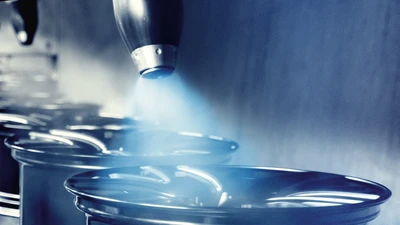
Innovations in wheel painting
Oct 28, 2019
Dürr ranks among the world’s leading plant manufacturers in the field of paint finishing on cars, vans, trucks and buses. But that’s not all: Its expertise additionally extends to painting rail vehicles, plastic parts and wheels, as well as other non-automotive components. Particularly when it comes to wheel painting, Dürr has completed a number of challenging projects in recent years. Highly diverse models and many new wheel sizes are increasing the demand for high-quality painting on a growing global market.
High-quality wheels featuring special effects have exploded in popularity in recent years. Diamond-cut wheels in particular are all the rage, one reason being that alloy wheels weigh less than their conventional steel counterparts and therefore improve fuel economy. Applying the diamond-cutting process to aluminum wheels furthermore opens up a whole new range of design options in terms of shape and color.
How to paint diamond-cut wheels
Wheels are initially cleaned in a pretreatment process, generally in a dip tank, and subsequently painted and dried. To apply the finishing touch, the aluminum wheels are then machined with a diamond cutter to remove some paint and a few hundredths of a millimeter of aluminum to reveal the shiny metal surface underneath. This diamond-cutting process is used mainly on the outwardly or inwardly curved or thickened wheel bead and the spokes, producing fascinating visual effects. For the final step, another clear coat layer is applied to protect and enhance the machined surface.
Standardized, yet customizable
Designing an efficient painting process that simultaneously takes customers’ requirements into account is another of Dürr’s strengths. Dürr has been implementing a wide range of projects in Europe and America, and increasingly in Asia as well.
Customized, process-optimized layouts permit high production volumes in automated manufacturing. For example, it can be expedient to relocate the diamond-cutting and subsequent clear-coating processes to a separate line section. Focusing on the customer is always the key consideration when planning and implementing solutions. Whether the customer requires powder coating, automatic wet paint application systems with paint mix rooms or the use of painting robots with →EcoBell2 SL direct-charging, high-speed rotating atomizers, plants from Dürr always ensure a high-quality paint finish. These systems guarantee efficient processes when combined with automatic color changers such as the →EcoMCC3, special color paint supply systems like the →EcoSupply P, gearwheel pumps, as well as paint-flow and back-pressure controllers for paint metering and supply.
The trend for new plants is toward robots with high-precision application technology. Painting angles and spray patterns can be changed rapidly, which is a key advantage. Dürr’s ready2spray robot is the right choice for this segment.
Robin Kaufmann , Senior Manager, Dürr Systems AG
Another factor contributing to efficiency is the smooth transfer of wheels from synchronized conveyors to downstream processes by handling systems with very light grippers. Patented, self-adjusting spindles and a brushless system for removing powder from the wheel hubs and mounting surfaces were developed to accommodate the special process requirements. Wheel manufacturers have so far been relying mostly on compact, wet scrubber solutions to remove paint overspray in spray booths. Dry paint overspray separation systems are gaining in importance, however, because they dispense with water and chemicals while consuming significantly less energy.
There is now great interest in dry paint overspray separation systems as well, because they have already proven their worth in automotive paint finishing.
Dirk Gorges , Senior Vice President Sales, Dürr Systems AG
More sustainable drying process
Customers are increasingly considering sustainability aspects as well. Ovens now account for most of the energy consumed in the painting process. It is therefore essential to use the heat exactly where it is needed for each specific wheel type. A standard painting line for aluminum wheels includes three ovens for drying after pretreatment and the various coating processes. Additional ovens may be required if the customer uses anticorrosion, polyester and acrylic-power clear coats. Another complication is that aluminum wheels vary greatly in material thickness and size. The major challenge during drying is therefore to direct the hot air to the right places. Whereas thick areas like the wheel hubs must be sufficiently dried, thinner parts must not be overheated to the point where their mechanical properties would suffer. Furthermore, it must be possible to dry 14- to 24-inch wheels in the same ovens.
Special attention must also be paid to the exhaust air. Regenerative thermal air pollution control systems can minimize volatile organic compound (VOC) emissions. For example, Dürr’s →Ecopure® RTO minimizes the condensation of high-boiling-point solvents in the oven’s exhaust air, which is typical of the wet paints used for finishing aluminum wheels.
Wheel Painting Conference 2019
Dürr was holding its Wheel Painting Conference on October 22 and 23 in Bietigheim-Bissingen. The Conference served as a platform for visitors to discuss current trends and challenges such as digitalization and customization. Experts were on hand to provide insights into important aspects of wheel painting. Dürr provided live demonstrations to showcase its latest developments and solutions for applications such as →overspray-free painting as well as cleaning and separation processes.