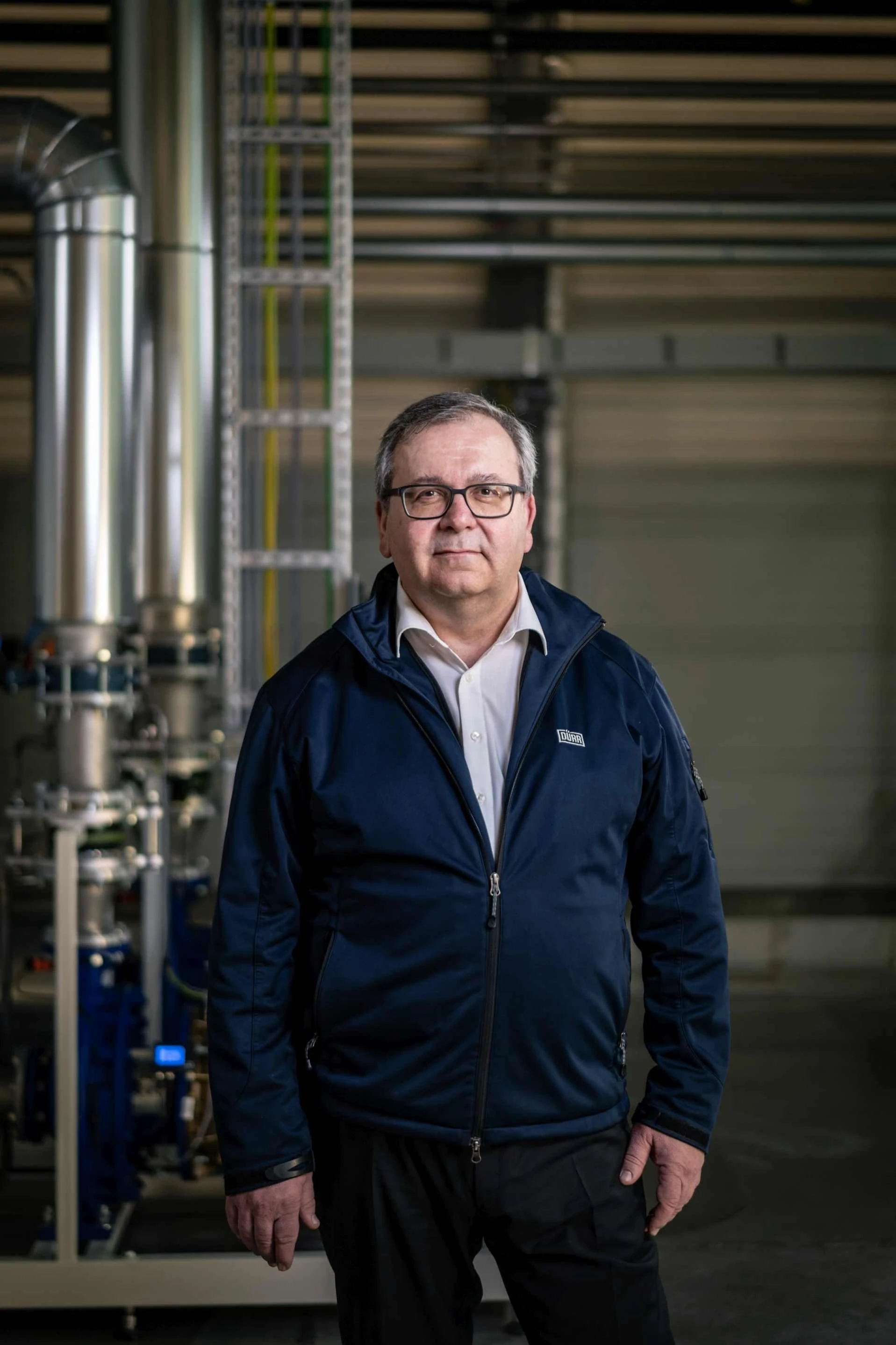
Experience and personal contact
Dürr, for one thing, offers comprehensive solutions from a single source, ranging from application technology to central control — all technically coordinated and highly efficient. For another, Dürr also supports the systems of other manufacturers. And then there are the many years of expertise of the company and its employees. The assessment of a plant only works in a team combining different perspectives and approaches. Professional experience is a very important factor here. “You are dealing with old equipment,” Wagner says. “Young colleagues first have to familiarize themselves with the technology of 20 years ago. So, it is good to have someone with the appropriate knowledge and experience on your team.”
Wagner has been with Dürr for 32 years. Having worked in spare parts sales and as a project manager, he moved up the ranks to become department manager. For the past two years he has been responsible for important key customers in the service area sales department. In doing so, he benefits greatly from his knowledge about Dürr and its products that he has acquired over the decades.
But in addition to expertise and solutions from a single source, there is another important factor: personal contact with customers on site. A close relationship of trust has grown with many of them over the years. “Of course, it is better if I can put across the benefits of our solutions to customers in personal meetings,” says Wagner. “Above all: The activity is at the customer’s site. Only when I can see the situation with my own eyes do I know what I have to do after that.”
Sustainability booster
The paint shop accounts for almost half of the energy consumption in automotive production. At the same time, the painting process offers many approaches for reducing energy, material, and space requirements as well as CO2 emissions. Dürr specifically develops products that help reduce the ecological footprint of paint shops. There is also a lot of green potential in digitalization.
The best way to remove overspray
No single measure is as effective in the sustainable modernization of old paint shops as the switch from wet to dry separation. Natural product instead of chemicals and recirculation instead of energy-intensive fresh air treatment: The EcoDryScrubber is the must-have for environmentally conscious plant operators.
Find out more about → EcoDryScrubber.
A revolution in car body curing
A lot of energy must be expended for curing freshly applied paint coats, particularly for heating the car body. Since this energy has previously come from natural gas, the oven has a negative impact on the automakers’ carbon footprint. This changes with the EcoInCure oven for innovative car body curing. The oven can be heated electrically so that significant amounts of CO2 can be saved using power from renewable energy sources: around 40% in the entire paint shop. In addition, this innovative oven reduces overall energy consumption through efficient utilization of waste heat and its compact design. Thanks to the reduced housing surface, there is less heat loss into the production environment.
Find out more about → EcoInCure.
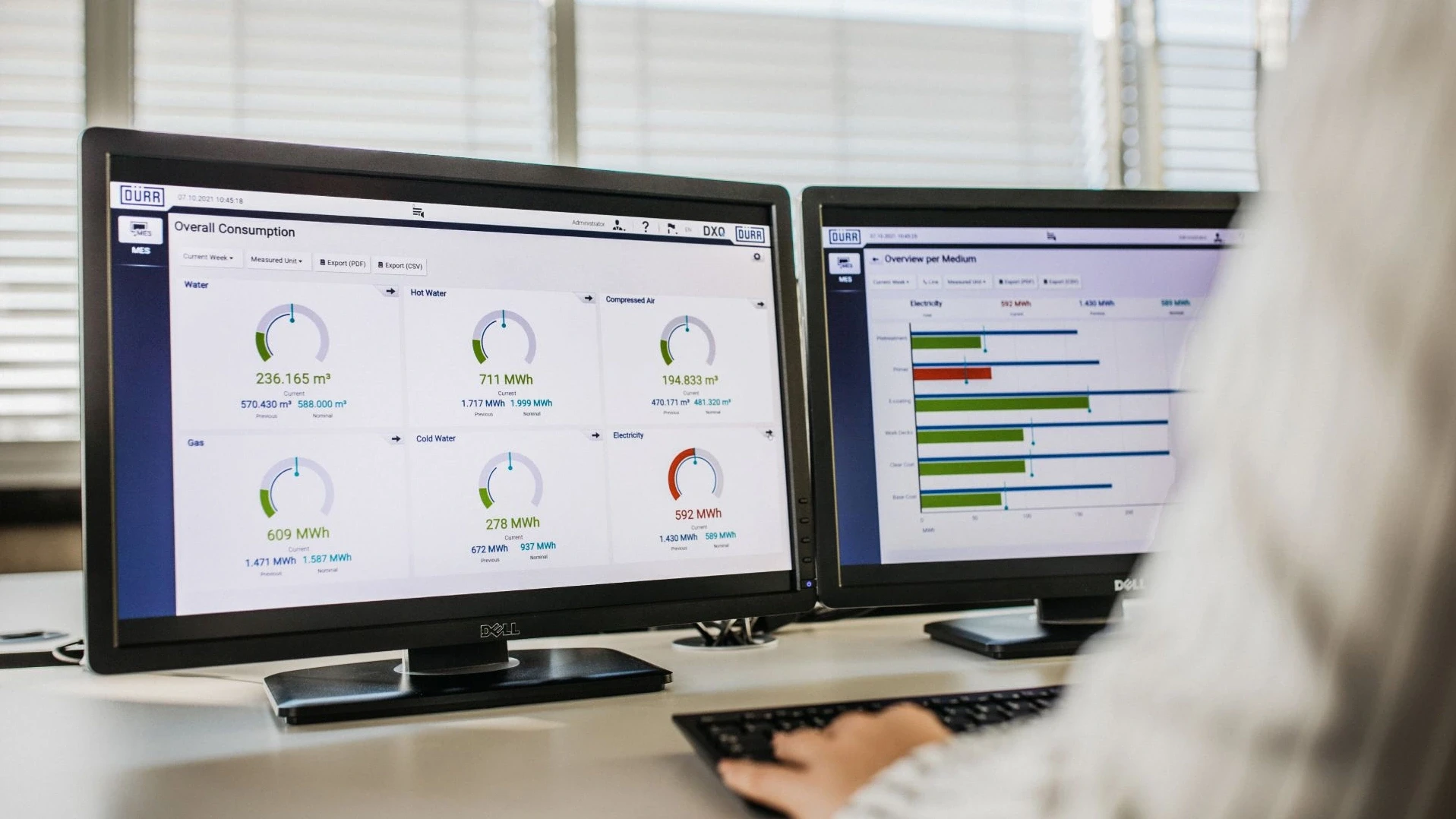
Intelligent energy management
The DXQenergy.management control software can be used to identify savings potentials throughout the paint shop. The smart application monitors consumption values and enables uncomplicated analysis of energy requirements for any period of time. On this basis, plant operators have the opportunity to investigate deviations, find causes, and optimize energy requirements. The focus is on transparent and consumption-oriented production without compromising overall equipment effectiveness. The software can also be retrofitted in existing paint shops.
Find out more about → DXQenergy.management.
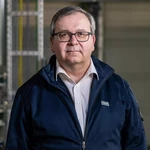
Damir
Wagner
Key Account Manager Service
Dürr Systems AG
Carl-Benz-Straße 34
74321 Bietigheim-Bissingen
Germany
Carl-Benz-Straße 34
74321 Bietigheim-Bissingen
Germany