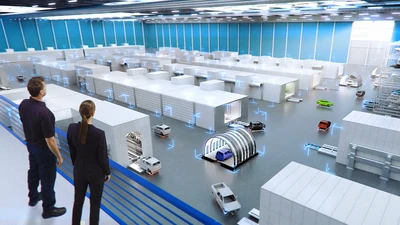
Autos lackieren in der Lackieranlage der Zukunft
18.12.2019
Innovativ, flexibel und skalierbar
Neue Anforderungen in der Automobillackierung erfordern neue Konzepte. Dürr stellt mit der Lackieranlage der Zukunft ein innovatives Layout mit speziell entwickelten Produkten vor. Im Gegensatz zur traditionellen Linienfertigung ermöglicht dieses modular aufgebaute Konzept mehr Flexibilität und Effizienz in der Fertigung. Egal, ob großer Volumenhersteller oder kleines E-Car-Startup: Automobilhersteller können dank des neuen Konzepts schneller auf Kunden- und Marktanforderungen, wie die wachsende Modellvielfalt, den Mix aus herkömmlichen und batteriebetriebenen Autos sowie eine höhere Individualisierung reagieren.
Das neue Konzept basiert auf dem Zusammenwirken frischer Denkansätze und Produktentwicklungen. Der → Lackieranlage der Zukunft liegt ein völlig neuer Layout-Ansatz zugrunde: Die rund 120 Arbeitsschritte eines Lackierprozesses werden nicht mehr in Linien, sondern in Boxen und kleinere Abschnitte aufgeteilt. Der Vorteil: Nicht jede Karosserie muss einem festgelegten Verlauf in einem festen Takt folgen, sondern kann je nach Modell mit individuellen Prozesszeiten in parallel angeordneten Boxen bearbeitet werden. Dieses revolutionäre Layout wird durch intelligente Steuerung und eigens entwickelte Produkte Realität.
Individuell fördern statt starren Linien folgen
→ EcoProFleet ist das erste fahrerlose Transportsystem (Automated Guided Vehicle, AGV), das in der Lackieranlage eingesetzt wird. Das System, das in der Endmontage bereits seit Langem für Flexibilisierung sorgt, wird nun als Transportsystem zwischen den einzelnen Boxen und Prozessabschnitten eingesetzt.
Individuell programmieren und sequenzieren
Gesteuert wird diese Flotte durch die Software → DXQcontrol. Sie erlaubt es, jedes einzelne AGV intelligent mit der darauf befindlichen Karosserie zum jeweils nächsten Prozess zu steuern, und sichert dadurch eine effiziente Auslastung aller Boxen. Im Zusammenspiel mit dem zentralen Hochregallager mit individuell ansteuerbaren Einzelplätzen entsteht so eine Flexibilität, die in den bisher verwendeten Flächenlagern mit fest installierter Bodenfördertechnik undenkbar war. Der große Vorteil: Die Karosserien werden intelligent sortiert, punktgenau zum richtigen Arbeitsplatz gebracht und abgeholt und können am Ende in der vom Hersteller geplanten Sequenz an die Endmontage übergeben werden.
Kürzere Prozesszeiten durch Drei-in-Eins-Lackierung
Das Konzept wird auch durch die Zusammenlegung von drei Lackiervorgängen – dem Innen- und der beiden Außenaufträge – in einer einzigen Kabine möglich. Das von Dürr zum Patent angemeldete Konzept, die EcoProBooth, spart Prozesszeit ein, da zwei der bisher üblichen drei Fördervorgänge entfallen. Gleichzeitig verringert sich der Verlust beim Farbwechsel: Wird in der EcoProBooth ausschließlich eine Farbe appliziert, kann der Lackverbrauch sogar um bis zu zehn Prozent verringert werden. So reduzieren sich auch die VOC-Emissionen. In das variable Layout lassen sich zudem eine Sonderfarbversorgung oder Sonderprozesse, wie die oversprayfreie Zweiton-Lackierung, leichter und kosteneffizienter integrieren.
Mit der ‚Lackieranlage der Zukunft‘ denkt Dürr den Lackierprozess neu und überwindet die Grenzen der starren Produktionslinie.
Bruno Welsch , Vorstandsmitglied der Dürr Systems AG
Erhöhte Gesamtanlagen-Verfügbarkeit
Auch die Gesamtanlagen-Verfügbarkeit steigt, denn eine Störung wirkt sich nur in dem betroffenen Boxenabschnitt aus und beeinträchtigt – anders als bisher – nicht die komplette Produktionslinie. Die intelligente Steuerung kann hierauf direkt reagieren: Die Karosserien werden einer anderen Box zugewiesen oder im Hochregallager zwischengelagert.
Skalierbar: Für grosse wie kleine Produktionen adaptierbar
Das modulare Boxenkonzept erlaubt es, Produktionskapazitäten einfach zu erweitern oder neue Modelle problemlos zu integrieren. Anwendbar ist das Konzept sowohl auf den gesamten Decklack- und Arbeitsplatzbereich als auch auf ausgewählte Prozessschritte. Damit ist es geeignet für große Volumenhersteller und für Newcomer mit dem Wunsch, ihre Stückzahlen je nach Nachfrage schrittweise auszubauen.
Ihre Vorteile
- Bedarfsorientierte Prozesszeiten statt fester Taktzeiten
- Einfache Integration neuer Fahrzeugmodelle
- Einfache Integration neuer und spezieller Prozesse
- Kapazitäten einfacher skalierbar im Vergleich zum Linienkonzept
- Zuweisung einzelner Boxen für besondere Aufgaben möglich, z. B. Teachen der Applikationstechnik für neue Karosseriemodelle, während die Produktion in anderen Boxen fortgesetzt wird
- Höhere Verfügbarkeit: Produktion wird auch bei Stillstand einzelner Boxen fortgesetzt