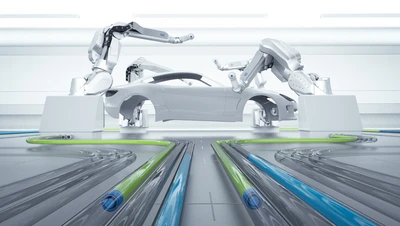
Customized items produced in series
It should really be something special – more and more people are guided by this principle when making a purchasing decision.
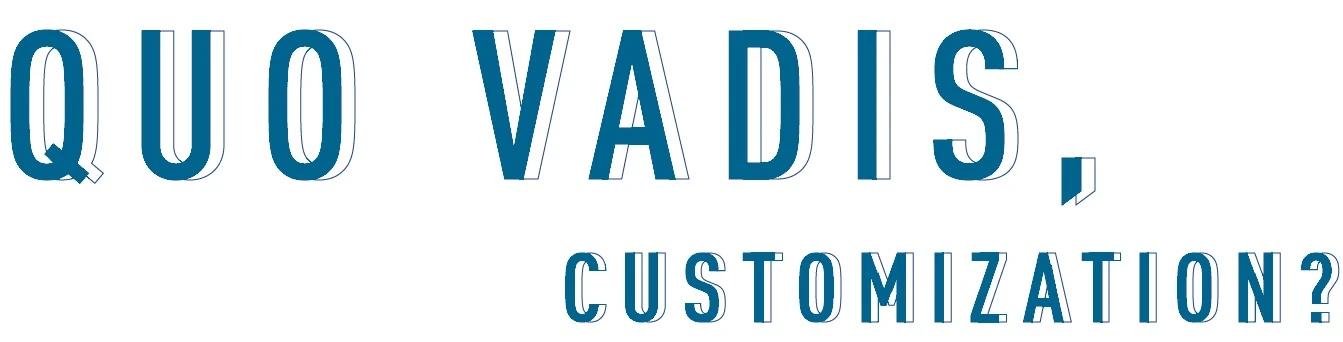
Globalization, digitization and increased prosperity have multiplied the options for self-fulfillment – while also fanning the desire for it. Customization is a trend that is not only impacting society, but also offering opportunities for business. Prof. Dr. Frank T. Piller is one of the leading experts on strategies for customer-centric value creation, such as mass customization and personalization. We discussed this trend with him.
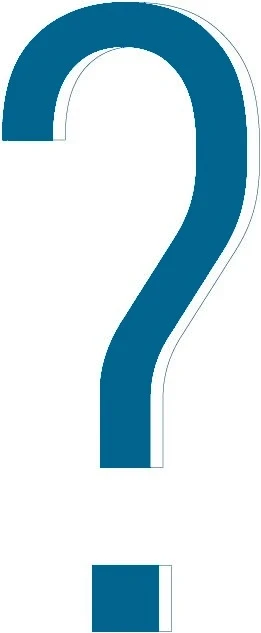
PROFESSOR PILLER, WHY IS CUSTOMIZATION GAINING EVER GREATER TRACTION NOWADAYS?
There are two significant societal developments in this regard. First, the growing diversity in terms of ages, cultures and lifestyles. This is also reflected in greater product variety. Second, generations Y and Z are now becoming consumers. In their personal media consumption, customization is all they know. TV and LPs are an alien world to them. They are used to video-on-demand, streaming and self-curated newsfeeds. Ultimately, that also carries over into their personal consumption. Overall, however, the retail sector remains the main driver for customization of consumer goods. Because products or packaging customized for a retail chain ensure an exclusive range. And exclusive ranges are not subject to the usual price competition.
SO, DOES EVERY COMPANY NEED TO ENSURE THAT ITS PRODUCTS ARE CUSTOMIZABLE?
No, and what is also important is that customization does not mean that a product is manufactured on demand as a one-off. Customers want what they want – how the manufacturer satisfies that is not their concern. And if a mass-produced product satisfies this need, that’s fine. Hence the very successful match-to-order applications in the sports shoe sector, for instance, in which an existing product is offered to a customer to match their requirement. There are enough sports shoes on the market. I just don’t know which of them best meet my needs. Mass customization occurs here in the sales process.
Brief resume
Prof. Dr. Frank T. Piller heads the Institute for Technology and Innovation Management at RWTH Aachen University in Germany. He is also the director of studies on the joint Executive MBA of RWTH Aachen University and Fraunhofer Gesellschaft. He is the co-founder of the Smart Customization Group at Massachusetts Institute of Technology (MIT) in the United States, where he worked at the MIT Sloan School of Management from the end of 2004 until early 2007.
HOW CAN MECHANICAL PLANT ENGINEERING COMPANIES BENEFIT FROM CUSTOMIZATION?
By creating benefit for their customers! Customization is not an end in itself. It has to come into play where the machine purchaser is willing to pay for the customization – such as for a machine capable itself of manufacturing customized products. But I know enough machinery manufacturers who proudly demonstrate the many options for the customized production of goods using their plant, only to be surprised later on that the potential machine purchasers have no idea what they are supposed to do with all the customization options. That’s because there is no appropriate business model in place yet. I also see great potential in the customization of accompanying services. Service business, if well managed, is always mass customization.
WHAT DIRECTION DO YOU THINK WE ARE HEADING IN? BY 2050, WILL WE ONLY BE ORDERING CLOTHES AND CARS THAT ARE FULLY TAILORED TO OUR SPECIFICATIONS?
An exciting question – without a one-size-fits-all answer. In the future, we will be more likely to share cars than to own them. Customization will then be all the more important during the usage phase. Not via hardware components, but via smart products. By that we mean that users will customize commoditized products to their own tastes and wishes via software adaptations or personalized services. Networked cars offer plentiful options in that regard. For instance, they automatically adjust the interior lighting to my preferences. At the same time, however, in those markets where people still own the car, the desire for customization of the “hardware” will continue to grow. In the case of clothing, we can already see that production is relocating from low-wage countries to the sales markets themselves, thanks to automated production technology. In this case again, though, I don’t see the end customer as the main user of customization but rather the retailers or business-to-business-to-consumer business models: Every retailer can now order a customized collection for the coming week, but also, for instance, an influencer on Instagram can create her own extremely short-run fashion collection and sell it to her followers. This type of customization offers huge potential!
Whether fitted kitchen or car – customized items can be produced in series thanks to manufacturing technology by the Dürr Group.
Autonomous carpentry workshop
A wider drawer, a higher table, a narrower cupboard – customers are requesting more tailor-made furniture. The woodworking industry has long been prepared for this and uses HOMAG Group technology to produce customized items fully automatically and with an efficiency similar to that of series production. What has so far been the reserve of large companies is now also a viable option for small carpentry workshops. The Dürr subsidiary from the Black Forest in Germany has developed the ‘autonomous cell’, a workshop that operates fully automatically. Tailor-made wood panels are initially given a machine-readable bar code, containing all machining information. In a subsequent step, a machine applies glue to the cut edges of the wood. Now comes the centerpiece: a CNC machine, which drills holes and fits dowels with maximum precision. The workpieces are transported by a small autonomous guided vehicle. The movable robot travels between the stations, collects panels and deposits them at the next machine or in a temporary storage facility. This is controlled by software which interconnects all components in the workshop.
Clear contours for multiple colors
To stand out from the crowd, buyers of new cars often order a contrasting color for the car roof. Or they ask for a decorative stripe to give the car a nice, sleek look. Making owners happy means a lot of effort for manufacturers. After the first coating, factory workers must cover the car body with masking film and, as if applying a template, expose just those areas which will be sprayed in a different color. After the second coating, the masking film is removed. This requires time and material. Dürr’s EcoPaintJet process offers a solution, whereby the nozzles in the robot arm no longer leave overspray on the car body. Since overspray lands in unintended places, sharp edges cannot be created without a template. The EcoPaintJet nozzles hover very closely over the car body surface and work so accurately that even the tiniest paint droplets land in precisely the right place. This enables color stripes to be applied exactly side by side and with sharp edges – and the result is faster, cleaner and more economical than ever before.
Cleaning pigs
They are reminiscent of rainbows, sapphires or Sahara sand – such are the names given to special colors popular among vehicle buyers. The number of striking and unusual paints applied to passenger cars and commercial vehicles has multiplied in recent years. The models with special colors are often painted in very small series, which increases costs. Manufacturers therefore want to equip their painting lines in a way that enables special colors to be changed quickly, economically and with minimum residues in series production. For this purpose, Dürr has developed the EcoSupply P special paint supply system, which is particularly suitable for low quantities. The system uses the so-called ‘pigging technology’. Pigs are small, movable plugs which move paint through hoses. Once paint has been applied, these pigs push any residual paint back into the containers without leaving any residue, then clean the hoses. This happens faster and with substantially less paint loss than in the previous, commonly used small-ring hose systems. The entire system, from pig through to painting robot, is controlled using Dürr’s smart system technology.