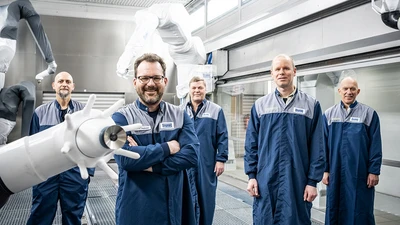
Don’t lay it on too thick
Mar 17, 2022
A uniform layer of paint is an important quality feature for cars. Adapting paint shops to this requirement is complex. New simulation software from Dürr makes this task easier and reduces the number of tests with real car bodies.
The mouse pointer moves along the virtual car body and stops over the hood. Tjark Bringewat has discovered a problem area. “Too little paint is being applied here,” says the software developer, describing small circles on the corresponding spot with the cursor. Then he repeatedly varies the settings of the program and starts new simulations.
Tjark Bringewat works at Dürr’s Digital Factory, a cross-departmental software competence center. He clearly enjoys the digital tool that he helped develop. It is a new module that makes an existing application even better. With the Dürr DXQ3D.onsite software, it was previously possible to program and simulate the work of painting robots. Users could check on the screen whether the robots were reaching all the relevant points along the car body on their pre-programmed paths and what clearance they needed to avoid getting in each other’s way. In addition, users were able to check compliance with the scheduled cycle time with the help of the digital twin. “Now, the thickness of the paint layer can also be estimated, visualized, and digitally optimized from the user’s desk,” says Bringewat.
Automobile manufacturers had requested this additional module, because it considerably simplifies the complex configuration of painting lines. This work is always necessary when a plant is newly commissioned, or if the paint or the vehicle model to be painted is changed. A five-member team of software developers and application technology specialists spent two years working on the new digital tool.
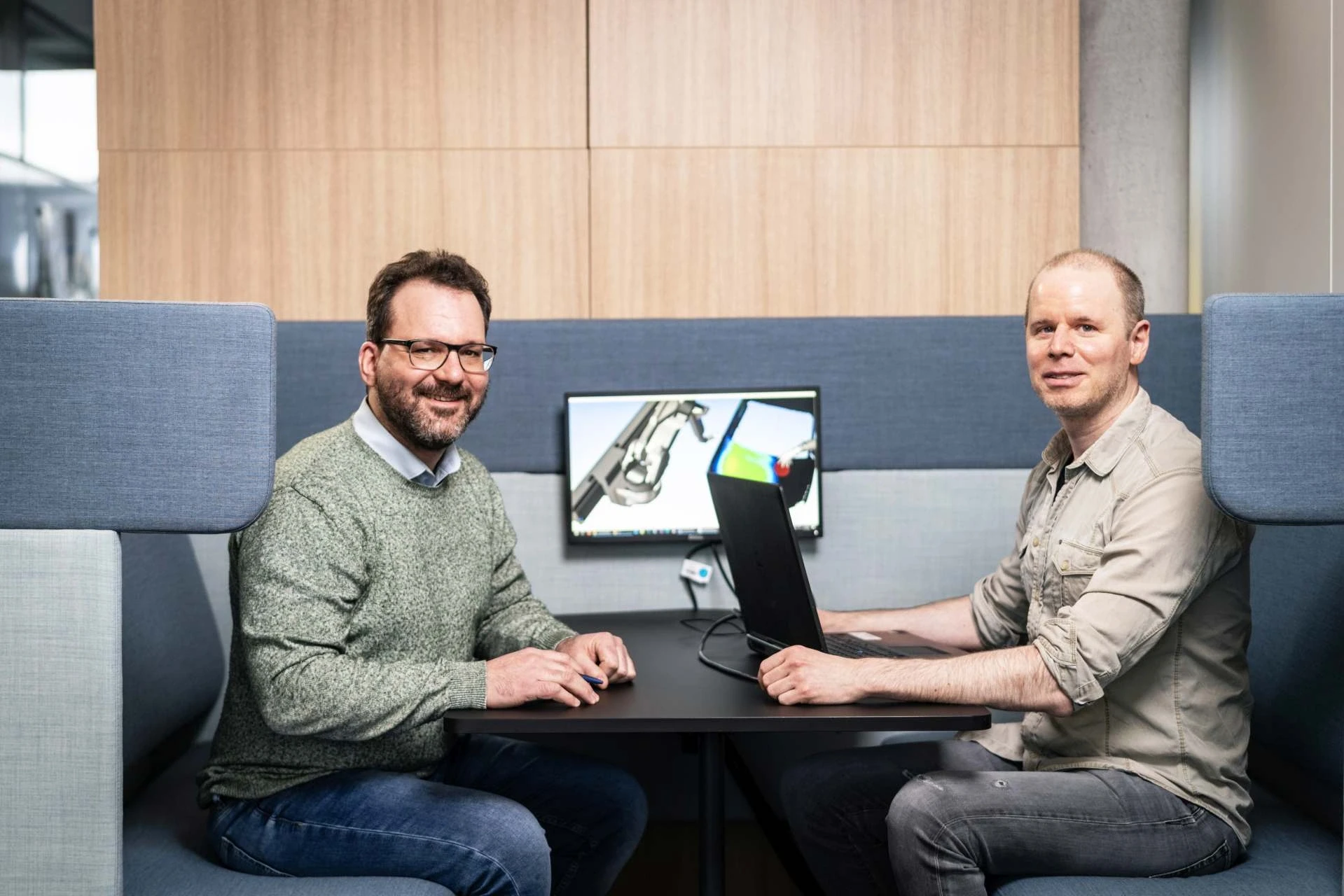
Christoph Heckeler and Tjark Bringewat are in a great mood as they take a look at the simulation tool together.
The thickness of the paint layer can be optimized from the user’s desk.
Tjark Bringewat , software developer
Fewer car bodies go to scrap
Before a painting line starts up, a team of experts has to set up all the procedures with utmost precision. The size and shape of the car bodies, but also the color and type of paint play a role in the process. All parameters must be coordinated before the start of operations. This takes weeks and is expensive, since manufacturers have to provide car bodies specifically for this purpose and send them through the painting line on a trial basis. After each test run, they are checked for errors and the configuration is adjusted if required. Depending on the model, ten or more car bodies may be painted and then sent to scrap. The new software, however, allows the settings for a paint layer that is as uniform as possible to be optimized on the PC so that a large part of the time-consuming test runs can be eliminated.
Painting car bodies is a science in itself: The appropriate amount of paint must be applied at each point. How much that is in each case is not very easy to determine in advance. After all, car bodies are complex structures. If the robot arm with the atomizer wanders over a boldly curved hood, the paint layer can vary in thickness at different points.
Problems like this can be easily solved with the new tool. The program creates its own 3D file format of the car body. It only takes into account information that is relevant for the simulation. This reduces memory space and computing time and has a decisive advantage: The simulation can be performed not only on mainframe computers, but also on normal computers such as those installed in paint shops. At the click of a mouse, the car bodies can be painted virtually within a few minutes.
In order to prove this, Tjark Bringewat starts the software on his notebook. Several clearly-arranged buttons appear on the screen, with a car body in the middle. It is flanked by four animated robots spraying paint. The car body is still black, but various color fields are gradually emerging. They show the thickness of the paint layer in the various areas of the car body. Red-colored areas indicate that the paint layer is too thick, while blue areas could use more paint, Bringewat explains.
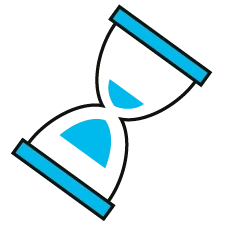
5 min
is roughly what the simulation tool needs to paint a car body virtually
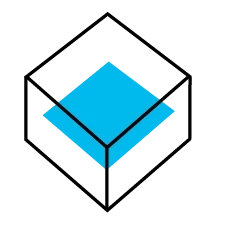
3D
Visualizations of the car body illustrate the painting result
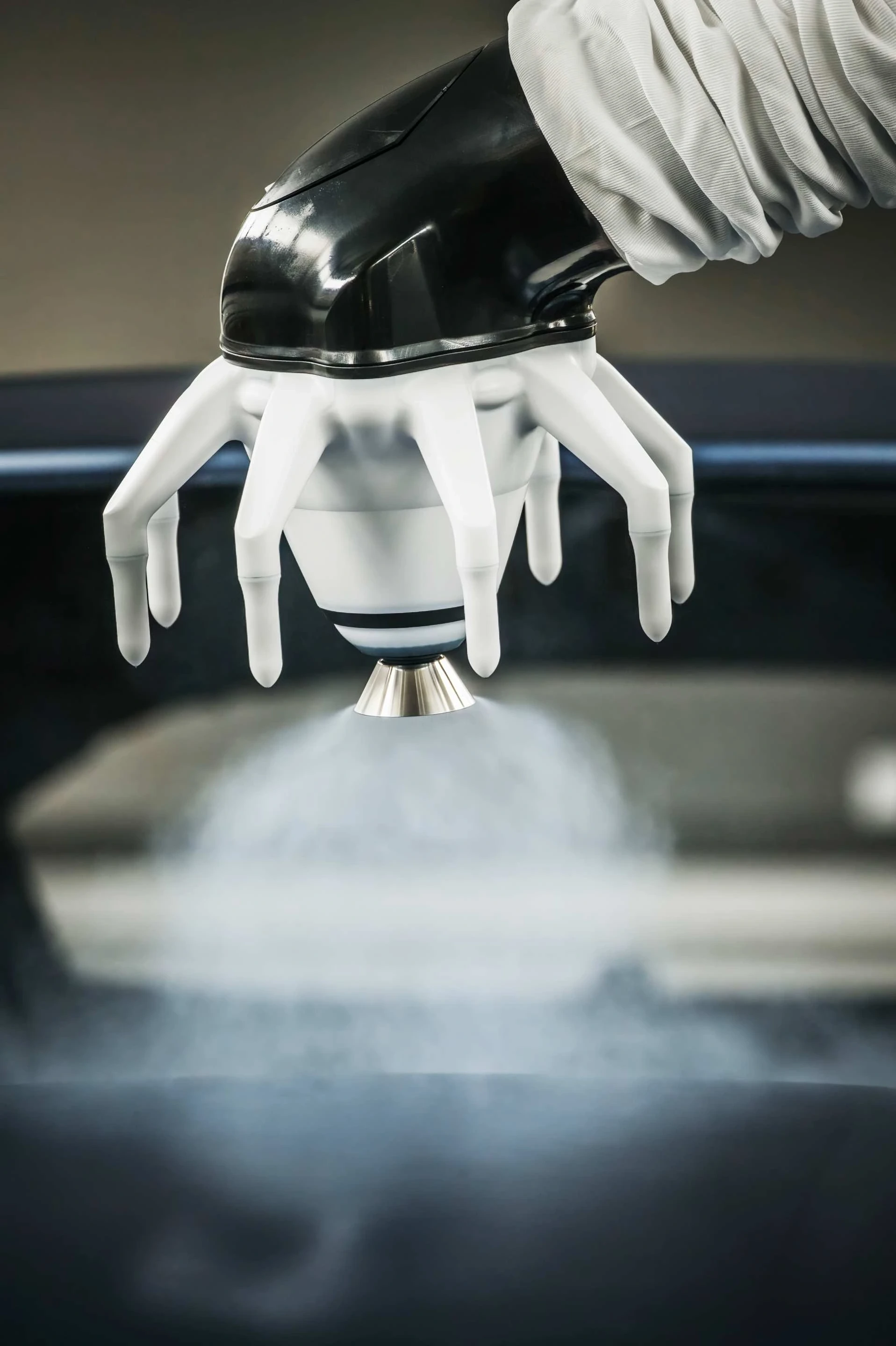
Not even half a millimeter thick and yet crucial: A uniform layer of paint is considered an important quality feature for cars.
A dictionary from the lab
The program allows the simulation of various scenarios in order to improve the quality of the paint application. This works, among other things, by setting two variables. One of them is the so-called spray pattern width. It shows the surface area covered by the paint particles flying out of the atomizer and can be compared in a figurative sense to the width of a brush. The other variable is the percentage amount of paint that comes out of the spray head.
“Here, we have greatly simplified the actual painting process,” explains Christoph Heckeler, application process developer at Dürr. It is not actually possible simply to adjust the spray pattern width and the percentage paint flow rate. In fact, they result from the properties of the paint used and specific operating parameters such as the painting distance and the speed of the atomizer.
But instead of taking these influencing variables into account as early as during simulation, the development team only considers them in a second step. This happens in real-life tests in the Dürr laboratory — not on car bodies, but on small test panels. This is easier, cheaper, and just as good. The values of these laboratory tests are reflected in digital feature maps and relate the behavior of atomizer and paint to the optimized parameters from the simulation tool. “You can think of the result as a dictionary,” Heckeler says.
In the simulation program, we have greatly simplified the actual painting process.
Christoph Heckeler , application process developer
It is fed into the simulation program, and the software automatically translates the previously determined virtual parameterization into settings for the real paint job. “The first test painting of a car body is then carried out with this pre-optimized parameter set,” explains Heckeler. This makes commissioning more efficient and enables automakers to achieve saleable paint quality faster. In addition, the new digital tool reduces material costs and results in fewer unevenly coated car bodies. Depending on the initial situation, the number of car bodies that go to waste through test runs is estimated to be reduced by up to 50 percent. A beta version of the simulation tool, which has been in use at some automotive manufacturers, has already proven its worth. Now the product is ready for the market.
Heckeler doubts that one day test runs with real car bodies will no longer be necessary. “The painting process is too complex for that.” But Dürr will, of course, develop further ideas to make painting more economical and sustainable. The simulation of the painting process is just one of many important building blocks on the way to a fully digitalized paint shop.
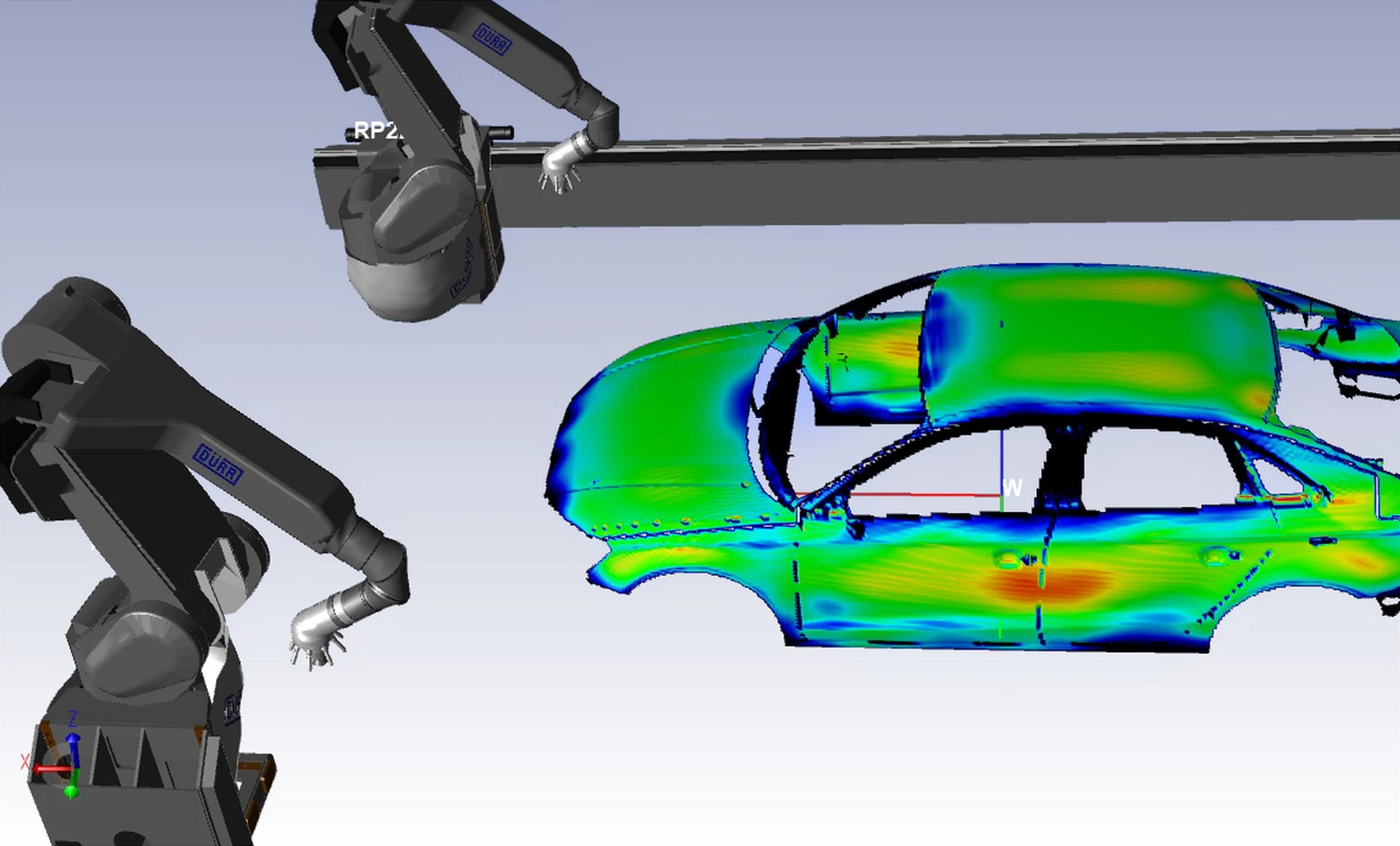
Everything in the green?
The simulation tool belonging to the DXQ3D.onsite software is very easy to use. Just one click of the mouse brings the digital robot station to life, where the car body is painted within a very short time frame. Different colors illustrate the painting result after the robots have finished their work. Problem areas are visible at first glance. In order to achieve a more uniform paint layer, the settings can now be varied. Only when the right parameters for an optimum coating result have been found virtually will the real-life test runs begin.
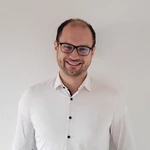
Felix
Losch
Senior Manager
Sales Digital Products
Dürr Systems AG
Carl-Benz-Str. 34
74321 Bietigheim-Bissingen
Germany
Carl-Benz-Str. 34
74321 Bietigheim-Bissingen
Germany