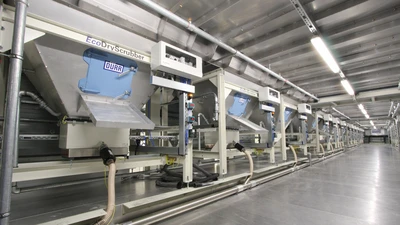
10 years of dry separation
Mar 23, 2020
From fully automatic to manual: Dürr offers tailored solutions
Energy-efficient, reliable, and environmentally friendly: Dürr revolutionized the process of paint overspray binding in paint booths in the automotive industry in 2010 with the EcoDryScrubber dry separation system. Right from the beginning, the new technology convinced OEMs with high cost and resource savings compared with conventional wet scrubbing. As a pioneer in dry separation, Dürr used its advanced knowledge to develop a product series that enables differentiated technical solutions.
Overspray is an inevitable part of automotive finishing since some of the atomized paint does not make it to the bodies and instead hovers in the paint booth as overspray. Process air with a constant sinking speed carries the paint mist from the application area into the paint separation. The traditional method of removing superfluous paint particles from the air uses a lot of water and chemicals. This has an environmental impact and is costly, not least because the wet paint sludge has to undergo an expensive disposal process as hazardous waste. Moreover, the entrained water can contaminate the booth and lead to corrosion.
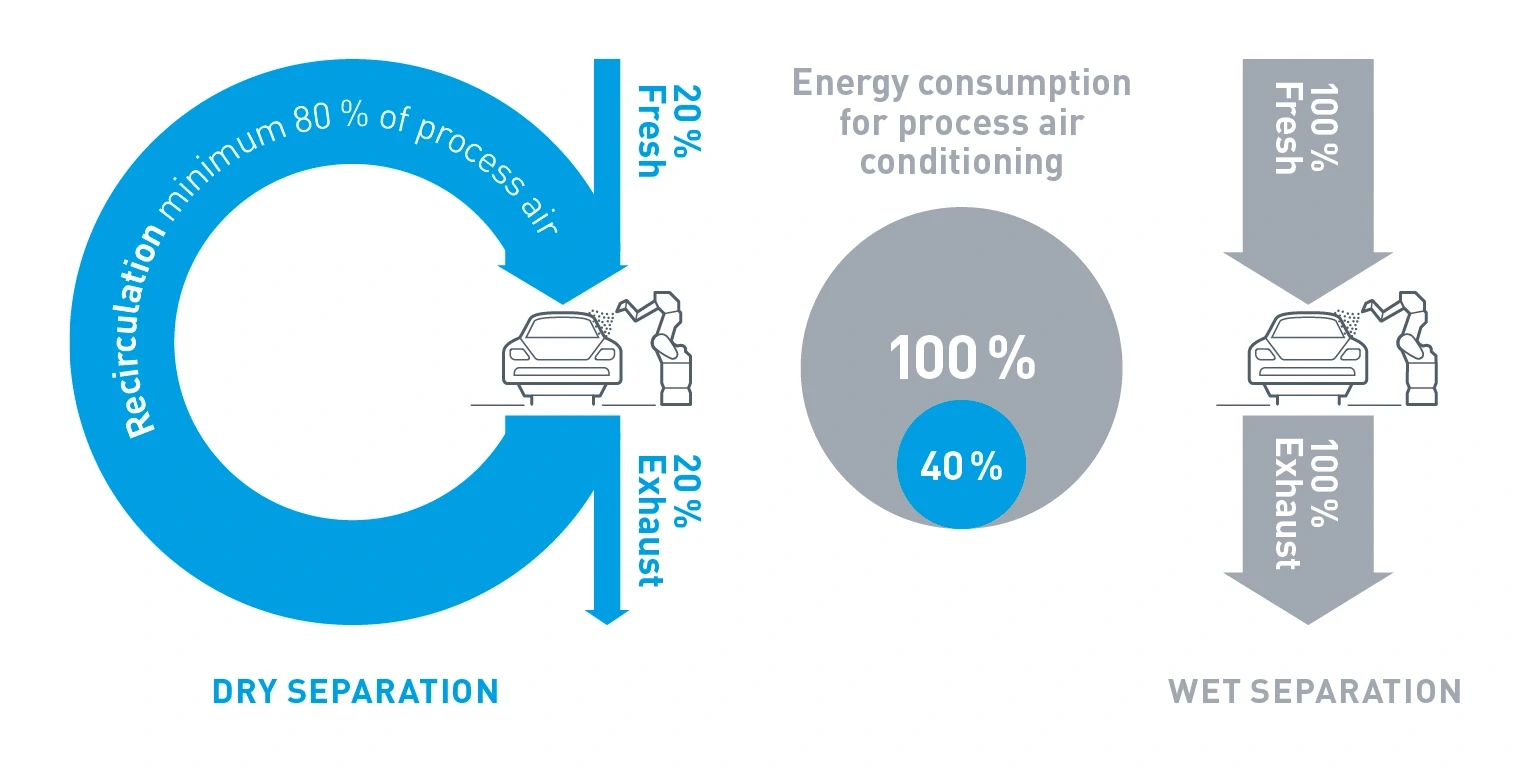
15 years ago, Dürr set itself the goal of developing an alternative for the wet scrubbing method with its many disadvantages. The standard it imposed for this was high: It had to be an environmentally friendly system with low energy consumption, without the use of water and chemicals.
The solution was → EcoDryScrubber, a fully automatic dry separation system that uses limestone powder as a dry binder. This made it possible for the first time in a paint booth with paint separation to conduct the process air in an energy-efficient way in a recirculated air mode. Compared with conventional wet separation with pure fresh/exhaust air operation, this saves about half the energy consumption of the entire paint shop. Since the first EcoDryScrubber was sold for BMW in Regensburg in 2010, more than 80 paint lines of all well-known OEMs on four continents have been equipped with the benchmark technology.
On the basis of this high-tech solution, Dürr developed two further filter systems, → EcoDry X and EcoDry Rack. Both of them use disposable cardboard filters. Together with EcoDryScrubber they form the Dürr dry separation family for different customer needs and budgets.
The product portfolio mirrors Dürr’s experience that efficient painting processes are individual and pose different demands. The determining factor is not only a paint shop’s throughput. The amount and type of overspray is critical in choosing the right dry separation system, because the systems differ in their absorption capacity, filter medium, and handling. Wet or dry? – dry separation has a clear edge since it combines environmental, quality, and cost aspects in one concept in the best possible way.
Maximum energy efficiency
Whether limestone powder or filter boxes, the dry binder is the key to extreme energy efficiency, since it enables the paint booth to be operated with up to 95 % recirculated air. This means that only a small percentage of fresh air needs to be conditioned. The picture is very different with wet separation, which adds moisture to the process air. With dry separation, on the other hand, there is no change in the humidity and temperature in the paint booth. The following figures demonstrate just how environmentally friendly and cost-effective this is:
- water consumption for fresh air conditioning is 80% lower compared to conventional wet separation;
- 80 to 95% air recirculation reduces the total energy consumption of a paint shop by around 30%;
- up to 80% less heat and 50% less power are required in the paint booth.
The fully automatic system of the EcoDryScrubber separates the overspray using natural limestone powder. The saturated limestone powder can be processed directly as a secondary raw material in the cement industry or used for flue gas desulfurization in power plants. This makes the system especially sustainable.
EcoDry X uses easily exchanged disposable cardboard filters, which can even be changed during production if necessary. The semi-automatic filter system offers all the benefits of dry separation, achieves the best results with minimum effort, and is easy to use.
Like its sister product EcoDry X, EcoDry Rack also relies on disposable cardboard filters while EcoDry Rack is particularly suitable for smaller production facilities with limited space. The filter boxes in EcoDry Rack are housed in permanently installed filter walls and are exchanged directly in the booth.
Dürr's dry separation systems have been proven over the last ten years in about 130 automotive paint lines worldwide. Find out more about Dürr’s dry separation products in the next parts of our series.