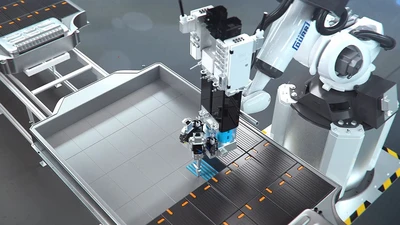
Ein Projekt mit großer Strahlkraft
26.03.2020
Dürr Consulting berät europäischen Automobilhersteller bei der Batteriemontage
Die E-Mobilität ist eine große Herausforderung für die Automobilindustrie. Dürr hilft seinen Kunden beim Umstieg auf die Batterietechnik wirksam, wie folgendes Projektbeispiel zeigt: Ein Automobilhersteller hat eine der ersten europäischen Batteriemontagen gebaut. Dürr Consulting hat bei diesem Leuchtturmprojekt über drei Jahre hinweg maßgeblich unterstützt.
Nahezu jeder Automobilhersteller entwickelt Elektrofahrzeuge und bietet erste Modelle an. Studien zufolge wird die Nachfrage nach Elektrofahrzeugen bis 2025 enorm steigen. Dies führt dazu, dass in den nächsten Jahrzehnten Milliarden von Euro in die Batteriefertigung investiert werden.
Die Batteriemontage ist ein neues, stark wachsendes Geschäft. Hier wollen außer Automobilherstellern und Mobilitäts-Start-Ups auch Zulieferer aktiv werden, um neben dem konventionellen Antriebsstrang weitere Geschäftsfelder zu erschließen. „Der Auftrag des europäischen Automobilherstellers war für uns eine große Chance. Wir haben hier die Basis für langfristiges Kompetenzwachstum geschaffen“, beschreibt Andreas Hohmann, Leiter der → Dürr Consulting, die Bedeutung dieses Projekts.
Mit dem Auftrag haben wir die Basis für langfristiges Kompetenzwachstum geschaffen.
Andreas Hohmann , Leiter Dürr Consulting
Zu Beginn im Jahr 2016 existierten nur rudimentäre Ideen und Konzepte. Ein zunächst achtköpfiges Consulting-Team arbeitete sich daher in das neue Thema Batteriemontage ein. Mit diesem Wissen und der langjährigen Expertise bei Neu- und Umbauten half man dem Automobilproduzenten.
Die Kernelemente:
- Entwicklung des Batteriemontageprozesses
- Produktionskonzeptplanung
- Festlegung des Automatisierungsgrads
- Erarbeitung eines Hochspannungssicherheitskonzepts
- Entwicklung von Automatisierungslösungen
Während der Arbeit an diesen Schritten wurde parallel auch das Design der Batteriemodule erarbeitet. Der Fokus von Dürr Consulting lag auf der Entwicklung manueller und vor allem automatisierter Prozesse sowie technischer Spezifikationen, um das Ziel von 20 Batterien pro Stunde zu erreichen.
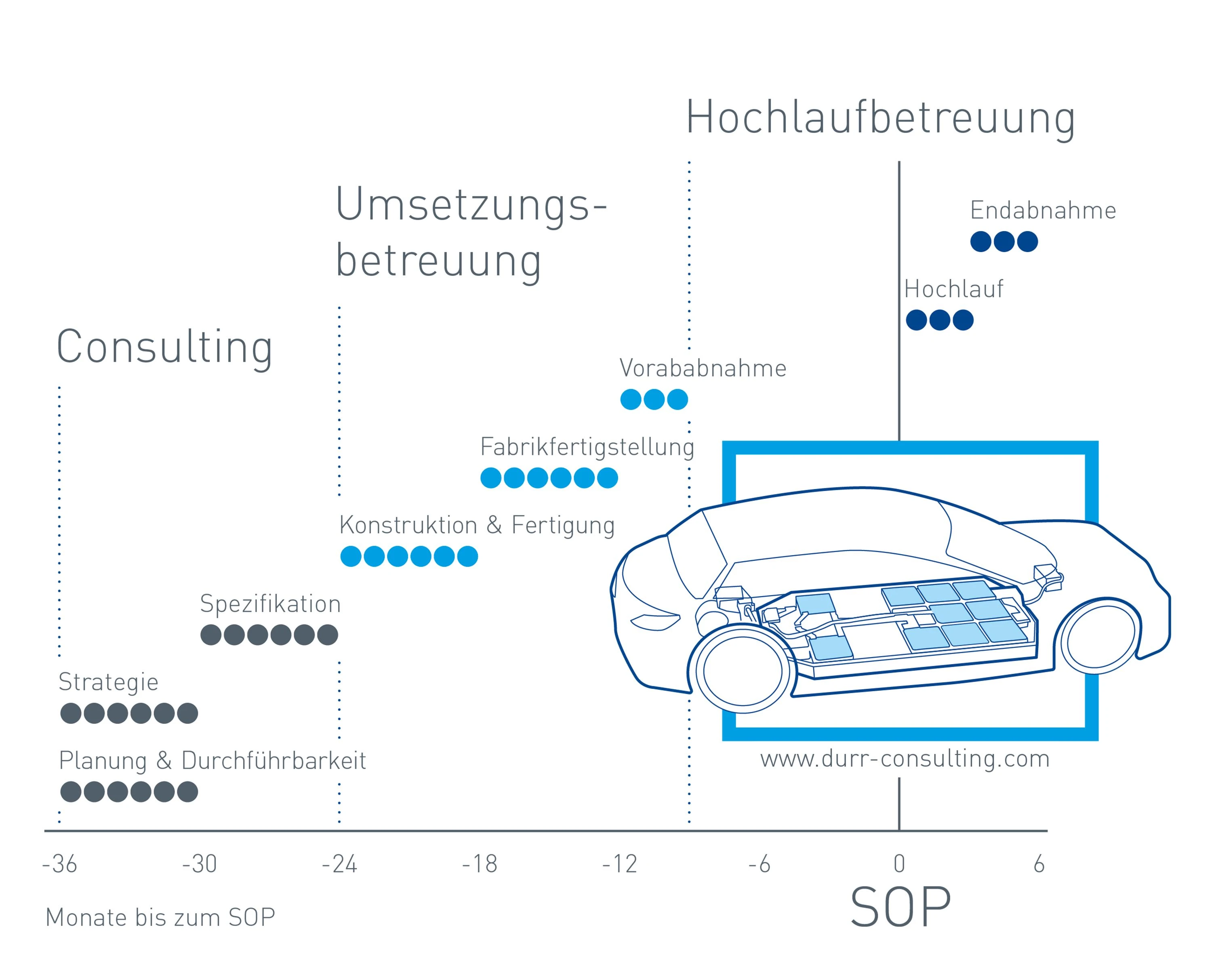
Das umgesetzte Konzept besteht aus fünf Montagelinien mit insgesamt 60 Takten. In Linie 1 tragen Roboter unter anderem den Gapfiller in den Batteriegehäusen auf. Diese Wärmeleitpaste überträgt die Wärme der Zellmodule zur Kühlung und gleicht Unebenheiten aus. Danach werden die Zellmodule eingesetzt und verschraubt. In Linie 2 werden die Hochvolt-Verbinder gesetzt, die alle Module verbinden und so eine Gesamtspannung von circa 400 Volt aufbauen.
Darüber hinaus werden in Linie 2 und 3 weitere Anbauteile und Leitungen teils manuell ergänzt; weitere automatische Schritte sind die Applikation des Abdichtmaterials auf die Wannen und Deckel der Batterie sowie das Aufsetzen und Verschrauben der Deckel. In Linie 4 führen Mitarbeiter des Automobilherstellers Dichtheitsprüfungen an der Kühlung und der gesamten Batterie durch. Am Bandende (Linie 5) wird die Batterie in mehreren automatisierten Prüfstationen getestet und geladen.
Neben den Produktions- und Sicherheitskonzepten kümmerte sich das Dürr-Team um technische Details, bewertete die Lieferantenbasis, zeigte geeignete Lieferanten auf und leitete die Hochlaufphase der Anlagen. Seit dem Produktionsstart Ende 2018 unterstützt es den Kunden dabei, die Produktion auf 20 Einheiten pro Stunde zu steigern und neue Batterietypen in den Produktionsprozess zu integrieren.
Dürr Consulting hat bei dem Batteriemontageprojekt weitreichende Kompetenzen entwickelt. So ist man in der Lage, andere Kunden im Batteriemontagegeschäft zu beraten, sei es bei der Produktionsstrategie, mit Marktanalysen oder bei der Frage, wie das Produktdesign mit Blick auf eine effiziente Fertigung aussehen sollte.
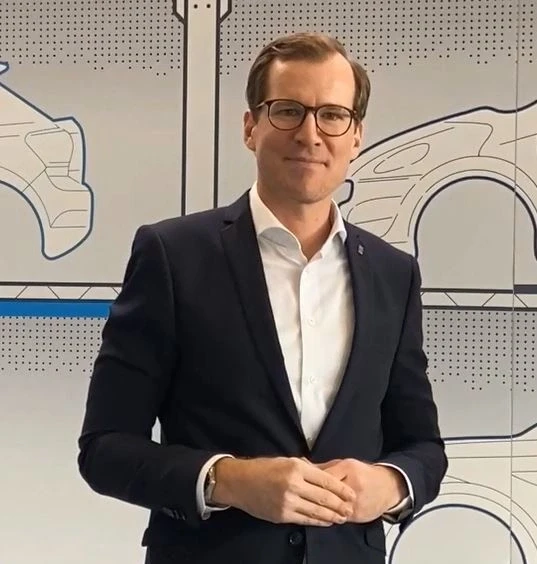
Sind Li-Ionen-Akkus die Zukunft?
Die Mitarbeiter der Dürr Consulting blicken mehrere Jahrzehnte in die Zukunft. Besonders beschäftigt sie die Frage, ob die heutigen Lithium-Ionen-Batterie langfristig der Energieversorger für Autos bleiben werden. „Wir sagen Nein", lautet die Antwort von Andreas Hohmann, Leiter der Dürr Consulting. Denn die Lithium-Ionen-Batterien haben Nachteile: Bei einem Elektroauto mit 20-jährigem Lebenszyklus sind die Gesamtkosten nach heutigen Berechnungen 46 % höher als bei einem Fahrzeug mit Verbrennungsmotor. Denn die Batterieherstellung ist enorm aufwändig, zudem müssen die Batterien während der Lebensdauer des Autos mehrmals gewechselt werden.
Im Vergleich dazu sieht Andreas Hohmann zwei andere Energiespeicher im Vorteil: zum einen die Feststoffbatterie, die in den nächsten fünf bis zehn Jahren marktreif sein wird, und zum anderen die Brennstoffzelle für schwere und mittelgroße Fahrzeuge. Sie ist bei hohen Reichweiten klimafreundlicher als die Batterie.
Aus Sicht der Autohersteller sind Elektrofahrzeuge derzeit sinnvoll, um Strafzahlungen zu vermeiden, die aufgrund verschärfter CO2-Emissionsvorgaben drohen. „Wir glauben allerdings, dass die herkömmlichen Lithium-Ionen-Batterien nur eine Übergangstechnologie auf dem Weg in eine grüne und nachhaltige Automobilzukunft sein werden“, prognostiziert Andreas Hohmann. Trotzdem wird die Dürr Consulting Kunden auf dem derzeitigen Weg zu einer effizienten und automatisierten Batteriemontage unterstützen – die Kompetenz dafür ist vorhanden.