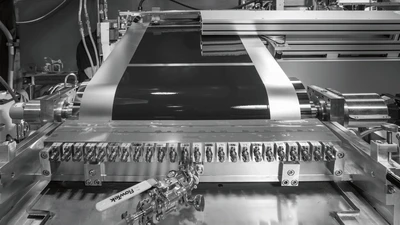
Schichtarbeit
18.03.2021
Die Nachfrage nach Elektroautos wächst – und damit auch die Produktionskapazität für Lithium-Ionen-Akkus. Der Batteriezellfertigung kommt dabei eine Schlüsselrolle zu, sie entscheidet über Kosten und Langlebigkeit des gesamten E-Fahrzeugs. Für die Elektroden in einer Batterie liefert Dürr die Beschichtungstechnik aus einer Hand – und vieles mehr.
460.000 E-Autos wurden 2020 in Europa zugelassen. Zwar entspricht das nur einem Marktanteil von rund 4 Prozent. Doch es ist eine Verdoppelung des Anteils gegenüber dem Vorjahr. Nach wie vor steht die E-Mobilität am Anfang, aber sie wird sich durchsetzen. Die Batteriehersteller müssen die globale Produktionskapazität für Lithium-Ionen-Akkus deutlich ausweiten. Allein in Europa soll sie bis 2025 auf 300 Gigawattstunden pro Jahr wachsen – das entspricht Batterien für rund 6 Millionen Elektroautos. Mehr als die Hälfte der dafür notwendigen Fabriken ist noch nicht einmal geplant – eine gewaltige Chance für den Maschinen- und Anlagenbau.
Schichtarbeit und saubere Luft
Es sind Dutzende Prozessschritte, die benötigt werden, um aus den Rohmaterialien eine sicher funktionierende und langlebige Batterie zu produzieren. Eine Schlüsselrolle kommt dabei der Zellfertigung und besonders der Elektrodenbeschichtung zu. Denn jede einzelne Batteriezelle besteht aus zwei Elektroden, hauchdünnen Aluminium- oder Kupferfolien, die als Parkplätze für die beim Laden und Entladen hin- und heranwandernden Lithium-Ionen dienen. Dafür müssen die Folien mit einer 50 bis 150 Mikrometer dünnen Schicht versehen werden – auf der Anodenseite mit Graphit, auf der Kathodenseite mit einem Gemisch aus Nickel, Mangan, Kobalt und Lithium in einem exakt definierten Mengenverhältnis. Rund 80 Prozent des Materialwerts eines modernen Akkus entfällt auf die Elektroden.
Für den Durchbruch des Elektroautos ist die Zellfertigung von entscheidender Bedeutung. Denn nur wenn es gelingt, vollautomatisiert sehr schnell sehr viele Zellen herzustellen, können die Akkupreise deutlich sinken. Zudem muss die Produktionsqualität extrem hoch sein, damit später nicht ein Teil der teuren Materialien als Abfall entsorgt werden muss – was sich zudem negativ in der Umweltbilanz des Elektroautos niederschlagen würde.
Die Elektrodenproduktion erfolgt unabhängig vom Akkutyp immer in zwei Schritten: Zunächst werden die auf großen Rollen angelieferten Aluminium- oder Kupferfolien beschichtet, anschließend durchlaufen sie einen Trockenofen. Dabei entweicht das im Beschichtungsmaterial enthaltene Lösemittel, was eine aufwendige Abluftreinigung nötig macht. Doch Lösemittel ist teuer – es geht also nicht nur darum, die Abluft zu reinigen. Dank einer ausgeklügelten Rückgewinnung kann ein Großteil des Lösemittels wiederverwendet werden. Das schont die Umwelt und die Kassen der Batterieproduzenten.
ALLES AUS EINER HAND
Im Automotive-Geschäft ist Dürr bekannt für seine Lackierfabriken – Kunden erhalten sie schlüsselfertig, sozusagen all-inclusive. Auch Batteriehersteller können nun bei Dürr die notwendige Technik zur Elektrodenbeschichtung aus einer Hand ordern: von der Beschichtung über die Abluftreinigung bis hin zur Lösemittelrückgewinnung.
Die meisten Anlagen, die derzeit bei Akkuherstellern in Betrieb sind, beschichten zunächst eine Seite der Elektrodenfolie, anschließend die zweite. Ein Pionier dieser Technik ist der Coating-Spezialist Techno Smart, mit dem Dürr seit 2020 kooperiert. Das aus dem japanischen Osaka stammende Unternehmen hat bereits in den 1990er-Jahren Beschichtungstechnologien für Lithium-Ionen-Zellen entwickelt und beliefert namhafte Hersteller. Dürr Megtec, seit 2018 Teil des Dürr-Konzerns, hat ein neues Verfahren entwickelt, das es sogar erlaubt, Elektrodenfolien simultan von beiden Seiten zu beschichten. Dafür muss die Folie den bis zu 50 Meter langen Trockenofen freischwebend ohne den geringsten Kontakt zu Maschinenteilen passieren. Andreas Keil ist bei Dürr Megtec für die Entwicklung des Europageschäfts in der Elektrodenproduktion verantwortlich – und davon überzeugt, dass durch die Simultanbeschichtung nicht nur Kostenvorteile erzielt werden, sondern auch die Qualität steigt. In der Pilotfertigung eines großen europäischen Autoherstellers kommt das Verfahren, das nur Dürr Megtec anbieten kann, derzeit schon zum Einsatz. Es eignet sich auch für kleinformatige Akkuzellen besonders gut, wie sie beispielsweise in Hörgeräten zu finden sind.
Ausgewählte Dürr-Angebote zur E-Mobilität
Cool Down!
In das Kühlsystem von Batterien und Elektronik werden mit Dürr-Technik bis zu 60 Liter Kühlmittel eingefüllt.
Hochtourig
Die Rotoren von Elektromotoren werden in Schleuderständen der Dürr-Tochter Schenck RoTec getestet und an ihre Belastungsgrenze gebracht.
Gut beraten
Mit Dürr Consulting helfen wir Autoherstellern, ihre Batteriemontagewerke zu planen und zu bauen.
Zellen kleben
Die einzelnen Batteriezellen werden nebeneinander angeordnet und – vereinfacht gesagt – zu einem Batteriemodul verklebt. Zwischen dem Batteriemodul und der Kühlplatte trägt unsere Applikationstechnik eine Wärmeleitpaste auf.
Unter Spannung
Dürr-Prüftechnik stellt sicher, dass von den Hochvoltkreisen in E-Fahrzeugen keine Gefahr ausgeht.
Volle Ladung Batterietechnik
Dürr-Technologien kommen auch an vielen anderen Stellen der Zell- und Batteriesystemproduktion zum Einsatz. Zum Beispiel bei der Beschichtung der Zellen mit dem →EcoPaintJet, einem besonders präzisen Lackierrobotersystem ohne Overspray. Dieser Schritt dient zum einen der elektrischen Isolation der Batteriezellen, zum anderen der thermischen Isolation. Fürs Verkleben der Batteriezellen zu Modulen und für den Auftrag einer Wärmeleitpaste zwischen Batteriemodul und Kühlplatte hat Dürr ebenfalls die passende Technik. Befüllung der Batteriekühlsysteme mit Kühlmittel? Auch hier kann Dürr helfen, ebenso bei der Planung von Batteriemontageanlagen. Die Liste lässt sich fortsetzen – und wird noch länger: Durch die Übernahme der Mehrheit von Teamtechnik im Februar 2021 gehören auch Technologien für die Montage und Prüfung von Batteriemodulen zum Angebot.
Anwendungsbeispiele für Lithium-Ionen-Akkus
Elektroautos sind der große Wachstumstreiber im weltweiten Markt für Lithium-Ionen-Akkus. Doch auch bei vielen anderen Geräten kommen sie zum Einsatz. Die Nutzer von schnurlosen Kopfhörern, E-Bikes und Stromspeichern wissen die hohe Energiedichte der Lithium-Ionen-Technik und das geringe Gewicht der Batterien zu schätzen. Auch diese Zellen werden mit Dürr-Technik hergestellt.
Unerhört gut
Vom Hörrohr zum winzigen Hightech-Lautsprecher: Der Fortschritt bei Hörgeräten ist enorm. Bislang funktionieren sie meist noch mit Einwegbatterien. Dank Lithium-Ionen-Technologie und Ladeschalen revolutionieren nun Akkus den Markt.
Wirbelwind
Sie machen Schluss mit Kabelsalat und dem mühsamen Heben des Staubsaugers von Stufe zu Stufe: Kabellose Modelle krempeln die Branche um. Durch leistungsstarke Lithium-Ionen-Technologie halten manche Geräte im Betrieb über eine Stunde aus – und sind trotzdem leicht.
Das Rad neu erfinden
Langlebige Lithium-Ionen-Akkus sorgen für ausreichend Energie und halten gleichzeitig das Gewicht gering. Ein Grund dafür, weshalb der Trend zum E-Bike ungebremst ist.
Auf die Ohren
Gerade während der Lockdowns waren sie bei Videokonferenzen im Einsatz: kleine kabellose Kopfhörer, die Gespräche und Musik wiedergeben – und die Umgebung ausblenden. Geladen werden ihre Lithium-Ionen-Akkus zum Beispiel in kleinen Boxen.
Weil nachts keine Sonne scheint
Mit Photovoltaikanlagen auf dem Dach wandeln immer mehr Hausbesitzer Sonnenenergie in kostenlosen Strom um. Ein Trend, der mit der Verbreitung des E-Autos weiteren Schub bekommen dürfte. Doch nachts scheint keine Sonne – und gerade dann hängt das E-Auto an der Steckdose, laufen Waschmaschine, Trockner und Co. Energiespeicher sind die Lösung. Sie nehmen tagsüber die Sonnenenergie auf und geben sie nachts wieder ab. Auch dies ein Fall für Lithium-Ionen-Akkus: Dank ihrer hohen Energiedichte sind sie klein und passen daher in viele Keller.
![[Translate to Deutsch:] duerr-andreas-keil Andreas Keil Director Business Development](/fileadmin/_processed_/8/c/csm_duerr-andreas-keil_01_c391b67ff5.webp)
Andreas
Keil
Director Business Development
Dürr Megtec
Carl-Benz-Str. 34
74321 Bietigheim-Bissingen
Deutschland
Carl-Benz-Str. 34
74321 Bietigheim-Bissingen
Deutschland