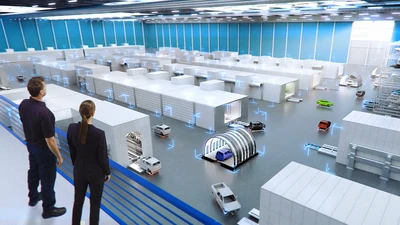
Painting cars in the paint shop of the future
Dec 18, 2019
Innovative, flexible and scalable
New requirements in car painting call for new concepts. Dürr’s paint shop of the future is an innovative layout with specially developed products. In contrast to the traditional production line, this modular concept enables greater flexibility and efficiency in manufacturing. Whether large volume manufacturers or small e-car start-ups: thanks to the new concept, automobile manufacturers can react more quickly to customer and market requirements, such as the growing variety of models, the mix of conventional and battery-powered cars, and greater individualization.
The new concept is based on the interplay of fresh approaches and product developments.The → paint shop of the future is based on a completely new approach to the layout: The 120 or so work steps of a painting process will no longer be divided into lines but into boxes and smaller sections. The advantage: Not all bodies have to follow a fixed sequence in a fixed cycle but can, depending on the model, be processed with individual process times in boxes arranged in parallel. This revolutionary layout, which is based on the paint box, will become a reality through intelligent control and specially developed products.
Individual conveying, instead of following rigid lines
→ EcoProFleet is the first driverless transport system (Automated Guided Vehicle, AGV) to be used in the paint shop. The system, which has been ensuring flexibility in final assembly for a long time already, will now be used as a transport system between the individual boxes and process sections.
Individual programming and sequencing
Controlling this fleet of AGVs is made possible by the → DXQcontrol software. It enables each individual AGV to be intelligently guided to the next process with the body located on it, which ensures efficient utilization of all the boxes. In interaction with the centrally placed high-bay storage area with individually controllable single bays, this creates a level of flexibility unheard of in the previously used single-level areas with permanently installed floor conveyor system. The big advantage: The bodies are intelligently sorted, delivered to and collected from the correct work zone, and can be handed over to final assembly at the end in the sequence planned by the manufacturer.
Shorter process times through 3-in-1 painting
The concept is also made possible by the merging of three painting tasks – one internal and two external applications – in a single booth. The product used for this is the patent-pending spray booth EcoProBooth. This change saves process time, as two of the three conveying procedures previously used can be omitted. The paint-loss during the color change process can even be reduced: If only one color is applied in the EcoProBooth, paint consumption can even be reduced by up to ten percent. This also reduces VOC emissions. A special color paint supply system or special processes, such as overspray-free two-tone painting, can also be easily and cost-effectively integrated into the variable layout.
With the “Paint shop of the future”, Dürr is reimagining the painting process and moving beyond the boundaries of the production line.
Bruno Welsch , Member of the Board of Management of Dürr Systems AG
Increased plant availability
The plant availability also increases, because malfunctions only affect the box section concerned and – unlike before – do not affect the entire production line. The intelligent control unit can react directly to this: The bodies are assigned to another box or sent to the high-bay storage area for temporary storage.
Scalable: Adaptable for large and small production runs
The modular paint box will enable production capacities to be easily extended or new models to be integrated without any problems. The concept can be applied to both the overall top coat and work zone area and to selected process steps. This permits production to be adapted to all requirements, whether for large volume manufacturers or newcomers looking to be able to expand their units in stages.
Benefits for you
- Needs-based process times instead of fixed cycle times
- Simple integration of new vehicle models
- Simple integration of new and special processes
- Capacities more easily scalable compared to the line concept
- Allocation of individual boxes for special tasks possible, e.g. teaching the application technology for new body models, while production in other boxes continues.
- Greater availability: Production can continue even when individual boxes are unserviceable